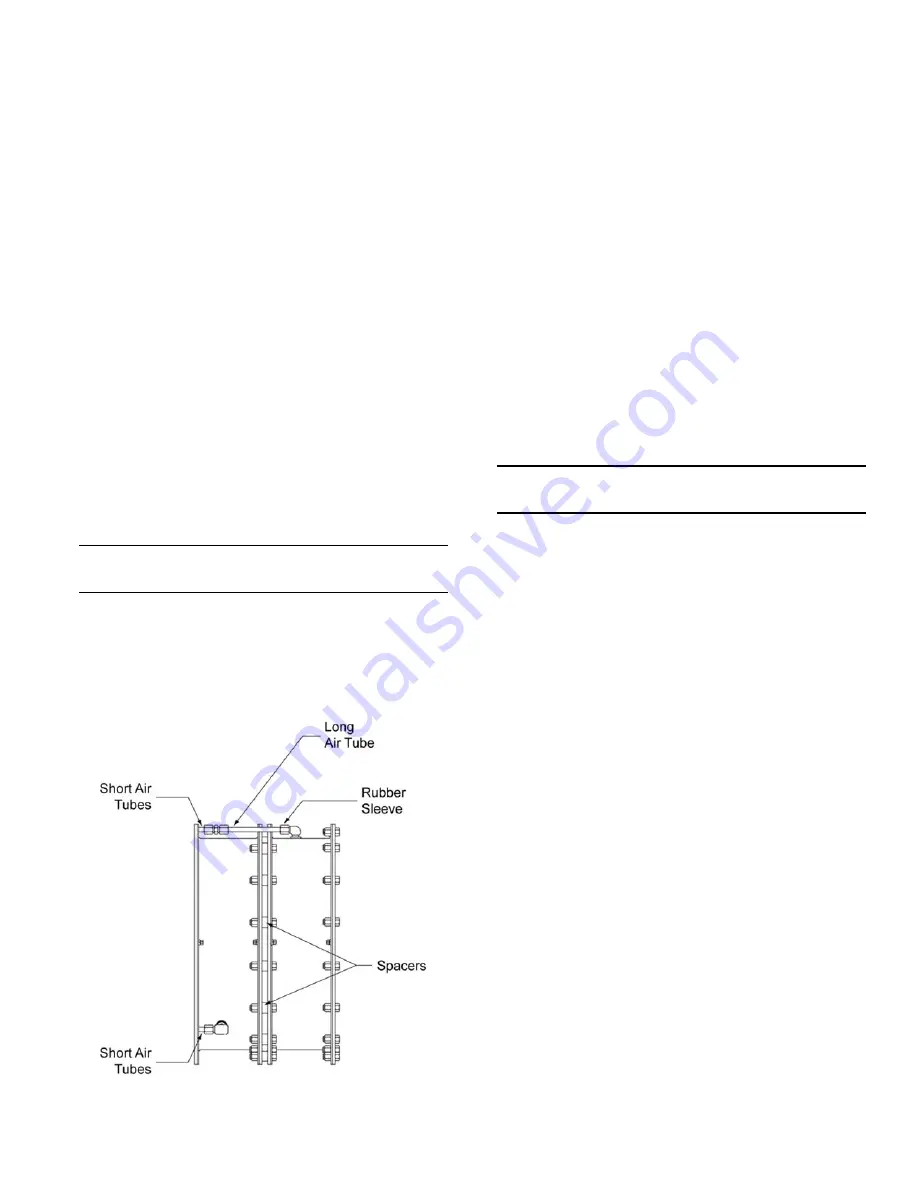
VC 5000
12
©Copyright Eaton Corp., 2019. All rights reserved.
2.6
Installation of Element and Drums
(Dual Wide)
2.6.1
Separate the shafts as far as the bearing
clearances will allow.
2.6.2
Attach the drum having the female register on the
drum flange to the drum hub with short screws and
lockwashers. There are tapped holes in the drum
flange to accept the screws. Make sure the bore in
the drum flange fully engages the pilot on the drum
hub. See
Figure 3.
2.6.3
Disassemble the dual element into two halves and,
noting the orientation of the air connections, place
the element onto the drum installed in 2.6.2.
2.6.4
Noting the orientation of the flange on the
remaining drum with respect to the air connections
on the remaining element, slide the drum into the
element.
2.6.5
Hoist the element/drum into position, align the
tapped holes in the drum having the male pilot with
the tapped holes in the drum attached to the drum
hub, and attach both drums to the drum hub with
the appropriate fasteners. See Table 1. Make sure
the male pilot fully engages the female register.
⚠
WARNING
Use only the proper grade and number of
fasteners. Using commercial grade fasteners
(Grade 2) in place of Grade 8 fasteners (where
called for) may result in failure of the fasteners
under load, causing personal injury or
equipment damage.
Figure 11
2.6.6
Align the air connections and reassemble the
element halves, making sure the spacers are in
place between the elements. See
Figure 11
.
2.6.7
Reassemble the air connection tubes. If an elbow
has been removed, use a good quality pipe sealant
on the threads. See
Figure 11
.
Note
: The elbow assemblies on the outboard
element (farthest from the spider) use rubber
compression sleeves. Make sure the sleeves are
secure on the long air tubes.
2.6.8
Install the air connection gaskets onto the air tubes.
The metal backup washer is to be positioned
towards the elbow (away from the spider). See
Figure 10
.
2.6.9
Align the element air connections with the
corresponding passages in the spider and attach
the element to the spider with the appropriate
fasteners. See Table 1. Make sure the element fully
engages the register in the spider.
⚠
WARNING
Use only the proper grade and number of
fasteners. Using commercial grade fasteners
(Grade 2) in place of Grade 8 fasteners may
result in failure of the fasteners under load,
causing personal injury or equipment damage.
2.7
Air Control System
2.7.1
A typical air control system is shown on
Figure
12
.
Since the air control system used will be dependent
on the specific application, a detailed description
cannot be made in this manual. Following are some
general guidelines for installing and adjusting air
controls.
2.7.1.1 The air receiver tank must be located as close to
the rotorseal as possible for consistent clutch or
brake response.
2.7.1.2 Use full size piping and valves consistent with the
rotorseal size.
2.7.1.3 Keep the number of elbows to a minimum.
2.7.1.4 Use poppet-type solenoid valves. Spool valves are
not recommended.
2.7.1.5 An air line lubricator is not required for the element;
however, if one is used, it must be a non-
adjustable, mist-type.
2.7.1.6 If a flow control valve is used, it must have free flow
(indicated by an arrow on the valve body) directed
away from the element.