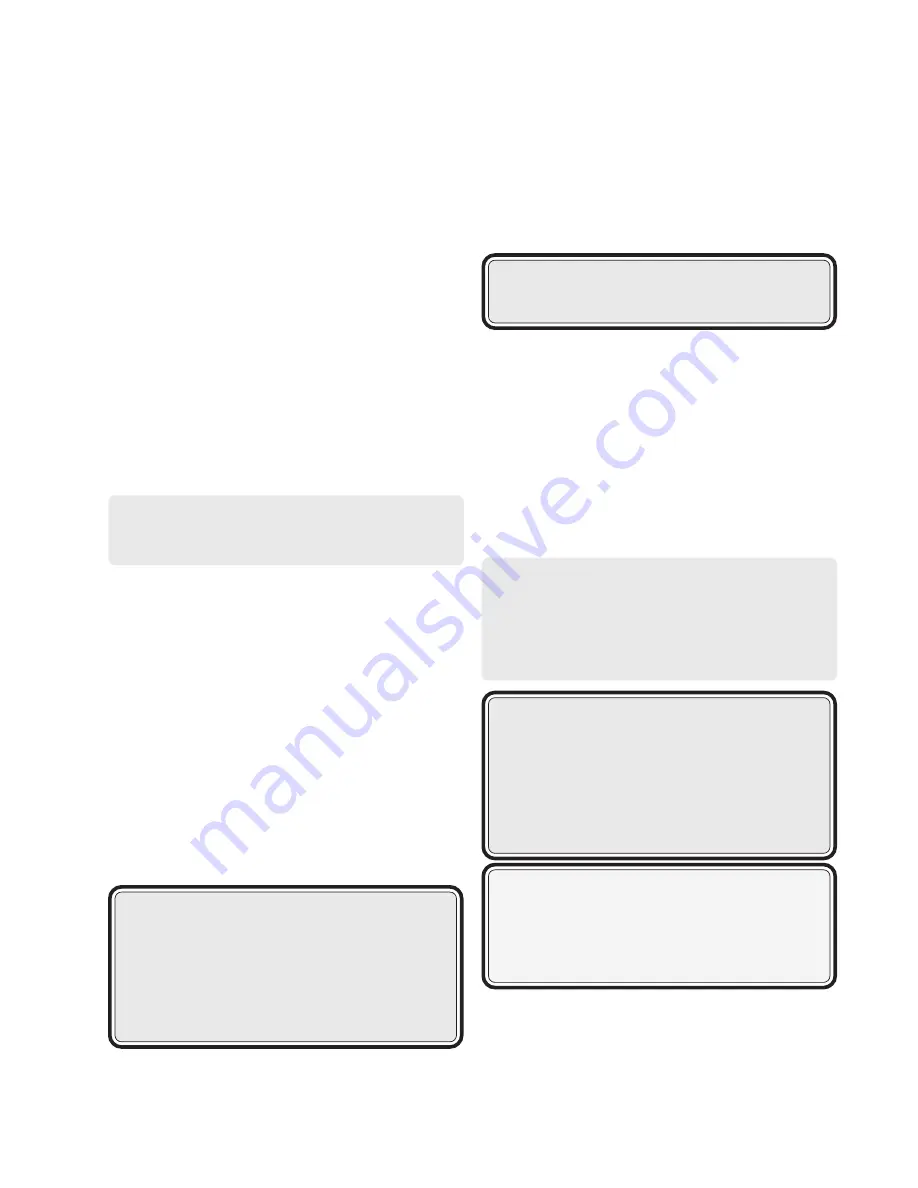
37
moisture may have entered the system. In such cases,
the compressor may need to be replaced to prevent
repetitive service.
If a high-side leak is located and some refrigerant
remains in the system, it is not necessary to change the
compressor.
TESTING FOR REFRIGERANT LEAKS
If the system is diagnosed as short of refrigerant and the
system has not been recently opened, there is probably
a leak in the system. Adding refrigerant without first
locating and repairing the leak, or replacing the
component, will not permanently correct the difficulty.
The leak must be found.
Sufficient refrigerant may
have escaped to make it impossible to leak test
effectively. In such cases, add a ¼” line piercing valve
to the compressor process tube. Add sufficient
refrigerant vapor to increase the pressure to 40 to 50 lb.
per sq. in. Check the low side for leaks. Run the
compressor 2 or 3 minutes and check the high side for
leaks. Recover refrigerant using an EPA approved
recovery system.
NOTE
: The line piercing valve (clamp-on type)
should be used for test purposes only. It must be
removed from system after it has served its purpose.
CHECKING FOR INTERNAL (HOT TUBE) LEAKS
Before checking for internal leaks, check all accessible
system components and joints for leaks.
If an internal hot tube leak is suspected, it must be
confirmed. Use the following procedure:
1. Recover refrigerant by using EPA approved recovery
system.
2. After
system
refrigerant
is completely recovered,
disconnect drier from hot tube. Pinch off and
solder end of hot tube closed.
3. Cut line from condenser to hot tube and solder a
¼”charging hose fitting to open end of hot tube or
put compressor fitting on tube.
4. Connect pressure gauge and access valve to hot
tube, and pressurize to 250 psig using dry nitrogen
or carbon dioxide.
WARNING: NEVER PRESSURIZE WITH
OXYGEN. NEVER OPEN A HIGH PRESSURE
TANK UNLESS IT IS EQUIPPED WITH A
PRESSURE REGULATOR. NEVER PUT HIGH
PRESSURE ON DOME OF COMPRESSOR – IT
COULD EXPLODE. MAKE SURE GAUGE
FITTINGS ARE IN GOOD CONDITION AND DO
NOT LEAK.
5. Leave pressure on hot tube for 24 hours. Any
drop in pressure is indication of leak.
If dry nitrogen or carbon dioxide is not available,
follow steps 1 through 3 above, then steps 4 and
5 below:
4. Connect gauges to charging hose fittings. Pull vacuum
on hot tube.
5. Leave vacuum on each side of system for 24 hours.
Any loss of vacuum indicates leak.
• If oil has a burned sugar odor and shows contamina-
tion (dark color) — follow instructions in next section,
To Flush The System.
Remove as much of
contamination as possible from system before
installing new compressor and filter-drier.
To Flush The System
NOTE:
It is recommended that system be flushed
with dry nitrogen. However, if refrigerant is used to
flush system, you must look at the serial plate to
see what type of refrigerant is used in the system.
This is the only refrigerant that can be used to flush
the system and it must be recovered.
CAUTION: Use extreme care when using dry
nitrogen to flush systems. Pressure in nitrogen
cylinder could be as high as 2000 psi. Nitrogen
cylinder must be equipped with approved
pressure regulator and pressure relief valve.
Ensure that your hoses have adequate ratings
for pressure involved, and that all of your
equipment is in good condition.
CAUTION: The end of flushing hose off tank
regulator must be equipped with a hand
shut-off valve (Robinair No. 40380). Close
hand shut-off valve and adjust nitrogen regulator
to correct pressure before proceeding with
flushing procedure.
COMPRESSOR REPLACEMENT
CAUTION: NEVER install a new compressor
without first checking for possible system
contamination.
To check for contamination, obtain oil sample from old
compressor.
• If the oil has burned odor, but no color change or
residue — follow instructions in section
“Installing A
New Compressor
on page 38”.
To Use Dry Nitrogen To Flush The System:
1. Remove compressor and filter-drier. Connect
process coupling to outlet tube of condenser.
2. Fasten cloth over other end of coil to prevent old oil
from spraying over room.
Содержание BEVERAGE CENTER II
Страница 22: ......
Страница 33: ...32 COMPRESSORWIRING Induction Run Compressor with Relay LADDER SCHEMATIC ...
Страница 34: ...33 WIRING DIAGRAM ...
Страница 61: ...60 ...
Страница 62: ...61 ...
Страница 63: ...62 ...
Страница 64: ...63 ...
Страница 65: ...64 ...
Страница 66: ...65 ...
Страница 68: ...67 Step 3 Step 4 Step 5 Step 6 ...
Страница 69: ...68 Step 8 Step 7 Step 9 Step 10 ...
Страница 70: ...69 Ice Maker Exploded View ...
Страница 71: ...70 Ice Maker Wiring Diagrams Enlarged view ...
Страница 77: ......