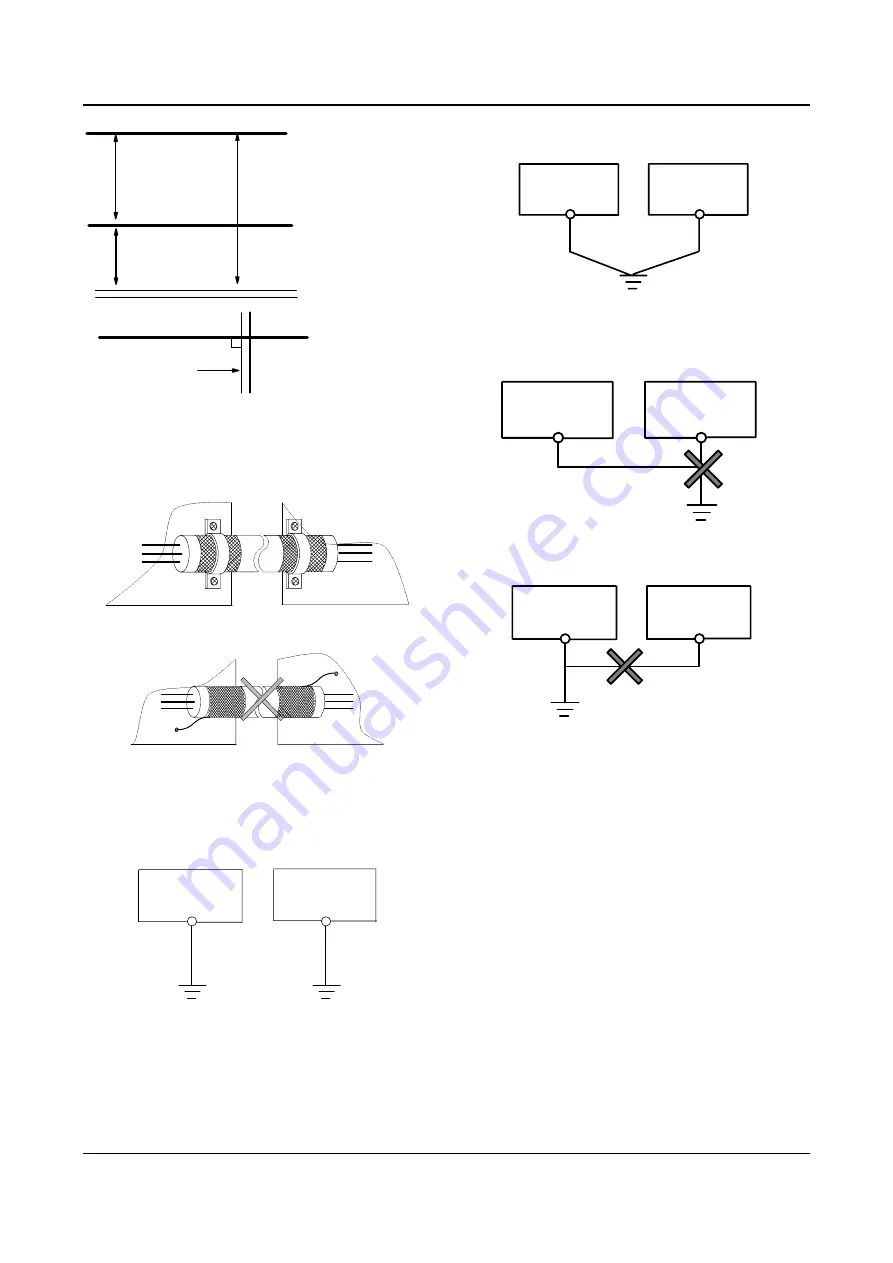
Chapter 3 Installation and Wiring 33
EV2000 Series Universal Variable Speed Drive User Manual
Power source or motor cable
Motor cable
Signal/Control cable
Power cable
Signal/Control cable
>50cm
>30cm
>20cm
Fig. 3-34 Wire connections
Generally, the control cables should be shielded cables
and the shielding metal net must be connected to the
metal enclosure of the drive by cable clamps.
PE
PE
enclosure
enclosure
Fig. 3-35 Correct shielding method of shielding layer
PE
PE
enclosure
enclosure
Fig. 3-36 Incorrect earthing method of shielding layer
3.4.3 Earthing
Independent earthing poles (best)
Drive
Other
equipment
PE
Fig. 3-37 Earthing diagram 1
Shared earthing pole (good)
Drive
Other
equipment
PE
Fig. 3-38 Earthing diagram 2
Shared earthing cable(not good)
Drive
Other
equipment
PE
Fig. 3-39 Earthing diagram 3
Drive
Other
equipment
( )
PE G
Fig. 3-40 Earthing diagram 4
Besides, pay attention to the following points:
In order to reduce the earthing resistance, flat cable
should be used because the high frequency impedance
of flat cable is smaller than that of round cable with the
same CSA.
For 4-core motor cable, the end of one cable should be
connected to the PE of the drive, and the other end
should be connected to the motor’s enclosure. If the
motor and the drive each has its own earthing pole, then
the earthing effect is better.
If the earthing poles of different equipment in one
system are connected together, then the leakage current
will be a noise source that may disturb the whole system.
Therefore, the drive’s earthing pole should be separated
with the earthing pole of other equipment such as audio
equipment, sensors and PC, etc.
In order to reduce the high frequency impedance, the
bolts used for fixing the equipment can be
used as the