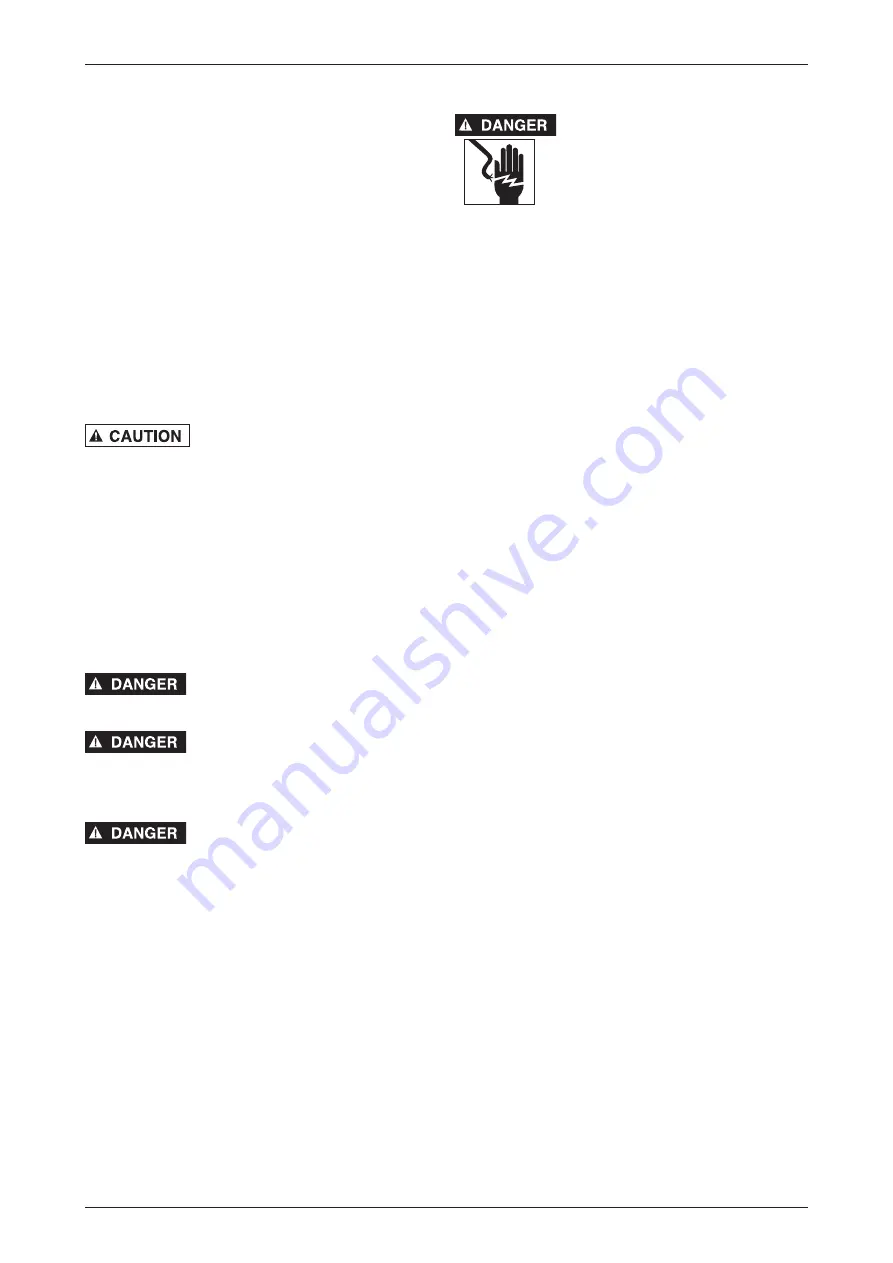
6
HULK Power
safety glasses. Everyday eyeglasses are NOT
safety glasses. Dust mask, non-skid safety
shoes, hard hat, or hearing protection should
be used in appropriate conditions.
2. Wear proper apparel.
Loose clothing, gloves, neckties, rings,
bracelets, or other jewelry may present a
potential hazard when operating this tool.
Please keep all apparel clear of the tool.
Installation
Area
1. Install compressor in a clean, dry and well-lit
area. Be sure installation area can maintain a
temperature range between 35° - 110° F (2° -
43° C).
2.
Do not use below garage floor or grade level
If ambient temperature drops
below 32˚F (0° C), be sure to
protect safety/relief valves and drain valves from
freezing. NEVER operate compressor with
temperatures below 15˚F (-9.5° C) or above 125˚F
(52° C).
3.
Allow sufficient space around compressor for
maintenance access and adequate airflow.
Mount unit leaving a minimum of 15 inches (38
cm) of clearance.
4. Use 1/4" rubber shims to level compressor
if installation area is not flat. This will avoid
excessive vibration and premature pump wear.
DO NOT use shims thicker than
1/4". Thicker shims can cause
tank damage.
DO NOT install compressor in
boiler room, paint spray room, or
area where sandblasting occurs. Make sure inlet
air is away from exhaust fumes or other toxic,
noxious or corrosive fumes or substances.
RISK OF FIRE OR EXPLOSION
– do not spray combustible/
flammable liquid in a confined area. spray area
must be well ventilated. do not smoke while
spraying or spray where spark or flame is
present. arcing parts – keep compressor at least
20 feet away from spraying area and all explosive
vapors.
5. If acid is used in operating environment or air
is dust laden, pipe intake to outside, fresh air.
Increase pipe size by one size for every 20
feet of run. Be sure to install protective hood
around intake filter.
6. Insulate cold water or other low temperature
pipes that pass overhead to avoid
condensation dripping on compressor which
could cause rust and/or motor shorting.
Electrical Safety
Be sure only trained and
authorized personnel maintain
this compressor in accordance
with all applicable federal, state
and local codes, standards and
regulations. Follow all NEC
(National Electric Code) standards especially
those concerning equipment grounding
conductors.
1. Follow all NEC and local codes for electrical
wiring. Allow only authorized Polar Air service
person or certified electrician to install
electrical components.
2. Put unit on dedicated circuit and make sure
no other electrical equipment is wired into it.
Failure to wire unit on independent circuit can
cause circuit overload and/or imbalance in
motor phasing. Install proper No Fuse Breaker
(NFB) according to kW output of compressor.
3. Ensure incoming service has adequate
ampere rating.
4. Ensure supply line has the same electrical
characteristics (voltage, cycles and phase) as
the electric motor.
5. Refer to amp load information on the
specifications label and use correctly sized
wiring. Be sure to consider distance between
power supply and machine.
6. Install surge protection device between power
supply and compressor motor.
7. Make sure to install properly sized breakers
and fuses.
8. The unit must be properly grounded. DO NOT
connect ground wire to air or cooling lines.
9. If the tool is equipped with three-pin plug, it
should be plugged into a three-pin electrical
socket. Never remove the ground pin.
10. Avoid body contact with grounded surfaces
such as pipes, radiators, ranges, and
refrigerators. There is an increased risk of
electric shock if your body is grounded.
11. To reduce the risk of electrical shock or injury,
do not expose tool to moisture.
Don’t use this tool in damp or wet locations.
Keep out of rain.
12. Do not abuse cord.
Never use the cord to carry tools or pull the
plug from an outlet. Keep cord away from
heat, sharp edges or moving parts. Check
for damage and replace damaged cords
immediately before connecting to power
supply. Damaged cords increase the risk of
electric shock.