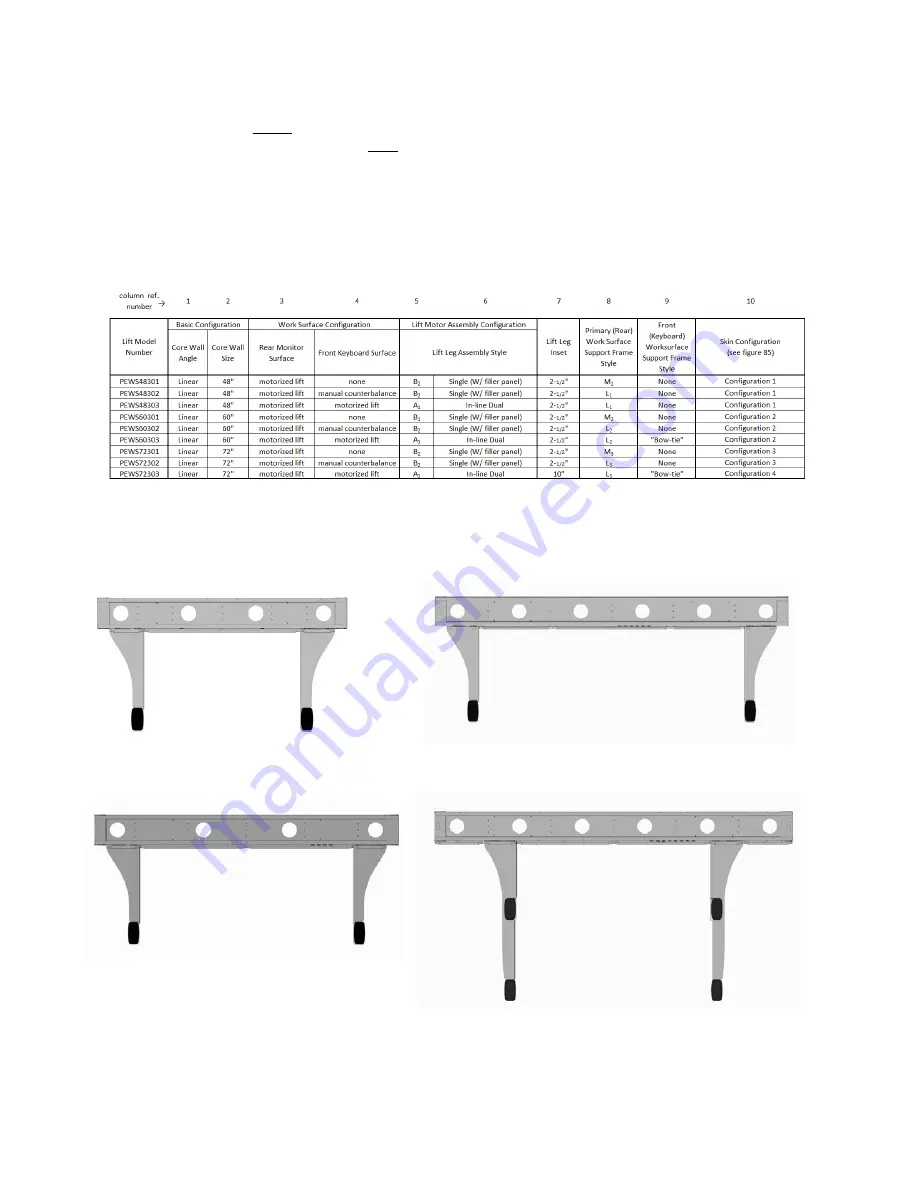
56
Profile
Installation Manual
PROFILE INSTALLATION MANUAL
Eaton.com/profile
P a g e
|
54
Eaton’s Profile Command Console
Installation Manual
B.
To install A Linear Sit-to-stand Desk
(Refer to the previous section, Section IV.A., for corner sit-to-stand desks)
All Profile linear sit-to-stand desks are comprised of similar components: lift leg assemblies, work surface support frames, work
surfaces, electronic components and core skins. Some linear sit-to-stand desks may have additional components such as manual
counterbalance mechanisms (for non-motorized keyboard surfaces) and cable management devices. However, while the
components are all similar, there will be some variations based on the model size and configuration.
Refer to the following table (figure 84) to determine the features and variations of your specific model number. The installation
steps on the following pages will refer to the information found in this table.
Step 1. Determine The Component Layout Of Your Linear Sit-to-Stand Desk
Refer to table 84 and figure 85 to determine the layout of your linear sit-to-stand desk model. They will define the size and
style of each component along with the locations of your core wall skins and lift leg assemblies. The figures in step 2 and step
5 on the following pages will help you visually identify the style and size of your lift leg and work surface frame components.
Linear Sit-to-Stand Desk Configuration Table (Figure 84
)
Lift leg
Ref col. 5
Lift leg
Ref col. 5
Lift leg
Ref col. 5
Lift leg
Ref col. 5
Lift leg
Ref col. 5
Lift leg
Ref col. 5
Lift leg
Ref col. 5
Lift leg
Ref col. 5
14
15
/
16
” Sk
in
14
15
/
16
” Sk
in
29
7
/
8
” Skin
19
3
/
8
” Skin
20
15
/
16
” Skin
20
15
/
16
” Skin
19
3
/
8
” Skin
9
3
/
8
” Sk
in
9
3
/
8
” Sk
in
Skin Configuration 1
PEWS48301
PEWS48302
PEWS48303
Skin Configuration 2
PEWS60301
PEWS60302
PEWS60303
Skin Configuration 3
PEWS72301
PEWS72302
23
15
/
16
” Skin
Skin Configuration 4
PEWS72303
Figure 85 – Linear Sit-to-Stand Skin Configuration