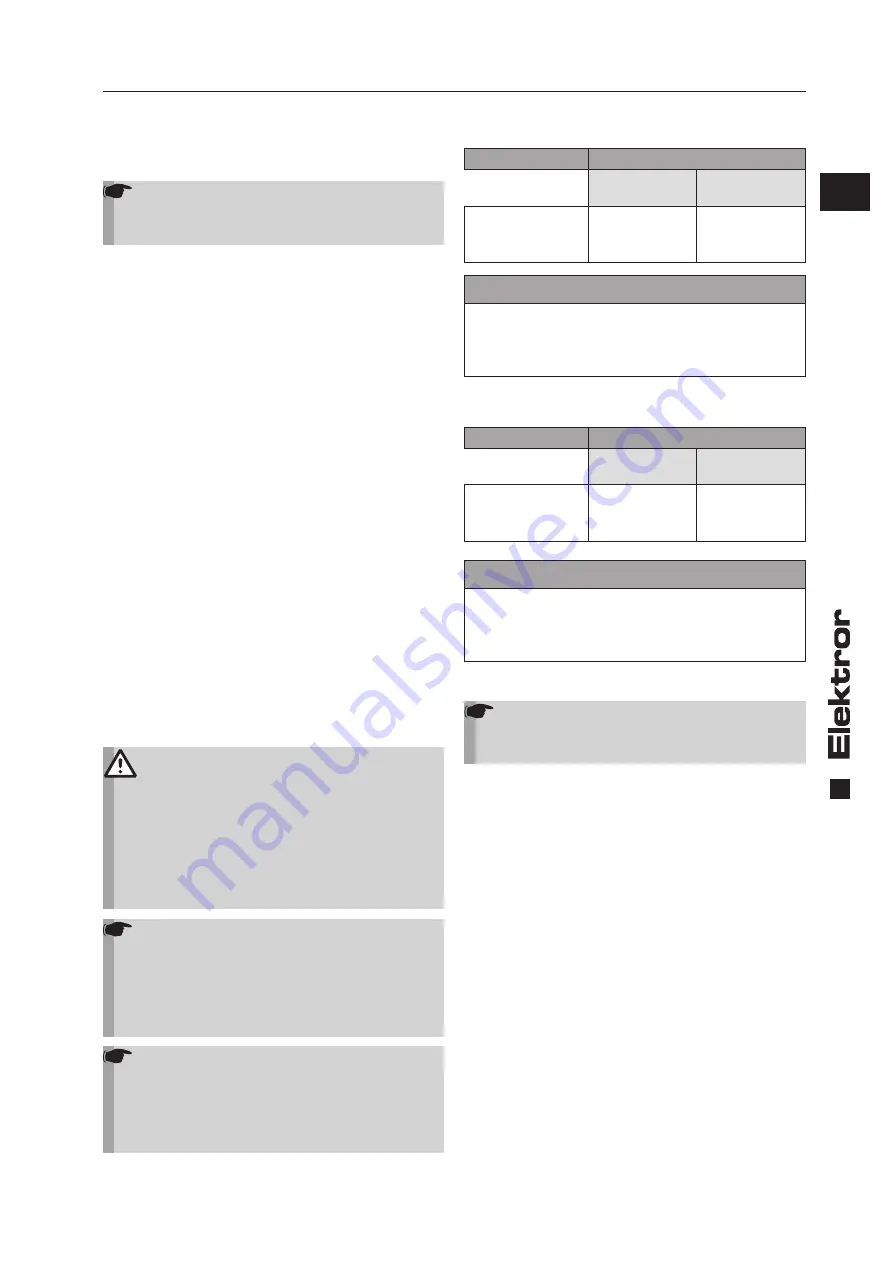
21
EN
Operating and assembly instructions ND ATEX
www.elektror.com
9016324 01.20/09
Immediate inspection and maintenance
The blower must be inspected immediately if vibrations or
reduced air
fl
ow are observed.
Note!
We recommend to have repairs carried out by the
manufacturer. We cannot accept any liability for
repairs carried out by third parties.
Perform the following tasks in course of every inspec-
tion/maintenance job as well as upon repair and replace-
ment of parts:
• Visually inspect all movable parts of the blower, such as
impeller, blower housing cover / intake nozzle for possible
damage, scoring, wear,
fi
ssures, cracks, deformation;
proper condition of all earthing connections, radial shaft
seals etc.
• Inspect the gap between the impeller nozzle and the intake
nozzle at the blower cover.
ATEX machine type D 09, D 092:
Minimum gap 3.0 mm
All other ND ATEX machine types:
Minimum gap 2.0 mm
• If ATEX blowers are stored for replacement, note that some
components installed have a limited storage life. This espe-
cially applies to the ball bearings, e.g. concerning the life
of the grease lubrication. The storage life depends on the
type of storage and the unit type as well as on the conditions
and duration of storage of the Elektror product. Type-related
information can be acquired from Elektror product manage-
ment.
• Inspection and service work must be documented chrono-
logically and fully stating the name of the person responsi-
ble. In particular, operating errors, measures implemented
as well as compliance with all applicable regulations and the
manufacturer’s speci
fi
cations must be documented. It is rec-
ommended that this documentation be kept in a report book
and safely stored.
5.3 Ball bearings
Danger!
Risk of injury and property damage posed by
improper handling!
The risk of injury and property damage increases
considerably if the device is handled incorrectly.
Explosions and the property damage and phy-
sical injuries resulting from them are the conse-
quence.
Only authorised specialist workshops with
approval are allowed to perform repairs to ATEX
devices.
Note!
The ball bearings are to be checked during each
instance of service and prior to each instance of
commissioning.
Operation is only permitted with
fl
awless ball
bearings!
Refer to the supplier‘s documentation of the ATEX
motor manufacturer for further notes.
Note!
In the event of frequently starting up and shutting
down, premature replacement of the bearings will
be required. Determining the time for replacing
the bearings is the sole responsibility of the main-
tenance and servicing personnel, who must make
a safety judgement.
Motor company CEMP
Devices
Minimum ball bearing service life
Horizontal motor
shaft
Vertical motor
shaft
ND ATEX range
20.000 Hours
Reduction of ball
bearing service
life
Ball bearing change recommendation
- Prior to reaching the minimum service life
- 30 months following delivery at the latest
- Check after 6 months’ storage time; change if necessary
Motor company VEM
Devices
Minimum ball bearing service life
Horizontal motor
shaft
Vertical motor
shaft
ND ATEX range
20.000 Hours
Reduction of ball
bearing service
life
Ball bearing change recommendation
- Prior to reaching the minimum service life
- 30 months following delivery at the latest
- Check after 6 months’ storage time; change if necessary
Other motor manufacturers
Note!
Refer to the supplier‘s documentation of the res-
pective motor manufacturer for further notes for
other motor manufacturers.
5.4 Seals and Radial Shaft Sealing Rings
For safety reasons, sealing elements and radial shaft seals
must be replaced at least in course of every maintenance work,
repair or replacement of parts, which requires that sealing el-
ements are opened, remove or otherwise manipulated. The
equipotential bonding must be inspected in conjunction with
every maintenance job and shall be in good operating order af-
ter the maintenance job is completed. The measures must not
lead to interconnections between explosion protection zones.
The radial shaft seals must be in perfect condition; this must
be checked during all maintenance work.
5.5 Micro-
fi
lters
The degree of clogging of the
fi
lter mats should be checked
at regular intervals, depending on the ambient conditions /
conditions of use. This means that the user is responsible for
ensuring that the
fi
lters are permeable.
5.6 ATEX Impeller
The balancing as well as the lateral and radial travel of the
impeller may not be impaired as a consequence of mainte-
nance/service, repair or replacement of parts.
The impeller must be replaced at the latest when clearly de-
tectable vibration occurs, or when mechanical wear or dam-
age is visible.