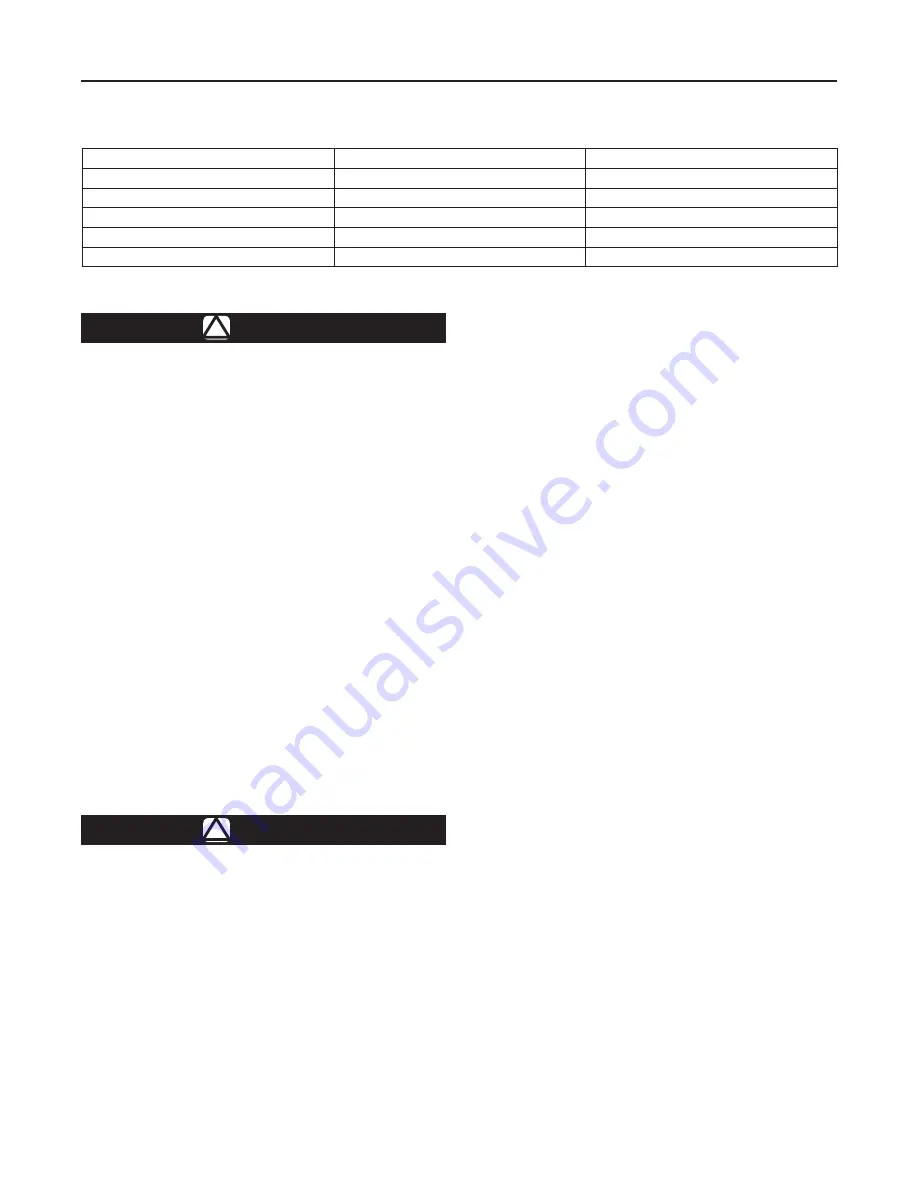
9
8 Series
DESCRIPTION
COEFFICIENT OF FRICTION
MULTIPLY TORQUE VALUE IN TABLE 5 BY
Machine Oil
f = 0.15
1.00
API SA2 Grease
f = 0.12
0.80
Never-Seez
®
(Ni base)
f = 0.11
0.73
Never-Seez
®
(Cu base)
f = 0.10
0.67
Molykote
®
G-n Paste
f = 0.06
0.40
Table 6.
Torque
Correction Factors for Common Lubricants
Molykote
®
G-n is a mark owned by Dow Corning Corporation.
Never-Seez
®
is a mark owned by Bostik, Inc.
CAUTION
Element assemblies are heavy and will
require the use of adequate equipment
and manpower to prevent injury.
3. Thoroughly clean the gasket sealing faces being
careful not to damage the sealing surface. For
reassembly, lightly grease one side of a new
gasket and place it in the machined recess of each
interior flange on the two conical sections.
4.
Replace the flame element assembly with a new
assembly or properly cleaned and inspected
existing unit.
5. Loosen the jacking nuts on the tension rods until
the flame cell assembly seats onto the gaskets.
6. Replace all tensioning studs and hand tighten the
outer nuts. Check to be sure that all the jacking
nuts are completely loose and not making contact
with the flange face.
7. Torque the bolts in sequence as shown in
Torquing Instruction.
Torquing Instruction
CAUTION
Excessive or uneven torquing can
cause permanent damage to gaskets
and housing.
Tools/Supplies Required
• Hand operated conventional torque wrench or
power assisted torque wrench appropriate for the
specified torque.
•
Socket wrenches of the proper size to fit the hex
nuts being tightened
•
Molydisulfide based lubricating paste,
Molykote
®
G-n or equivalent
• Brush suitable for applying lubricant to the studs
• Wiping rags necessary for the clean up of
excessive lubricant
Procedure
1. Use studs and nuts that are free of visible
contamination and corrosion.
2. Apply lubricant to the threads of the stud
protruding outboard of the interior flanges and
to the face of the hex nuts which will contact
the flange.
3. Assemble the nuts to the studs such that the
amount of thread extending outboard beyond the
nut is approximately equal on both ends.
4. Tighten the nuts to the torque values shown
in Table 5 following the designated sequence,
repeating the sequence as shown. Flange pattern
tightening sequences are shown in Figure 4.
Bolt Lubrication
Lubrication will affect required torque of clean
fasteners in good condition more than any other factor.
In fact, 90% of applied torque goes to overcome
friction while only 10% actually stretches the bolt.
Table 5 assumes that only machine oil is used as a
lubricant. Table 6 shows a list of several common
lubricants and their effect on torque required to stretch
bolts to 50% of their yield strength. Most are available
from local bearing distributors.