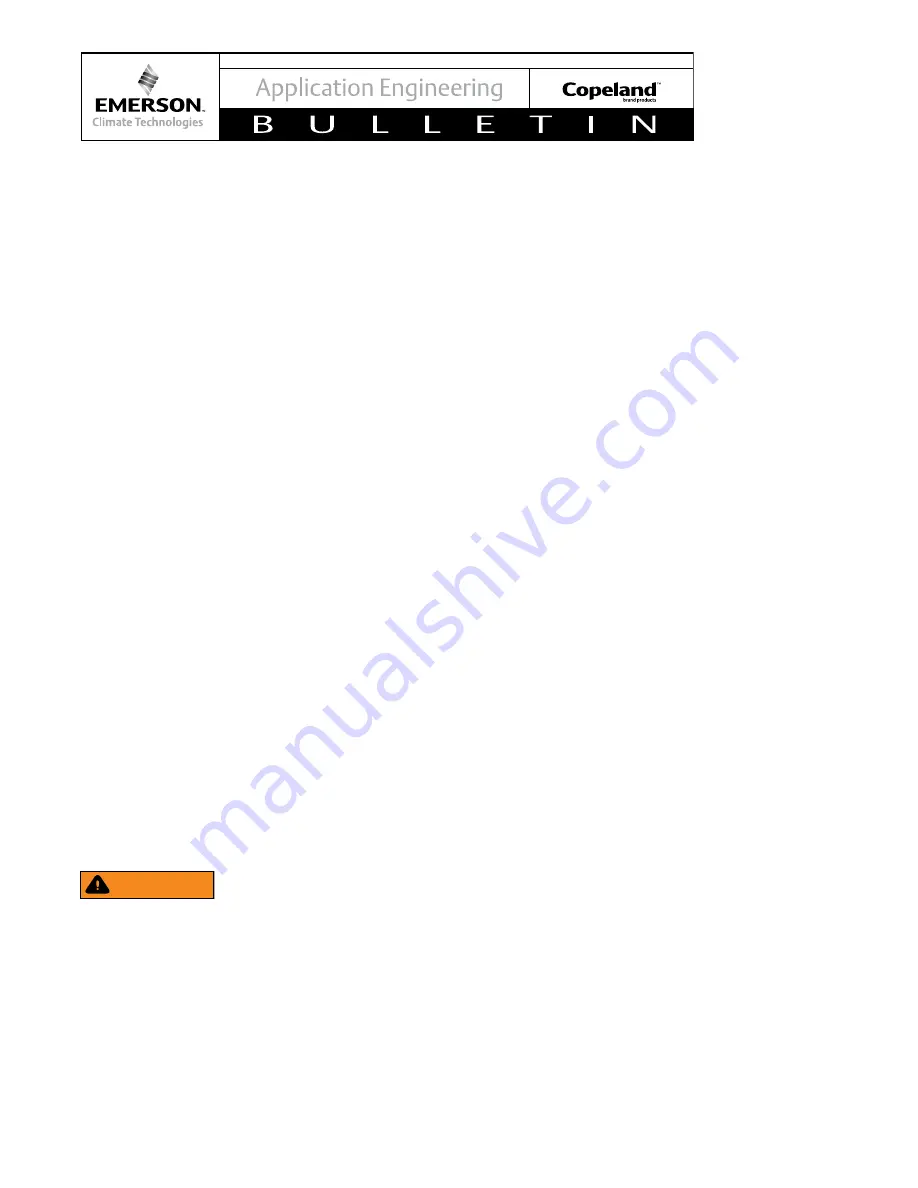
14
© 2015 Emerson Climate Technologies, Inc.
AE4-1365 R4
Copeland Scroll compressors are designed for use
with refrigerant, and testing with nitrogen may result
in a situation where the compressor does not develop
a pressure differential (no pump condition). When
testing with nitrogen, the compressor must be allowed
to cool for several minutes between tests.
Single phase scrolls with an electrical nomenclature
of “PFV” (208-230 volt, 1Ø, 60 Hertz) at the end of
the model number are guaranteed to start at 187 volts
or higher and must have a voltage no lower than 197
volts once the compressor is running under load. All
other compressor voltages, both single and three
phase, 50 & 60 Hertz are guaranteed to start and
run at 10% below the lowest voltage shown on the
nameplate.
Variable transformers used on assembly lines are often
incapable of maintaining the starting voltage when
larger compressors are tested. To test for voltage sag
during starting, the first compressor in a production
run should be used to preset the voltage. Remove the
start wire from the compressor and apply 200 volts to
the compressor. With the start winding removed, the
compressor will remain on locked rotor long enough
to read the supply voltage. If the voltage sags below
the minimum guaranteed starting voltage, the variable
transformer must be reset to a higher voltage. When
discussing this starting amperage it should be noted
that “inrush current” and locked rotor amps (LRA) are
one and the same. The nameplate LRA is determined
by physically locking a compressor and applying the
highest nameplate voltage to the motor. The amperage
that the motor draws after four seconds is the value
that is used on the nameplate. Since there is a direct
ratio between voltage and locked rotor amperage, the
lower the line voltage used to start the compressor,
the lower the locked rotor amperage will be.
Unbrazing System Components
WARNING
Before attempting to braze, it is important to
recover all refrigerant from both the high and low
side of the system.
If the refrigerant charge is removed from a scroll-
equipped unit by recovering one side only, it is very
possible that either the high or low side of the system
remains pressurized. If a brazing torch is then used
to disconnect tubing, the pressurized refrigerant and
oil mixture could ignite when it escapes and contacts
the brazing flame. Instructions should be provided
in appropriate product literature and assembly (line
repair) areas. If compressor removal is required, the
compressor should be cut out of the system rather
than unbrazed. See
Figure 7
for proper compressor
removal procedure.
SERVICE PROCEDURES
Copeland Scroll Compressor Functional Check
A functional compressor test during which the suction
service valve is closed to check how low the compressor
will pull the suction pressure is not a good indication
of how well a compressor is performing.
NOTICE
Such a test will damage a scroll compressor in
a few seconds.
The following diagnostic procedure
should be used to evaluate whether a Copeland Scroll
compressor is functioning properly:
1.
Proper voltage to the unit should be verified.
2. Determine if the internal motor overload has
opened or if an internal motor short or ground
fault has developed. If the internal overload has
opened, the compressor must be allowed to cool
sufficiently to allow it to reset.
3. Check that the compressor is correctly wired.
4. Proper indoor and outdoor blower/fan operation
should be verified.
5. With service gauges connected to suction
and discharge pressure fittings, turn on the
compressor. If suction pressure falls below normal
levels the system is either low on charge or there
is a flow blockage in the system.
6. Single phase compressors
– If the compressor
starts and the suction pressure does not drop
and discharge pressure does not rise to normal
levels, either the reversing valve (if so equipped)
or the compressor is faulty. Use normal diagnostic
procedures to check operation of the reversing
valve.
Three phase compressors
– If suction
pressure does not drop and discharge pressure
does not rise to normal levels, reverse any two of
the compressor power leads and reapply power
to make sure the compressor was not wired to
run in reverse. If pressures still do no move to
normal values, either the reversing valve (if so
equipped) or the compressor is faulty. Reconnect
the compressor leads as originally configured