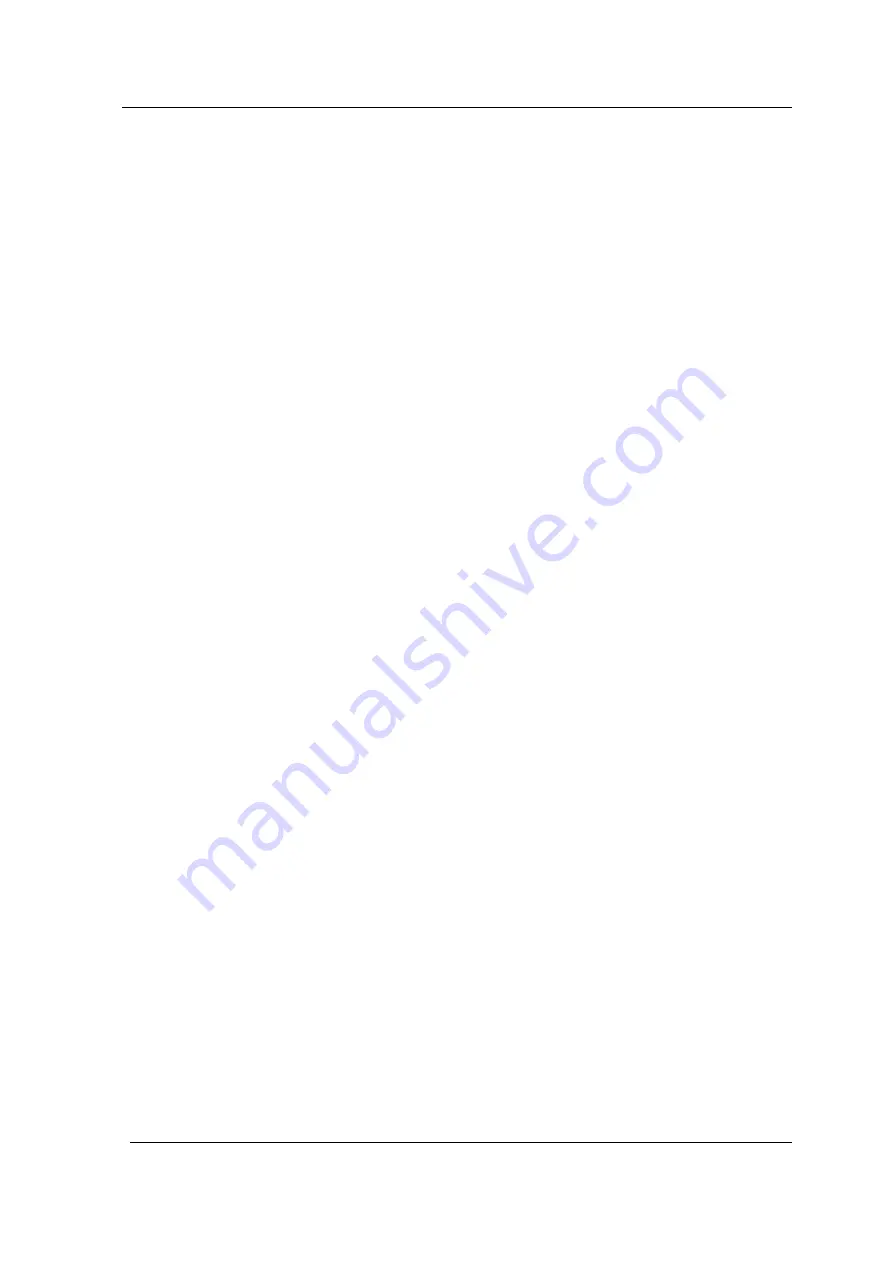
Cleaning media
30
BA_ES xtra ST_EN_Vers.08.2016
© Elma Schmidbauer GmbH
8.2
Limitations on aqueous cleaners
Do not use aqueous cleaning media with pH values in the acid
range (pH < 7) directly in the ultrasonic tank if fluoride (F
ˉ),
chloride (Clˉ) or bromide (Brˉ) ions can be taken in by the
removed dirt or through the cleaning chemical. These can
destroy the stainless-steel tank by crevice corrosion within a
very short period of ultrasonic operation.
Other media which can destroy the stainless-steel tanks when
used in high concentrations or with high temperatures during
ultrasonic operation are: hydrochloric acid, nitric acid, sulphuric
acid, formic acid, hydrofluoric acid (even diluted).
(Completeness of list not guaranteed.)
Examples:
Treatment with hydrochloric acid or hydrofluoric acid, or acid
solution salts
Removal of fluxing agents containing fluoride, chloride or
tetrafluoroborate from soldered metal parts or electronic
components
Decalcification, in a solution containing citric acid, of
medical systems which are contaminated by physiological
saline
Risk of damage to the unit: do not use cleaning solutions
containing more than 0.5 mass % alkali (KOH and/or NaOH) in
an ultrasonic cleaning tank.
Potassium hydroxide solution will cause stress cracks in the
ultrasonic tank.
The above limitations for the use of chemicals in an ultrasonic
bath also apply for the aforementioned chemicals when these
are brought into an aqueous (particularly distilled water) bath
through entrainment or from the removed dirt.
Examples:
Ultrasound-aided rinsing of items which have been etched
by hydrofluoric acid or ammoniumbifluoride.
The limitations of use also apply to the standard cleaners and
disinfectants if these contain the above mentioned compounds.
For the ultrasonic treatment with the above mentioned media
use an acid-resistant tank.
Please contact your supplier for available accessory equipment.
Observe the safety warnings indicated by the manufacturer of
the chemicals (e.g. goggles, gloves, R and S phrases).
For queries please contact the manufacturer or your supplier.
No liability can be accepted for any damage caused by non-
observance of the instructions and limitations stated in
Sections 8.1
Acids
Alkaline solutions
KOH
Entrainment of
chemical substances
Disinfectants
Acid-resistant tank
Safety regulations
Exclusion of liability