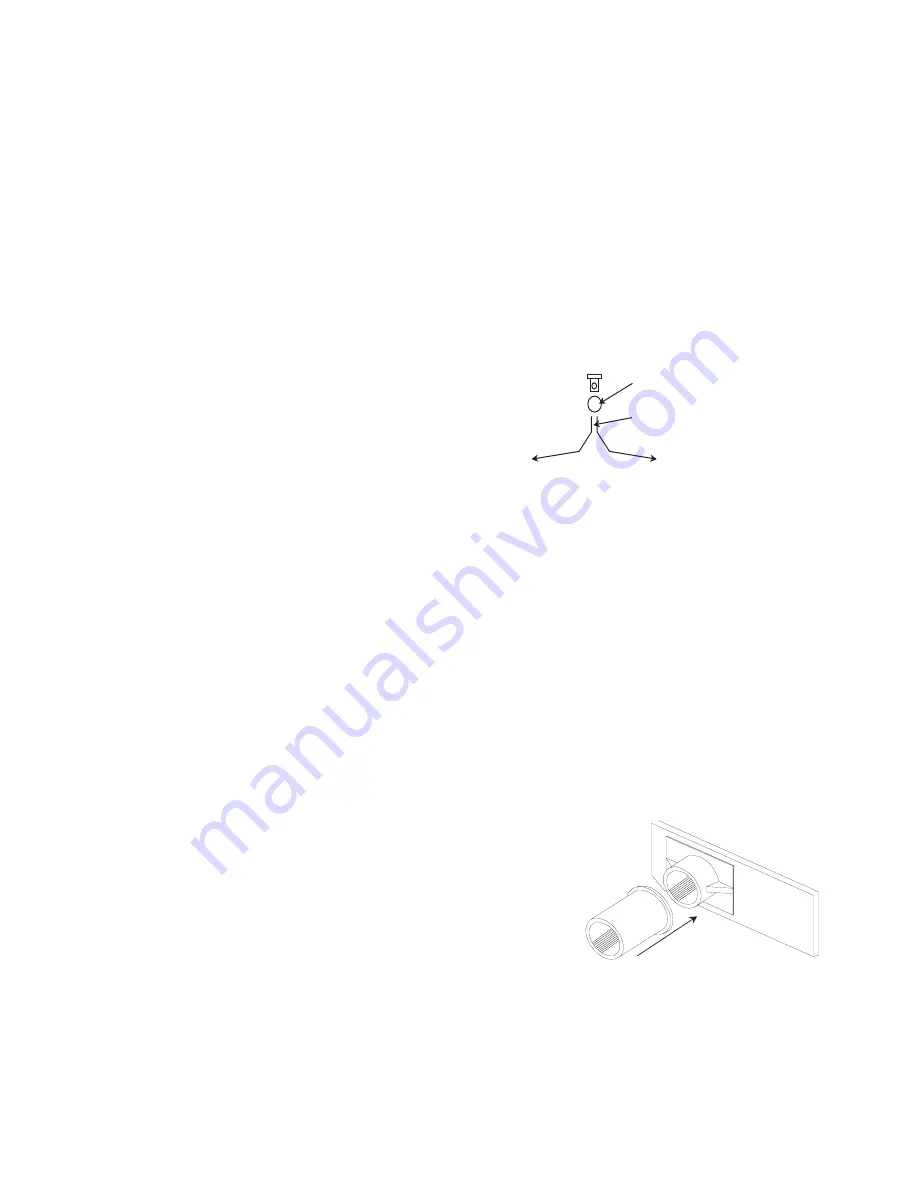
LEAVE BODY TO HARDEN
33)
Once the roof has firmly set, take time now to inspect the fit of the roof outline against the
end molding. Due to the different means by which the roof and ends are produced, it will be found
that the alignment of the roof line and the ends requires blending with an appropriate car body, or
modelling filler. Likewise, there is a gap between the underside of the roof and the top of the non-cab
ends which also requires filling as necessary.
Once again, do take your time with these steps not least because the roof and end joints will be very
visible on the finished model.
34)
If the roof vents were not fitted earlier now is the time to do so. The roof vents will also offer
the body some extra stability when it is placed upside-down for the following steps.
35)
(DMCL) Form and fit the water pipes to the filler casting (unfortunately not shown on the
castings photo, but looks like a small top hat!) on the roof
and down to the brackets moulded onto the end. Use
0.7mm brass wire for the pipes, file the ends of the two
halves flat, solder together, drill a hole through the body of
the filler and insert the pipe end. See photos for shape of
pipe run (DMBS GUARDS DOOR - Cl. 108 prototype). Cut off the pipes about 2.5mm below the
retainers.
36)
(DMCL) Fit the small roof box (C33) detail on the centerline between the second pair of vents
(from the rear).
UNDERFLOOR ASSEMBLY
NOTE: The molded ribs on the floor molding determine the underside of the floor molding!
37)
Check the floors will fit within the sides and end molding. It is likely that you will have to adjust
the floor width to gain the best fit. Do this carefully removing the minimum amount evenly from each
side to keep the floor central to the body. This is best done using a scraping action with a sharp blade.
38)
To improve the visual appearance of the underframe, cut the two lengths of 5mm wide 0.5mm
styrene to 391mm and affix to the outside face of the molded solebars. Align the strips to the rear
edge of the underfloor so that they protrude at the front (take care when handling so as not to break
the ends). Keep the strip firmly butted against the underside of the floor lip.
39)
Remove the four bufferbeams from their sprues together
with their associated extension collars, clean flash, etc. and check
the fit of the buffer shanks into the holes. Use a 3mm drill bit to
carefully open any tight holes to allow the buffers to slide easily. Use
a buffer to align the buffer stock extension collar to the end of the
buffer housing - affix with solvent and remove the buffer
immediately. Once the joints have hardened run the 3mm drill
through again to ensure the holes are clean.
40)
Install the floor into the body and temporarily secure into position. Now fit the bufferbeams to
the underside of the cab ends, aligned centrally across the cab and butted against the ends of the
extended solebars to ensure vertical squareness.
DO NOT GLUE THE BUFFERBEAM TO THE
SOLEBAR EXTENSIONS BECAUSE IF YOU DO, YOU WILL NOT BE ABLE TO REMOVE THE
9
DRILL 0.7MM HOLE THROUGH
BODY OF FILLER
FILE HALF FLAT BETWEEN
TWO PIPES AND SOLDER
TOGETHER
Buffer
Extension
Содержание DERBY LIGHTWEIGHT CLASS 108 DMU
Страница 20: ...20 DMBS DMCL CASTINGS CONTROL DESK DETAILS...