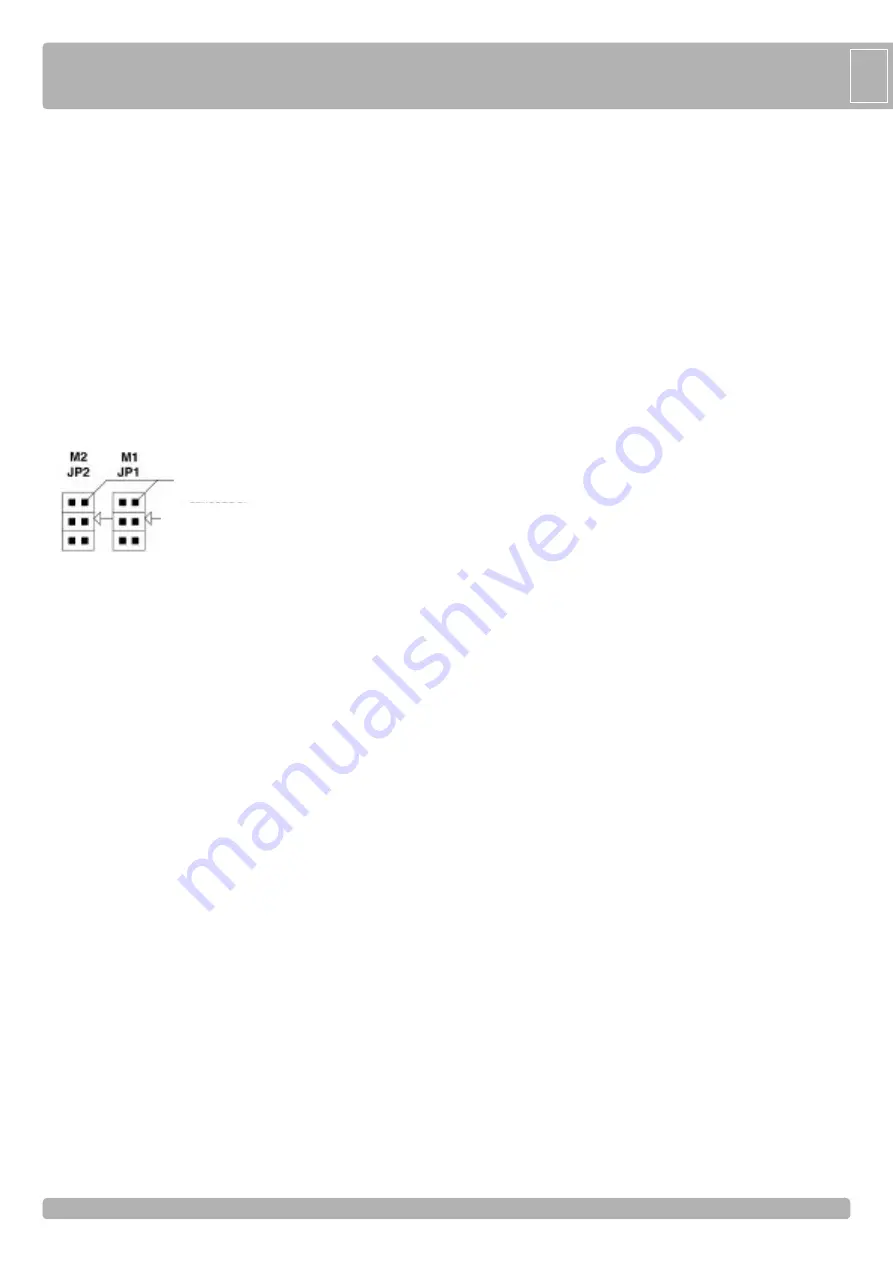
31
31
C
- CHECKING THE ROTATION DIRECTION OF THE
MOTOR
This control facilitates installation of the system and allows further
checks to be performed.
1 - Switch DIP 1 to ON. Led DL7 starts blinking.
2 - Depress and maintain the pushbutton PROG (movement is obtained
with the presence of the operator, open-stop-close-stop-open-etc)
=> RED LEDS DL9 and DL10 lit and the gate leaves close with a
fixed timing difference of 4 sec. In case of misfunctioning release
the button and change over the two wires of affected motor.
3 - Depress and maintain the pushbutton PROG => GREEN LEDS DL8
e DL11 lit and the gate leaves open with a fixed timing difference of
2 sec.
4 - Set the mechanical stop devices for opening (installed on the
actuator).
5 -
ONLY IF INSTALLING ACTUATORS WITHOUT ENCODER,
PERFORM SETTING OF THE CURRENT SENSORS
otherwise
carry on the next step.
Select first the type of sensor through connectors JP1 and JP2. For
a correct setting rotate the trimmer fully clockwise (+), maintain
depressed the pushbutton PROG and as the gate leaves get to the
mechanical stop operate the trimmers M1 and M2 to locate the
switching treshold of the current sensors. Operation of the current
sensor is shown by the led DL3 lit for motor 2 and DL4 for motor 1.
The test can be repeated as desired both with gate fully open and
closed.
6 - Drive the two leaves to full closure, preparing for time setting.
7 - At the end of the procedure, switch DIP1 to OFF. LED DL7 goes off
to confirm exit from the check procedure.
N.B. During this check, the encoder and photocells are not active.
D
- TIME PROGRAMMING (#)
THIS CAN BE DONE IN EITHER OF TWO WAYS:
MODE 1 - WITH ENCODER (DIP 7 ON )
MODE 2 - WITH CURRENT SENSOR (DIP 7 OFF)
MODE 1
1 - Start with the gate completely closed and with mechanical stopper
already regulated like fig.10.
2 - Switch DIP 2 to ON => LED DL7 will blink rapidly.
3 - Press PROG. => M1 opens.
4 - When the gate comes into contact with the opening stop, the
ENCODER stops M1 (with storage of the encoder readings and the
time) and M2 starts to open simultaneously.
5 - When the gate comes into contact with the opening stop, the
ENCODER stops M1 (with storage of the encoder readings and the
time) => the delay countdown prior to automatic closing starts
simultaneously (max 5 minutes).
6 - Press PROG. => delay countdown prior to automatic closing stops
and M2 closes.
7 - Press PROG. => M1 closes and creates a phase difference
between M2 and M1. At the same time LED DL7 stops blinking to
signal exit from the programming mode. At this point, the safety
devices and other gate controls will resume normal operation
(inversions, stops, alarms, etc.).
8 - Leaves closure is carried in quick mode, reverting to slow mode in
proximity of the travel end.
9 - On completion of ENCODER measurement the gate stops.
AFTER PROGRAMMING, SWITCH DIP 2 TO OFF.
MODE 2
1 - Start with the gate completely closed.
2 - Switch DIP 2 to ON => LED DL7 will blink rapidly.
3 - Press PROG. => M1 opens.
4 - When the gate comes into contact with the opening stop, the
CURRENT SENSOR stops M1 (with storage of the time) and M2
starts to open simultaneously.
5 - When the gate comes into contact with the opening stop, the
CURRENT SENSOR stops M2 (with storage of the time) and the
delay countdown prior to automatic closing starts simultaneously
(max 5 minutes).
6 - Press PROG. => delay countdown prior to automatic closing stops
and M2 closes.
7 - Press PROG. => M1 closes and creates a phase difference
between M2 and M1. At the same time LED DL7 stops blinking to
signal exit from the programming mode. At this point, the safety
devices and other gate controls will resume normal operation
(inversions, stops, alarms, etc.).
8 - Leaves closure is carried in quick mode, reverting to slow mode in
proximity of the travel end.
9 - Upon closure through the current sensors the gate stops.
AFTER PROGRAMMING, SWITCH DIP 2 TO OFF.
(#) SAFETY DEVICES ARE ACTIVE DURING THE PROGRAMMING
AND THEIR INTERVENTION STOPS IT (THE LED 7 BLINKS NO
MORE BUT REMAINS CONSTANTLY TURNED ON). TO REPEAT
THE PROGRAMMING SET DIP 2 OFF (IF IN NORMAL MODE) OR
DIP 1 AND DIP 2 OFF (IF IN PEDESTRIAN MODE), CLOSE THE
GATE ACCORDING TO THE PROCEDURE “VERIFICATION OF
MOTORS DIRECTION OF ROTATION” AND REPEAT THE
PROGRAMMING AS DESCRIBED ABOVE.
O
PERATION OF THE OPERATING ACCESSORIES
OPENING BUTTON (with timer function)
When the gate is standstill, the button operates the opening mode. If
you push this button when the gate is on closure, It opens again.
TIMER FUNCTION
This function is useful In the rush hours, when vehicle traffic is slow
(e.g. entry/exit of workers, emergencies In residential or parking areas
and, temporary, for removals).
APPLICATIONS
By connecting a switch and/or a daily/weekly timer (in place or in
parallel with the opening button N.O. “COM-OPEN”), it is possible to
open the automation or to keep It open, as long as the switch is on or
the timer is activated.
When the automation is open, all operating functions are inhibited.
If the automatic closing Is started, by releasing the switch or at the time
set before, the automation immediately closes; if not, you need to
operate a command.
CLOSING BUTTON (COM-CLOSE)
When the gate Is standstill, It operates the closing.
JOGGING OPERATION BUTTON (COM-K BUTTON)
DIP5 - OFF =>
It cyclically commands open-stop-close-stop-open-etc.
DIP5 - ON =>
It opens the gate when this Is closed. If It Is operated
while the gate Is opening, It has no effect. If It Is operated
when the gate is open, it closes the gate and, If It Is
operated while the gate Is closing, It opens the gate
again.
Dip position for PRINCE with Encoder
DIP 7 ON - Current sensors Off / Encoder On
Dip position for PRINCE with Current sensors
DIP 7 OFF - Current sensors On / Encoder Off
GG
BB