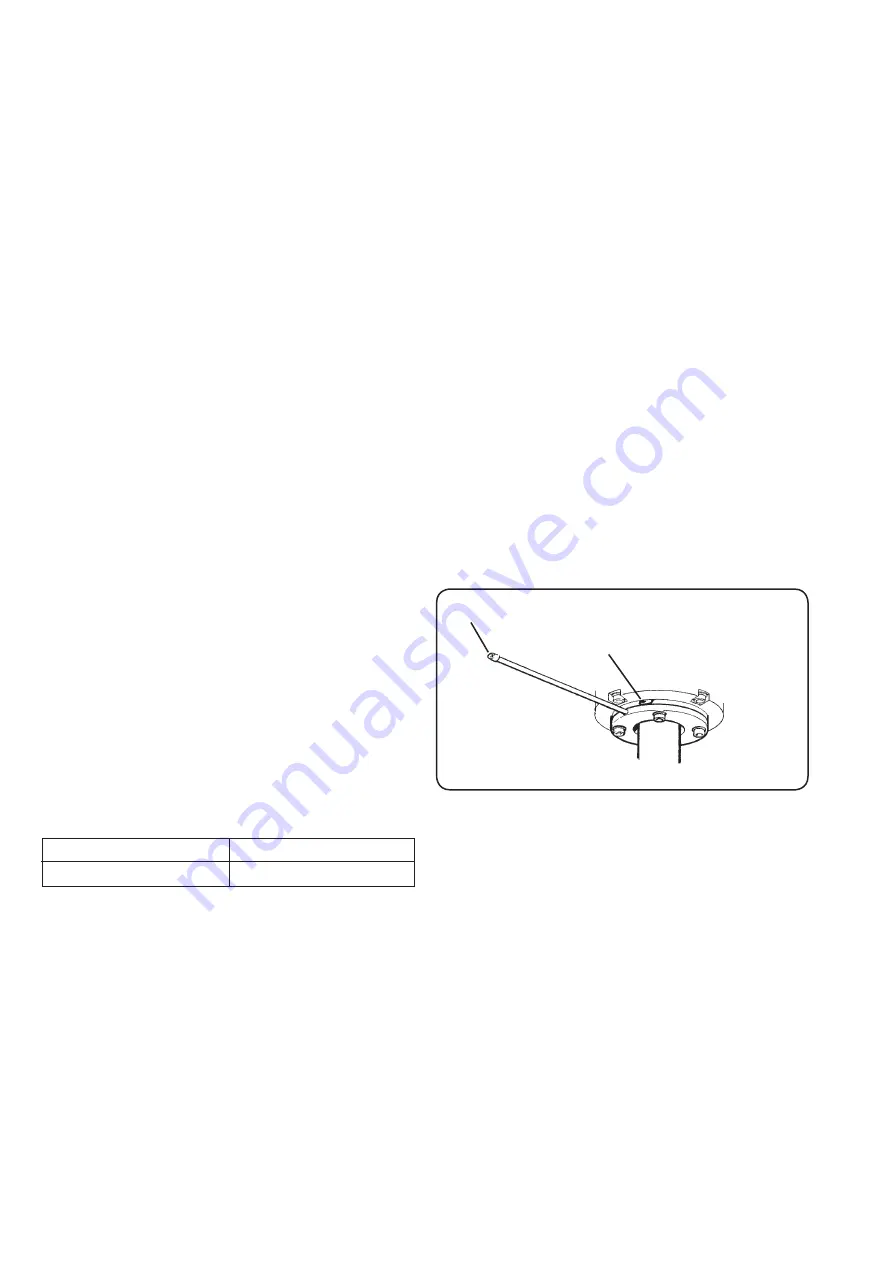
12
·
Tighten the carrier shaft with the carrier screw.
There should be an O-ring under the screw.
This must also be replaced with a new one.
·
Rotate the shaft and check that the rotation is continuous
and soft.
·
Pump in grease into the bearing. See the section for Lub-
rication of agitator axel. About 350 g of grease is required*.
Lubrication of agitator axel
(See fig. 6)
Control/Filling with grease of agitator’s bearing
The agitator’s bearing is filled with grease from the factory.
Refilling grease should take place during installation and then at
least twice per year.
Should be performed by trained personnel.
• Use grease with high temperature properties*.
* Order the maintenance service kit ST12335-00.
• Grease should be pumped in so that it is forced out through
the overflow hole on the bearing housing.
• Check the grease that is forced out. If it shows signs of being
mixed with water, the agitator’s bearing and seal should be
removed for inspection and if necessary replacement.
Dismantling of agitator bearing
(See fig. 5)
·
Dismantle the worn gear motor.
·
Lossen the carrier screw from inside the pan and
pull out the carrier. The O-rings, under the carrier
screw and the carrier must be replaced each time
they have been fitted and used.
·
Pull the sliding bearing seal top straight out.
Note that the small key which ensures that the seal
rotates with the shaft.
NOTE!
Do not touch the sealing surfaces, and
protect the surface from knocks and scratches. Any
grease stains or finger marks on the sealing surfaces
can be wiped clean with pure acetone and a cotton
cloth.
· Lossen the bottom to the bearing. Make sure the rubber
seal in the bottom is not damaged by the key to the work
gears.
·
The bearing can be pressed out from inside the pan.
·
Dismantle the fixed part of the sliding bearing seal.
·
Dismantle the holder and upper rubber packing, the holder
can be pressed out from underside of the pan.
Fitting of agitator bearing
· Make sure that the bearing housing and sealing is well
cleaned and dried.
· Fit the top part of the sliding bearing seal, then fitt them
in the bearing housing.
NOTE!
The ring should be open downwards and is pressed
straight in from above so that it does not become
twisted and bear against it`s position.
· Fitt the fixed part of the slide bearing in to the rotative
part of it.
NOTE!
This requires a special tool which can be ordered
from
Spare Parts Division
. This will require special
tools, can be ordered through spare parts department,
place the tool on the slide bearing and press down with
the carrier shaft.
Order no:
50 & 100 liters
482 01 23-00
150,200 & 300 liters
482 01 23-01
Before fitting:
Lubricate with soapy water to facilitate fitting.
NOTE!
Only soapy must be used.
·
Press the ball bearing on the shaft, the smallest bearing on
top.
·
Press in the shaft and bearing from underneath.
·
Fit the top part of the sliding bearing seal.
NOTE!
Do not forget the key.
NOTE!
Do not touch the sealing surfaces and
protect the surface from knocks and scratches.
Any grease stains or fingermarks can be wiped
clean with pure acetone and a cotton cloth.
·
Fit the carrier and accompaying O-ring. The O- ring
must be replaced each time the carrier has been removed
and in use.
Overflow hole
fig. 6
Lubrication point