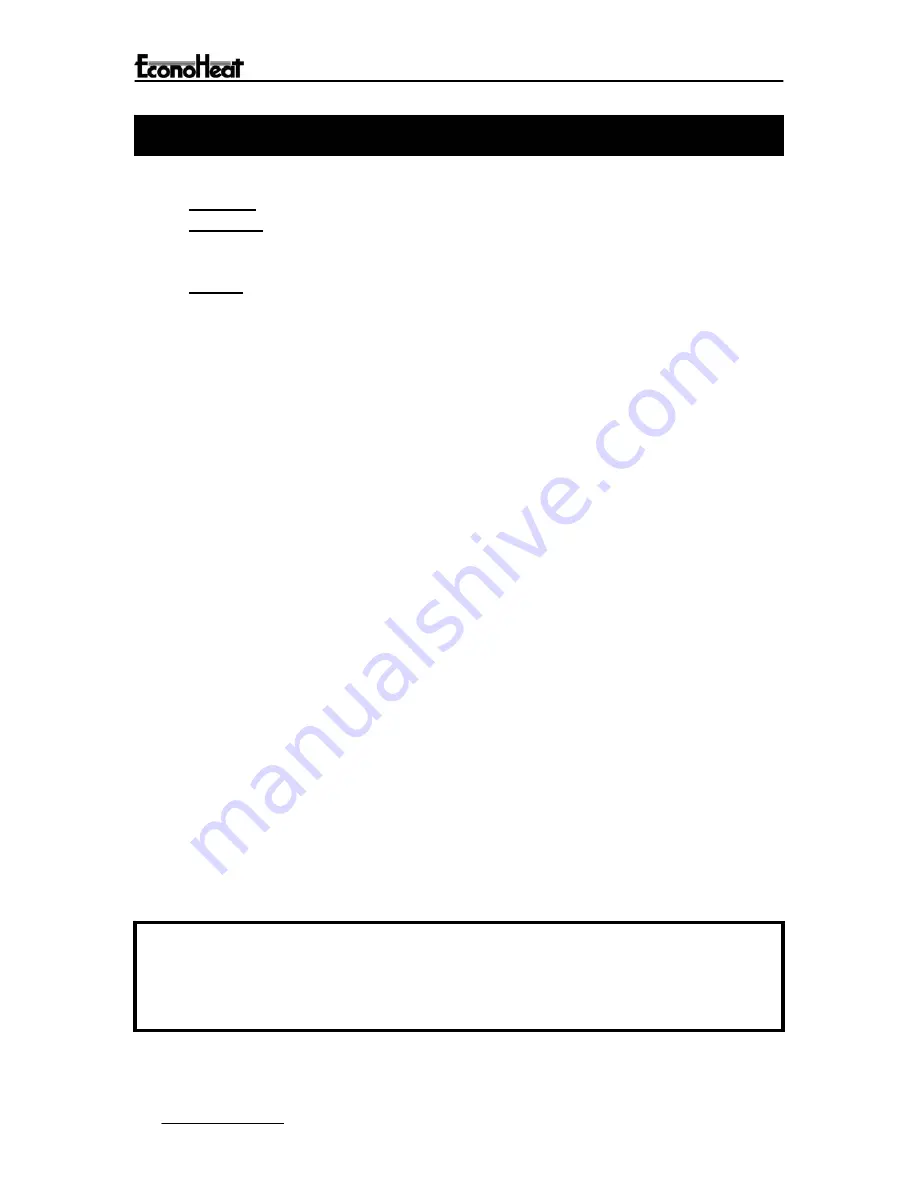
26
Installation, Operation, And Service Instructions
WASTE OIL BURNER:
1.
Weekly
Drain water from storage tank.
2.
Monthly
Clean pump screen on oil pump assembly of sludge and remove
any water. Access to screen is by removing pump cover. Clean flame
cone of deposits.
3.
Yearly
Inspect and adjust electrodes per (figure 37).
CAUTION: turn off
main electrical power before checking or adjusting electrode
settings.
Inspect and check alignment of nozzle in relation to flame
cone/burner tube (figure 37). Tip of nozzle must be 1/4” forward of inside
radius of flame cone. If nozzle is behind inside radius of flame cone,
coking will occur and flame cone can clog. To adjust, loosen Pre-Heater
block securing nut and set screw, push fore or aft as needed then
retighten securing nut and set screw.
BOILER:
1.
Clean Boiler using procedure below.
2.
Check all water system piping for leaks. Repair any found.
3.
Check pressure relief valve operation by opening with manual lever. If it fails to
relieve, replace immediately.
4.
Check operation of safety controls, low water cutoff and manual reset high limit
(if provided).
5.
Check breeching connections to ensure there are no flue gas leaks. Seal any leaks
found with High Temperature Silicone Sealant.
6.
Check flue gas temperature at the test point in the breeching. If gross flue gas
temperature is 550 degrees F or above, suspect that cleaning of the boiler
flueways is required.
BOILER CLEANING:
Turn off the power with the line switch. Disconnect the electrical plug at the J-Box by
the Aquastat Relay. Remove the four hex head bolts from the outer corners of the burner
mounting plate and swing open the burner door with burner mounted to provide access to
the boiler flueways. Remove sludge and deposits from Stainless Steel Insert. When all
deposits are removed, close burner door, and plug in the electrical lead, restore the power
and turn burner on. If a boiler is to be shut down and taken out of service for a period of
time, the boiler should be cleaned immediately upon shut down while the flueways are
still warm. When the boiler gets cold, the deposits harden making cleaning difficult.
Further, hardened deposits will absorb moisture and cause corrosion.
MAINTENANCE
IMPORTANT
It is essential that the boiler be cleaned on an annual basis, even if no soot is present.
Sulfer, and other deposits which may be present, can cause severe corrosion damage
if they are not removed periodically.