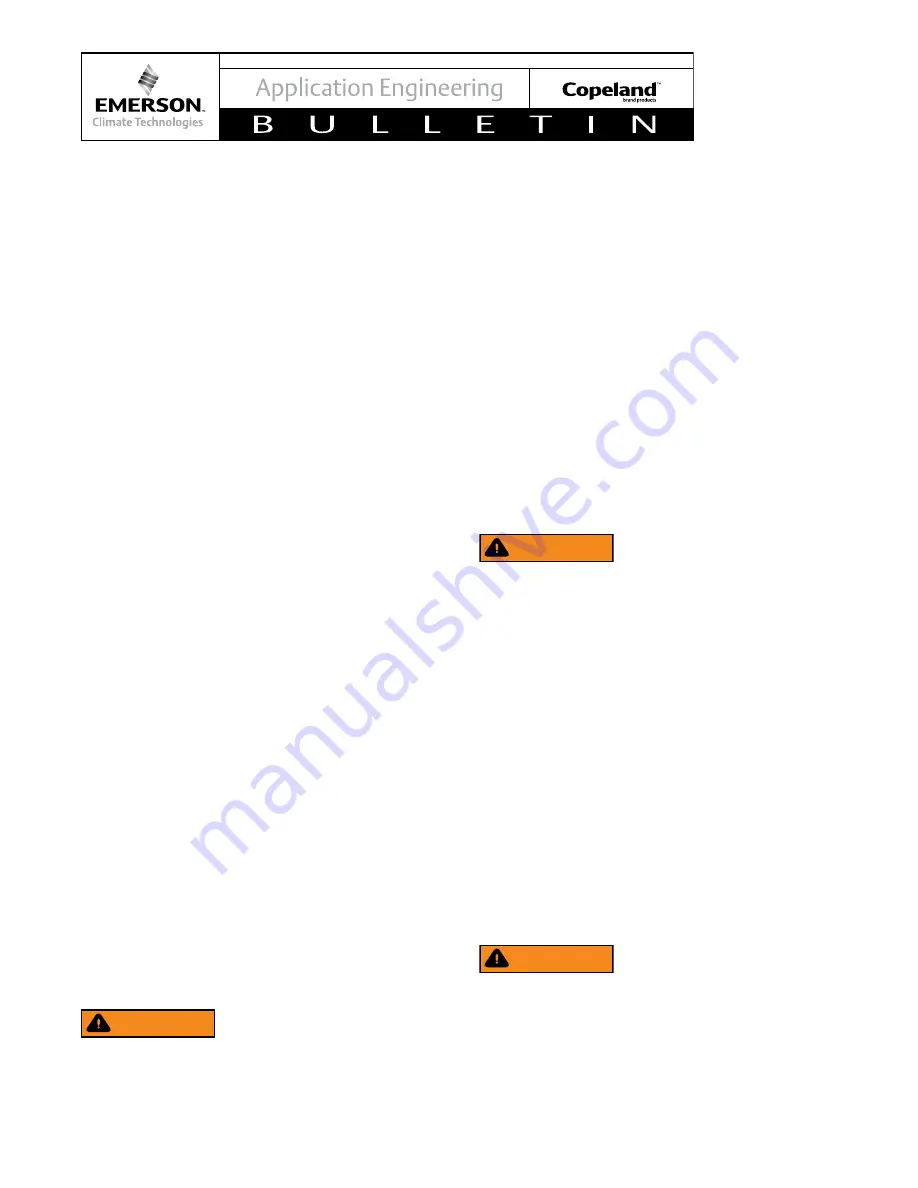
12
© 2015 Emerson Climate Technologies, Inc.
AE4-1365 R4
Field Application Test
To test for repeated, excessive liquid flood back during
normal system off-cycles, perform the
Field Application
Test
that is outlined in
Table 1
. Obtain a sample
compressor with a sight-tube to measure the liquid level
in the compressor when it is off.
Note: The sight-tube is not a good liquid level indicator
when the compressor is running because the top of the
sight-tube is at a lower pressure than the bottom causing
a higher apparent oil level.
Set the system up in a configuration with the indoor
unit elevated several feet above the outdoor unit with
a minimum of 25 feet (8 meters) of connecting tubing
with no traps between the indoor and outdoor units. If
the system is designed to be field charged, the system
should be overcharged by 15% in this test to simulate
field overcharging. Operate the system in the cooling
mode at the outdoor ambient, on/off cycle times, and
number of cycles specified in
Table 1
. Record the height
of the liquid in the compressor at the start of each on
cycle, any compressor overload trips, or any compressor
abnormal starting sounds during each test. Review
the results with Application Engineering to determine
if an accumulator or other means of off cycle migration
control are required.
This test does not eliminate the
requirement for a crankcase heater if the system
charge level exceeds the values in Table 3
. The
criteria for pass/fail is whether the liquid level reaches
the level of the compressor suction tube connection.
Liquid levels higher than this can allow refrigerant/oil
to be ingested by the scrolls and pumped out of the
compressor after start-up.
The tests outlined above are for the common
air conditioning and heat pump applications of
compressors in this family. Many other applications
of the compressors exist, and tests to effectively
evaluate those applications and designs can’t
possibly be covered in this bulletin. Please consult
with Application Engineering on applications
outside of those outlined above for the appropriate
application tests.
ASSEMBLY LINE PROCEDURES
Installing the Compressor
WARNING
Use care and the appropriate material handling
equipment when lifting and moving compressors.
Personal safety equipment must be used.
Copeland Scroll compressors leave the factory
dehydrated, with a dry air holding charge. If compressors
are stored in a cold ambient (i.e. outside during the
winter), the suction and discharge plugs should not
be removed until the compressor has had sufficient
time to warm up to the plant ambient temperature.
The suggested warm up time is one hour per 4°F (2K)
difference between outdoor and indoor temperature. It
is suggested that the larger suction plug be removed
first to relieve the internal pressure. Removing the
smaller discharge plug could result in a spray of oil out
of this fitting since some oil accumulates in the head
of the compressor after Emerson’s run test. The inside
of both fittings should be wiped with a lint free cloth
to remove residual oil prior to brazing. A compressor
containing POE oil should never be left open longer
than 20 minutes.
Assembly Line Brazing Procedure
WARNING
Personal safety equipment must be used during
brazing operation. Heat shields should be
used to prevent overheating or burning nearby
temperature sensitive parts. Fire extinguishing
equipment should be accessible in the event of a
fire.
Figure 7
discusses the proper procedures for brazing
the suction and discharge lines to a scroll compressor.
NOTICE
It is important to flow nitrogen through the
system while brazing all joints during the system
assembly process.
Nitrogen displaces the air and
prevents the formation of copper oxides in the system.
If allowed to form, the copper oxide flakes can later
be swept through the system and block screens such
as those protecting capillary tubes, thermal expansion
valves, and accumulator oil return holes. Any blockage
of oil or refrigerant may damage the compressor
resulting in failure.
Tandem Assembly
WARNING
When lifting tandem compressor assemblies,
both compressors must be lifted by their
respective lifting rings. Use care and exercise
extreme caution when lifting and moving
compressors. Personal safety equipment must
be used.