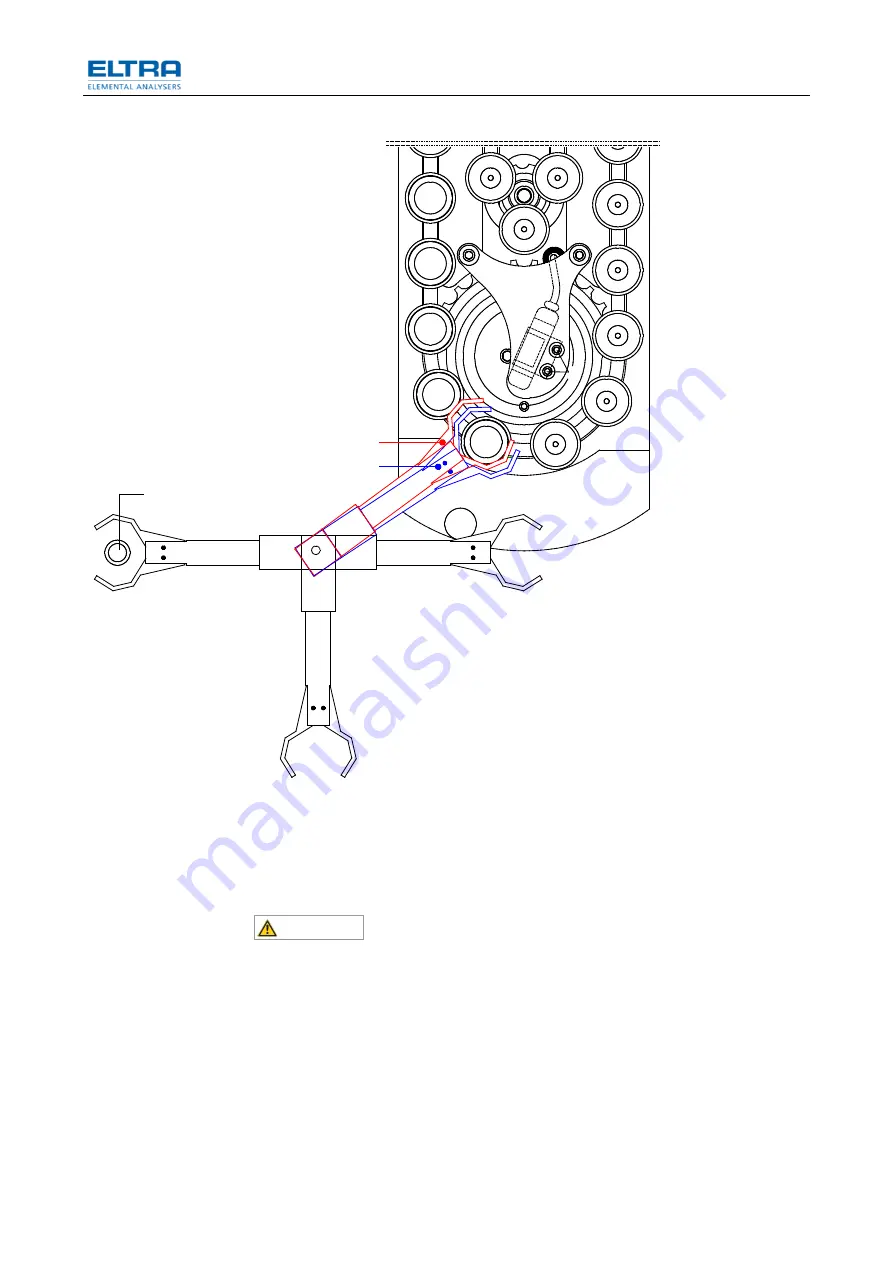
Operating the machine
17
Fig. 16: Loader steps
•
Press the adjust button (5) of image pneumatic connections again for only
about one second.
Now the horizontal laser (6) for sensing the position of the crucibles (1 to 4) is
continuously ON. This can be seen by looking at the sensor (7) in front of the laser
(6).
CAUTION
Don’t look directly into the laser beam.
If the laser (6) is ON and there is no beeping to hear, it means that the sensor (7) is
sensing the laser beam. For this, make sure that there is no crucible or anything
else between the laser (6) and the sensor (7) preventing the beam from reaching
the sensor (7).
•
Interrupt the beam between the laser (6) and the sensor (7) to verify the
correct functioning of detector and beeper.
If the laser (6) is ON and the beeper is beeping, although the beam is not
interrupted, this means that the beam doesn’t hit the detector (7). The beeper
signalises this condition. In this case the laser (6) should be mechanically adjusted
6
7
9
8
1
4
3
J
H o m e p o si t i o n
P e d e s t a l
P a r ki n g
p o s i t i o n
D i s p o sa l
p o s i t i o n
P i ck u p p si t i o n
pi ck
up
2
Содержание CS-800
Страница 2: ...2 Copyright Copyright by Eltra GmbH Haan Retsch Allee 1 5 D 42781 Haan Federal Republic of Germany ...
Страница 3: ...3 ...
Страница 13: ...Operating the machine 13 Fig 13 Electrical circuit 14621 6001 3 4 1 5 6 2 ...
Страница 25: ......
Страница 26: ......
Страница 27: ......
Страница 28: ...Copyright Copyright by Eltra GmbH Haan Retsch Allee 1 5 D 42781 Haan Federal Republic of Germany ...