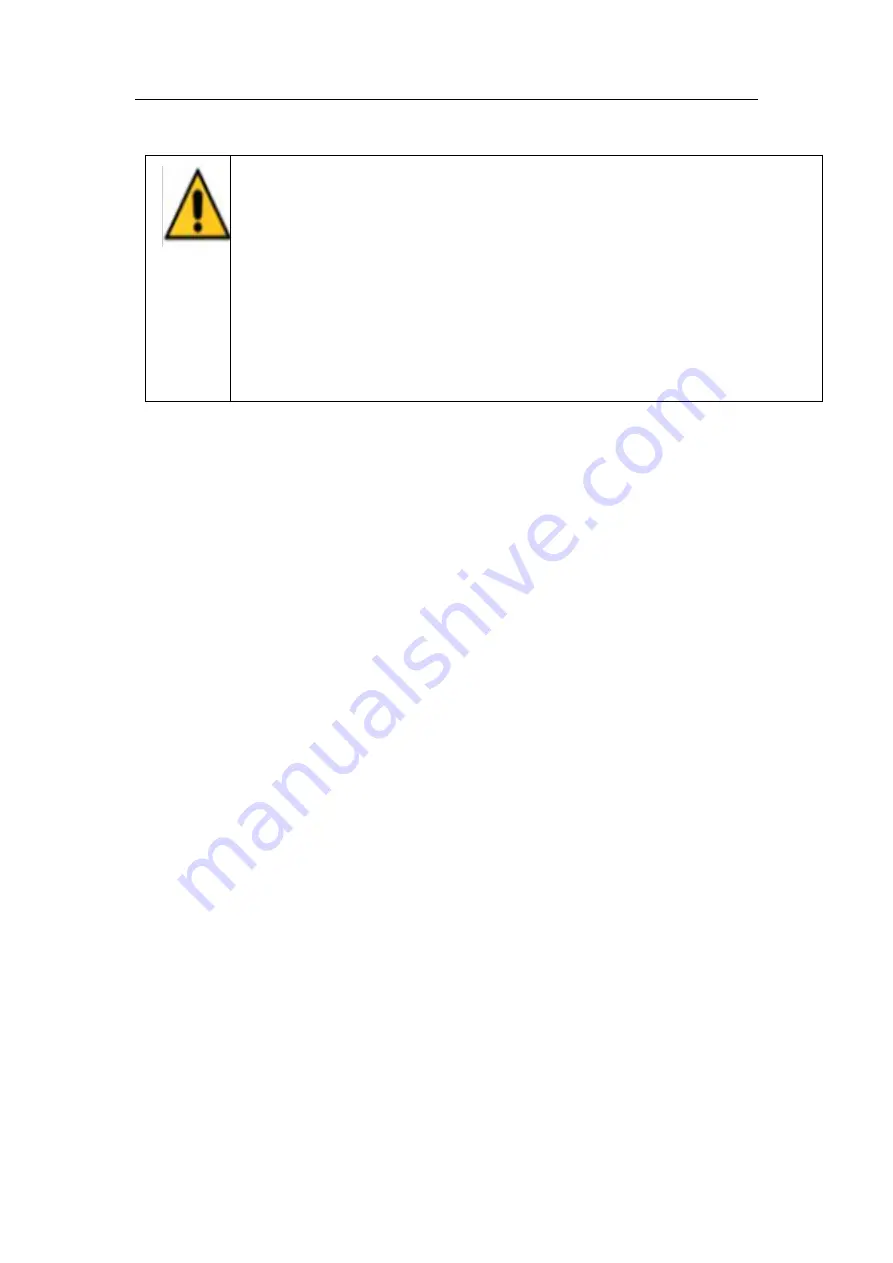
Mechanical Operations and Maintenance Manual for Industrial Robot ER12-4-2000
20
3.2 Robot Installation
Danger
1
、
Set up safety fence
Otherwise, accidents such as personal injury and equipment damage may occur.
The robot should be placed in a position where the tool and the tip of work piece of
the robot arm will not touch the safety fence even if the robot arm reaches the
longest.
Otherwise, accidents such as personal injury and equipment damage may occur.
2
、
If the robot is not fixed, it cannot be electrified and operated.
Otherwise, accidents such as toppling, personal injury, and equipment damage may
occur.
3
、
When choosing the suspended or wall-mounted installation method, it should be fixed
on the ceiling and wall with sufficient strength, and the treatment plan to prevent
falling should also be considered.
Otherwise, accidents such as personal injury and equipment damage may occur.
3.2.1 Setting of Safety Fence
It is necessary to comply with the national standard of the People’s Republic of China
GB11291.2-2013-that is “Safety Requirements for Robots and Robot Equipment; Industrial
Robots, Part 2: Robot System and Integration”, and see more in 5.10 Safety Device Restrictions:
“In the automatic operation of industrial robots, there is a risk of the operator to have contact with
the robot, so safety measures such as guards must be in place to prevent the operator from
approaching.”
In order to avoid equipment damage and personal injury to the operator and surrounding
personnel during the operation of the robot, please be sure to set up a safety fence (and with safety
settings such as interlocking doors)!
Note: GB 11291.2-2013 is equivalent to ISO 10218-2:2011;
3.2.2 Robot Installation Method
The installation of the robot, especially the fixing of the base and the foundation, can
withstand the dynamic load of the robot during acceleration and deceleration and the static weight
of the robot and fixtures. In addition, if the installation surface of the robot is not flat, the robot
may deform and its performance may be affected.
Please ensure that the flatness of the robot installation is less than 0.5mm.
The dimensions of the base installation interface are shown in Figure 3-3 as follows:
Содержание ER12-4-2000
Страница 2: ......