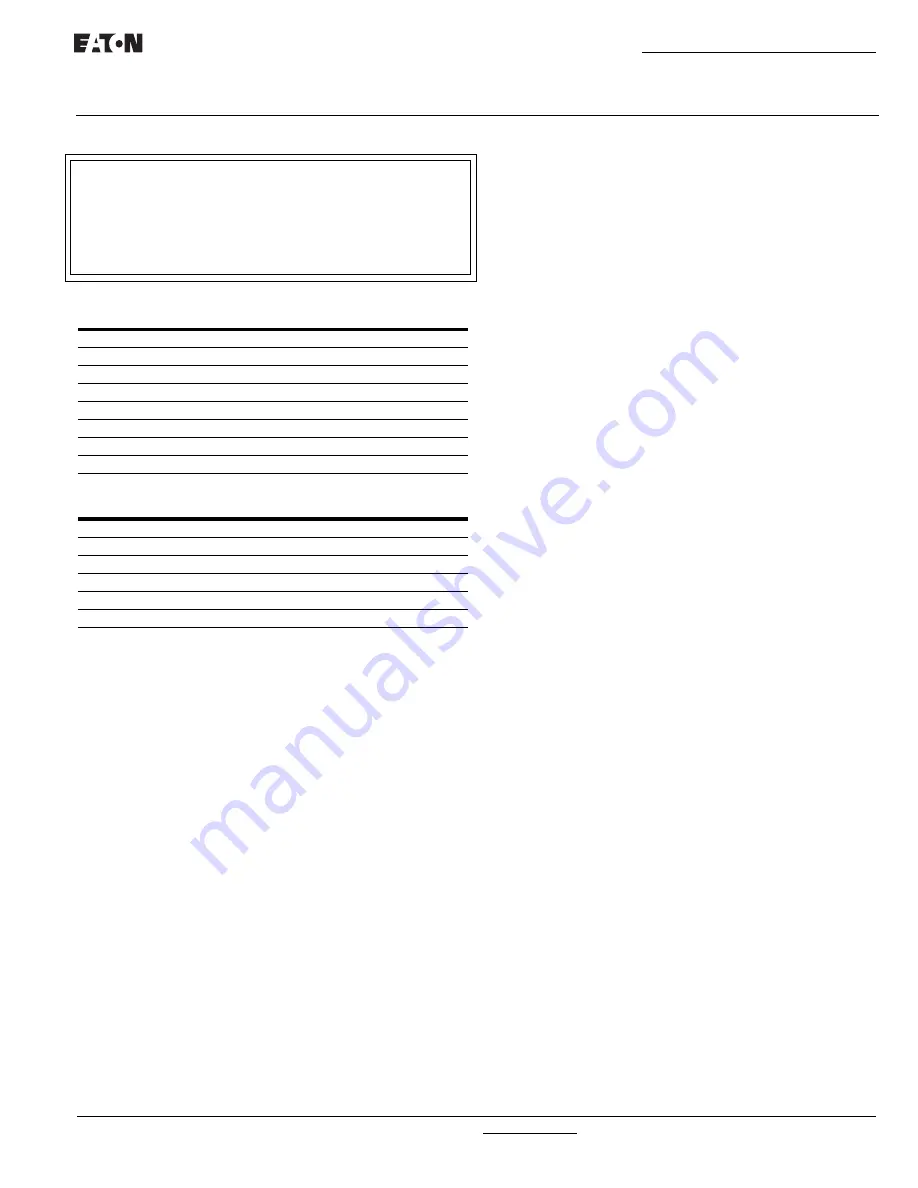
IB140012EN
For more information visit: www.eaton.com
Instructional Booklet
Effective: March 2021
Page
17
Operation and Maintenance Manual,
Automatic Transfer Switch Controller, ATC-900
4.3 Switch Type Setpoints
There is a feature that the user can set the SWITCH TYPE
(Device) by simply changing the setpoint. See Tables 4 and 5
below .This allows the ATC-900 controller to be completely pro-
grammable by the end user with all options available. It cannot be
read/changed by MODBUS. The feature types are the following
and depends on if the switch is an open type or a closed (and
open) type. See section 5.2 on how to set the switch type.
Table 4. For Open Transition Controllers
Table 5. For Closed Transition Controllers
4.4 Test Mode
The Engine Test is intended to allow periodic system tests. The
exact test conditions are determined by the programmed set-
points. The operator-selected parameters include setting the
engine run time and the Test Mode. Refer to Table 7 for test pro-
gramming details.
There are four test modes:
1 No Load Engine Run Test;
2 Load Transfer Engine Test; or
3 External: Select No Load or Load Transfer based on Engine Test
Mode Select programmable input.
4 Disabled.
IF THE ATS IS UNABLE TO PROCESS A ENGINE TEST REQUEST
DUE TO THE ATS STATUS, THE REQUEST IS IGNORED.
When the Engine Test pushbutton is pressed, the display will
prompt the user to input a password (factory set to 0900). Use
the arrow keys to enter the password, then press the right arrow
key to highlight the "Enter Password" icon and press the Enter
key.
The ATC-900 will display the Time Delay on Engine Starting
(TDES) timer countdown. Once the TDES countdown reaches
zero, the ATC-900 Controller will initiate an engine start. The
engine run duration will be per the Engine Run Test Time setpoint.
If Test Mode is set to "Engine Run", then the switch will start the
non-preferred generator, but will not initiate a transfer to the non-
preferred source.
If Test Mode is set to "Load Transfer", then the switch will start
the non-preferred generator and initiate a transfer to the non-pre-
ferred source once the generator output has reached the specified
setpoints.
All enabled and programmed time delays will be performed per the
setpoints during an engine test. The time delays will appear on the
LCD Display with “countdown to zero” when active. Depending
on the setpoints and the optional features selected with the ATC-
900 Controller, these can include:
•
Time Delay Engine Start (TDES);
•
Time Delay Normal to Emergency (TDNE);
•
Time Delay Emergency to Normal (TDEN);
•
Time Delay for Engine Cooldown (TDEC);
•
Time Delay Neutral (TDN);
•
Time Delay Normal Disconnect (TDND)*
•
Time Delay Normal Reconnect (TDNR)*
•
Time Delay Emergency Disconnect (TDED)*
•
Time Delay Emergency Reconnect (TDER)*
•
Pre-transfer Delay Signal (TD PRE-TRAN).
•
Post-transfer Delay Signal (TD POST-TRAN).
* See flowchart example in Appendix C.
All operations are “Failsafe”, meaning they prevent disconnection
from the only available power source and also force a transfer or
re-transfer operation to the only available power source.
During an engine test, if the Engine Test pushbutton is pressed a
second time before the Engine Test is complete, the Engine Test
will be terminated. An engine test may also be aborted in the fol-
lowing ways:
1. If the Emergency Source does not become available within 90
seconds of the ATC-900 providing the engine start command;
2. If, during the TDNE countdown, the Emergency Source goes
unavailable more than three times (Each time, TDNE will
restart);
3. If the Emergency Source is powering the load and it goes
unavailable for more than the TDEF (Time Delay Engine Fail-
ure) setting; and
4. If the Normal source becomes unavailable.
When an engine test is aborted due to an unavailable source
during TDNE countdown, the Alarm relay will energize, a “TEST
ABORTED” message will appear on the display, and the event will
be logged into the Transfer History as “Aborted Test” Aborted.
4.5 USB Interface (Event Status-Setpoints)
Every ATC-900 transfer switch includes a front panel, NEMA 4X
rated USB port for use in configuring set points or downloading
event data to a USB flash drive. The USB interface is brought to
the front of the enclosure to enable flash memory (memory stick)
to be plugged in to upload or download data such as History Data
Logging, or Setpoints. The USB interface will only work with
memory devices and not laptop computers.
4.5.1 Upload/Download Setpoints via USB
To reduce the time spent on site for commissioning, set points
can be configured at a PC using the ATC-900 configuration
software and saved to a USB flash drive to be uploaded to one or
multiple controllers. Set points are also easily copied from one
controller to another. See EASE, section 7.1, last paragraph.
SWITCH TYPE
TRANSITIONS
Unprogrammed
Open Style
2-Position Contactor
In-Phase/Open
Breakers with Motor Operator
Open/Delayed
Power Breakers
In-Phase/Open/Delayed
3-Position Contactor
In-Phase/Open/Delayed
Medium Voltage Switch
In-Phase/Open/Delayed
Medium Voltage Breaker
In-Phase/Open/Delayed
3000 Amp Contactor
In-Phase/Open/Delayed
SWITCH TYPE
TRANSITIONS
Unprogrammed
Closed Style
Power Breakers
Closed/In-Phase/Open/Delayed
3-Position Contactor
Closed/In-Phase/Open/Delayed
Medium Voltage Switch
Closed/In-Phase/Open/Delayed
Medium Voltage Breaker
Closed/In-Phase/Open/Delayed
3000 Amp Contactor
Closed/In-Phase/Open/Delayed