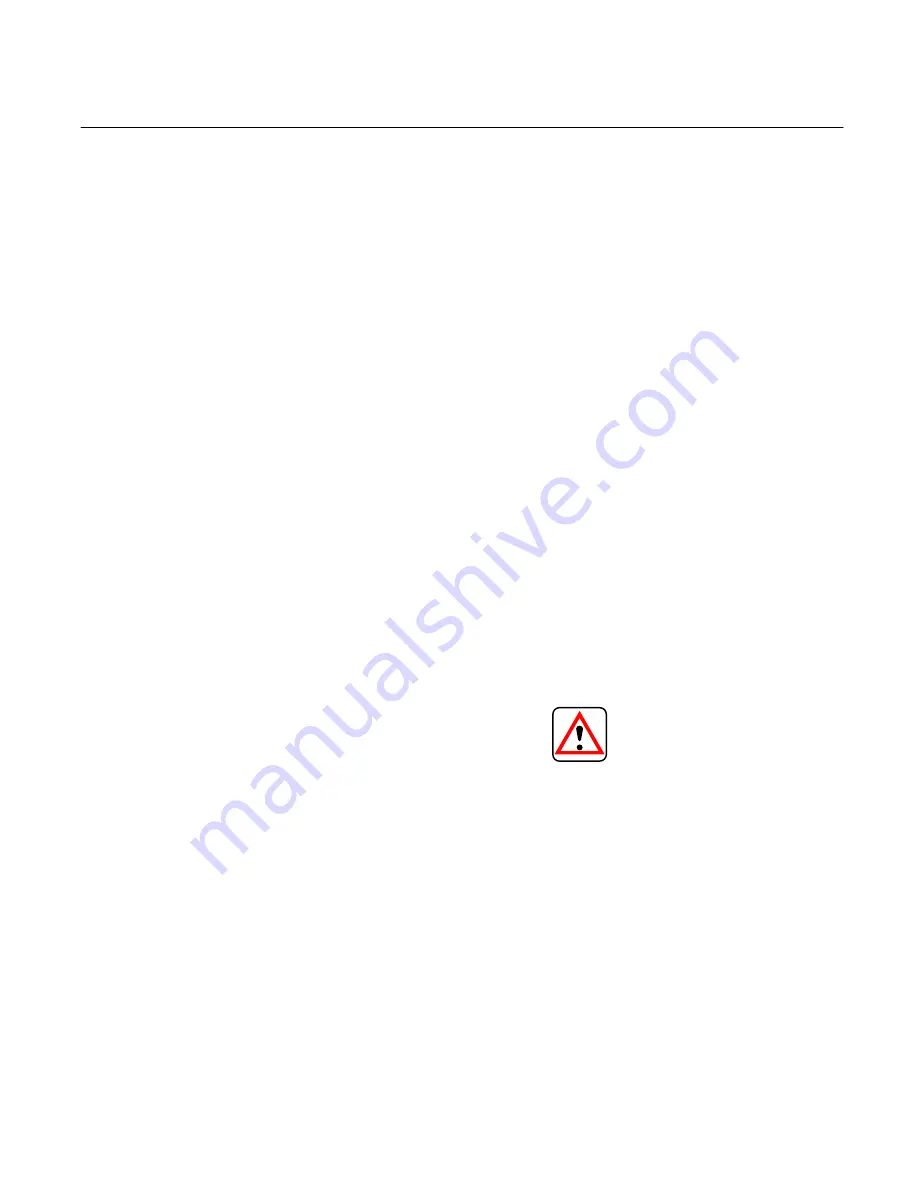
15
Section VI
–
Overhaul
A. General
During disassembly, particular attention should be given to
identification of parts for reassembly. Spools are selectively
fitted to valve bodies and must be returned to the same bo-
dies from which they were removed. Valve sections should
be reassembled in the same order.
Figure 9 and 9A is an exploded view showing the proper
relationship for reassembly. Reference is made to these fig-
ures in the procedures which follow.
B. Disassembly
1.
Controls
- Be sure the unit is not subjected to pres-
sure. Disconnect and cap all lines and disconnect linkage to
the spool. If hand levers are used, remove the
“
E
”
rings
which retain the fulcrum rod and remove the links, levers and
retaining rings.
2.
Attaching Parts
- Remove the four tie studs and nuts
and separate the valve sections. Be careful not to destroy or
lose spacers.
3.
End Caps
- Remove the two screws which secure
the spool and cap and remove the cap. If the cap has a det-
ent assembly, screw out the detent plug and remove the
spring and piston. Remove the O-ring from the body.
4.
Operating Spool
- Slide the spool out of its bore from
the cap end and remove the O-rings from the valve body
around the spool bore. Do not remove the centering spring
and retainers unless it is necessary to replace them.
5.
Check Valve
- Grip the stem of the check valve plug
with pliers and pull it out of the valve body. Remove the
spring and poppet from the valve body.
6.
Relief Valve Sub-Assy
- Screw out the plug which
retains the relief valve and remove the O-ring from the plug.
Remove the spring and the relief valve sub-assembly. In F*
sections, remove the solid plug.
7.
Valve Body
- Remove the plug and O-ring from the
blocked cylinder port on models with a single acting spool. If
the alternate discharge port is plugged, it is not necessary to
remove the plug unless the body is to be replaced.
C. Cleaning, Inspection and Repair
1. Discard all old seals. Wash all parts in a clean mineral
oil solvent and place them on a clean surface for inspection.
2. Carefully remove burrs by light stoning or lapping. Be
certain there is no paint or burrs on matting surfaces of valve
bodies.
3. Inspect the valve spools and bores for burrs and scor-
ing. If scoring is not deep enough to cause objectionable
leakage, the surfaces can be stoned or polished with crocus
cloth. If scoring is excessive, the valve body and spool must
be replaced by ordering a new section. Check the valve
spool for freedom of movement in the bore.
4. Check the relief valve for smooth movement in its
bore. The valve should move from its own weight.
D. Assembly
NOTE
Coat all parts with clean hydraulic oil to facilitate
reassembly and provide initial lubrication. Petro-
leum jelly can be used to hold seal rings in place on
assembly.
1.
Valve Body
(Figure 9) - On models with single-acting
spool, install the O-ring on the port plug and plug the ap-
propriate cylinder port. Tighten the plug securely, but DO
NOT over tighten.
2.
Relief Valve
- Install the O-ring on the relief valve plug.
Place the relief valve assembly in its bore, hex nut end to-
wards opening. Install the spring and plug and tighten the
plug securely but DO NOT ever tighten.
3.
Check Valve
- Install a new back-up ring and O-ring
on the check valve plug with the O-ring toward the spring
and poppet. Place the poppet and spring in the body and
install the plug.
4.
Operating Spool
- If centering spring and spool have
been removed, install new O-rings in the O-ring groove in
the body at each end of the spool bore. Install spool in bore
from the cap end. Install the flat retainer, guide and screw.
Tighten the screw securely. Align the flat retainer by shifting
the spool. Spool bind is an indication of flat retainer misalign-
ment. Install the end cap and attaching screws. Tighten the
end cap screws securely. On models with detents grease all
the detent parts and install the piston, springs and plug. Be
sure to screw the plug in all the way.
5.
Assembly of Unit Sections.
CAUTION
Make sure all mating surfaces of valve bodies are
free of burrs and paint.
Install seal rings in the grooves in the body of each inlet and
center section. Use petroleum jelly to hold the seals in place.
For CM2 valves, install the spacers to insure against spool
bind when the studs are tightened. With the mounting feet on
a flat surface carefully place the sections together in the
same order in which they were removed. The mounting feet
must be maintained in a flat plane to prevent spool bind (due
to body distortion) when the valve is mounted for operation.
If levers are used, install pins in each spool and assembly
the levers fulcrum rod and
“
E
”
rings. Tighten the nuts on the
CM2 to 45-50 foot pounds torque and on the CM3 to 55-60
foot pounds torque.