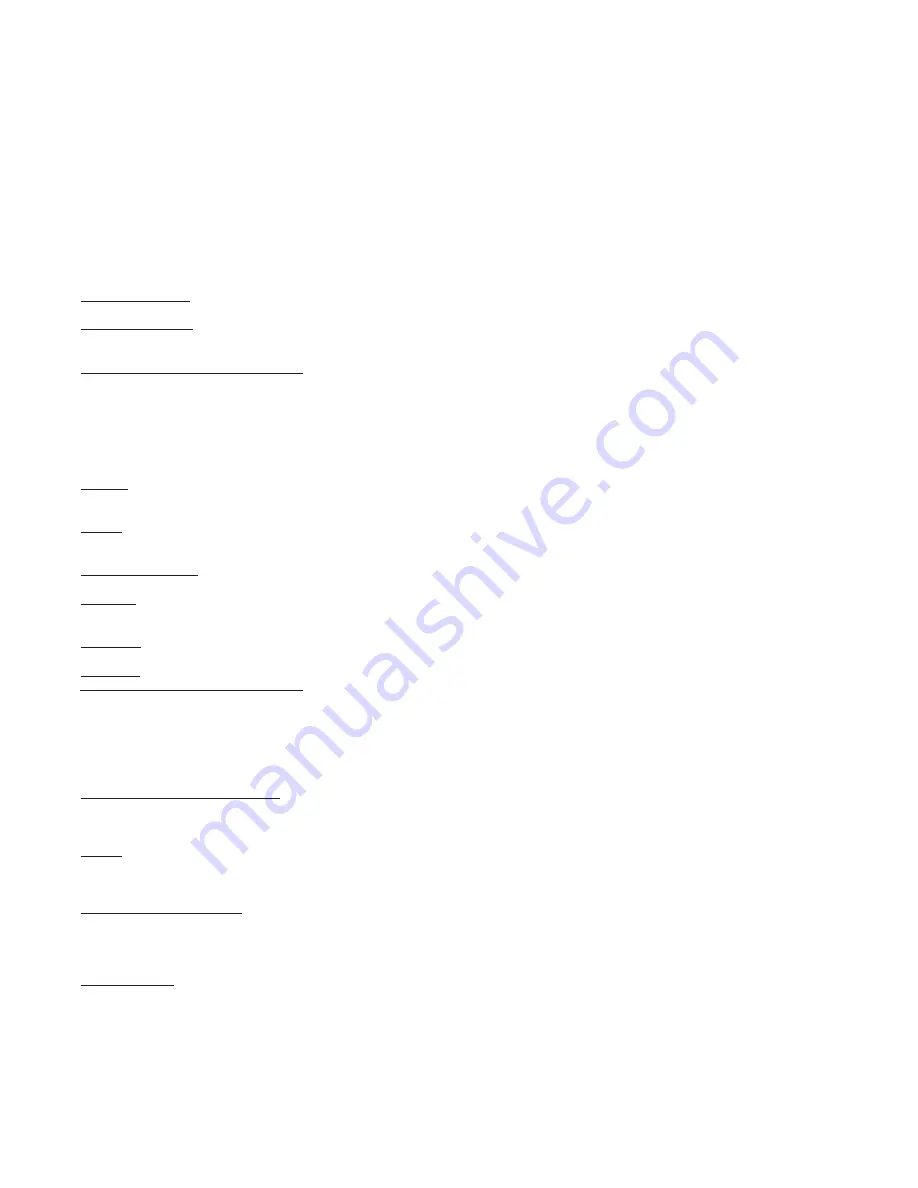
Page 6
LZSTL8WS_2D
1000002481 (Rev. C - 11/15)
Service
For proper and safe servicing, please read these instructions completely.
DANGER
• All Service and Maintenance must be performed by an authorized service personnel.
• Disconnect electrical supply to the unit before any service work to reduce risk of electrocution.
• Shut off water supply serving the unit before any service work to reduce risk of water damage.
CAUTION
• Tools/Items required but not provided, for Servicing:
o Safety Glasses
o Protective gloves
o 5/16” (8mm) Hex Socket or Flathead Screwdriver
o 5/32” (4mm) Hex Key
Service: Adjustments
1. Temperature Control: Factory set for 50ºF ± 5º (10ºC ± 2.8º) water under normal conditions. To adjust water temperature, turn screw on Item
No. 13 clockwise for colder, counter clockwise for warmer.
2. Water Stream Height: Stream height is factory set at 35 psig (0.24 MPa). If supply pressure varies greatly from this, adjust screw located on
the left side below push bar assembly on crossbar. Clockwise adjustment will raise stream and Counterclockwise adjustment will lower
stream. For best adjustment, stream should hit basin approximately 6-1/2” (165mm) from bubbler on the downward slope of the basin.
3. Water coming out of Bubbler continuously: When this occurs at the end of the compressor cycle, turn the cold control warmer
(counterclockwise) ¼ turn.
Service: Inspection/Cleaning
• Inspect Cooler twice each year for proper operation and performance.
• Inspection of the unit will require disconnecting electrical supply, removal of panels, etc. and reassembly and return to service
practices.
1.
Cleaning
: Warm, soapy water or mild household cleaning products can be used to clean the exterior panels. Extra caution should be used
to clean the mirror finished stainless steel panels. They can be easily scratched and should only be cleaned with mild soap and water or
Windex glass cleaner and a clean, soft cloth. Use of harsh chemicals or petroleum based or abrasive cleaners will void the warranty.
2. Bubbler: Mineral deposits on the orifice can cause water flow to spurt or not regulate. Mineral deposits may be removed from the orifice with
a small round file not over 1/8” (3 mm) diameter or small diameter wire.
• CAUTION : DO NOT file or cut orifice material. Care must be taken not to damage the orifice(s)
3. Condenser Fan Motor: Confirm condenser fan turns freely. If the condenser fan does not spin freely, have an authorized service personnel
replace.
4. Ventilation: Cabinet louvers and condenser fins should be periodically cleaned with a brush, air hose or vacuum cleaner. Cleaning should be
done twice each year or more frequently if needed due to environment. Excess dirt or poor ventilation can cause no cold water and
compressor cycling on the compressor overload protector.
5.
Water Flow
: Confirm proper water flow. If water flow is slow, inspect filter or inline strainer for restriction. Replace filter cartridge if required.
Disassemble inline strainer and clean if required.
6. Lubrication: Motors are lifetime lubricated.
7. Actuation of Quick Connect Water Fittings: Cooler is provided with lead-free connectors which utilize o-ring water seal. To remove tubing
from the fitting, relieve water pressure, push in on the gray collar before pulling on the tubing. To insert tubing, push tube straight into fitting
until it reaches a positive stop, approximately 3/4” (19mm). See Figure 10.
Service: Inspection/Replacement
• Inspect Cooler twice each year for proper operation and performance.
• Inspection of the unit will require disconnecting electrical supply, removal of panels, etc. and reassembly and return to service practices.
1. Lower Front Panel and Upper Shroud: To access the refrigeration system and plumbing connections, remove four (4) screws from bottom of
cooler to remove the lower front panel. To remove the upper shroud (Item 6) for access to the pushbars, regulator, solenoid valve or other
components located in the top of the unit, remove lower panel, disconnect drain, remove four screws from tabs along lower edge of upper
shroud, unplug two wires and water tube.
2. Bubbler: To remove the bubbler, first disconnect the electrical supply. The underside of the bubbler can be reached through the access panel
on the underside of the upper shroud. Remove the access panel by removing the retaining screw. To remove the bubbler, loosen locknut from
the underside of the bubbler and remove the tubing from the quick connect fitting (see Figure 10). When installing replacement bubbler and
pedestal, tighten nut only to hold parts snug in position. Do Not Overtighten. After servicing, replace the lower front panel and four (4) screws.
3. Switches Behind the Push Bar: The regulator in an EZ cooler is always held fully open by the use of a single regulator nut. Water is not
dispensed until the pushbar is depressed to activate a switch which then opens a solenoid valve. When installing the regulator nut, the
regulator spring must be depressed while turning the nut. Single bar units will have the same wiring as side push bar units but will not have
the extra leads attached to sidebars. To remove sidebars, from the inside compress the flared tabs and pull out carefully. To reinstall side
pushbars, the front of the pushbar is inserted first. While keeping the switch depressed, snap the rear of the pushbar into position.
4. Cleaning Strainer: To clean the strainer, unscrew the cap of the solenoid valve. Remove screen and rinse thoroughly with water. Insert screen
back into solenoid valve and screw cap on. Make sure the o-ring is placed properly.