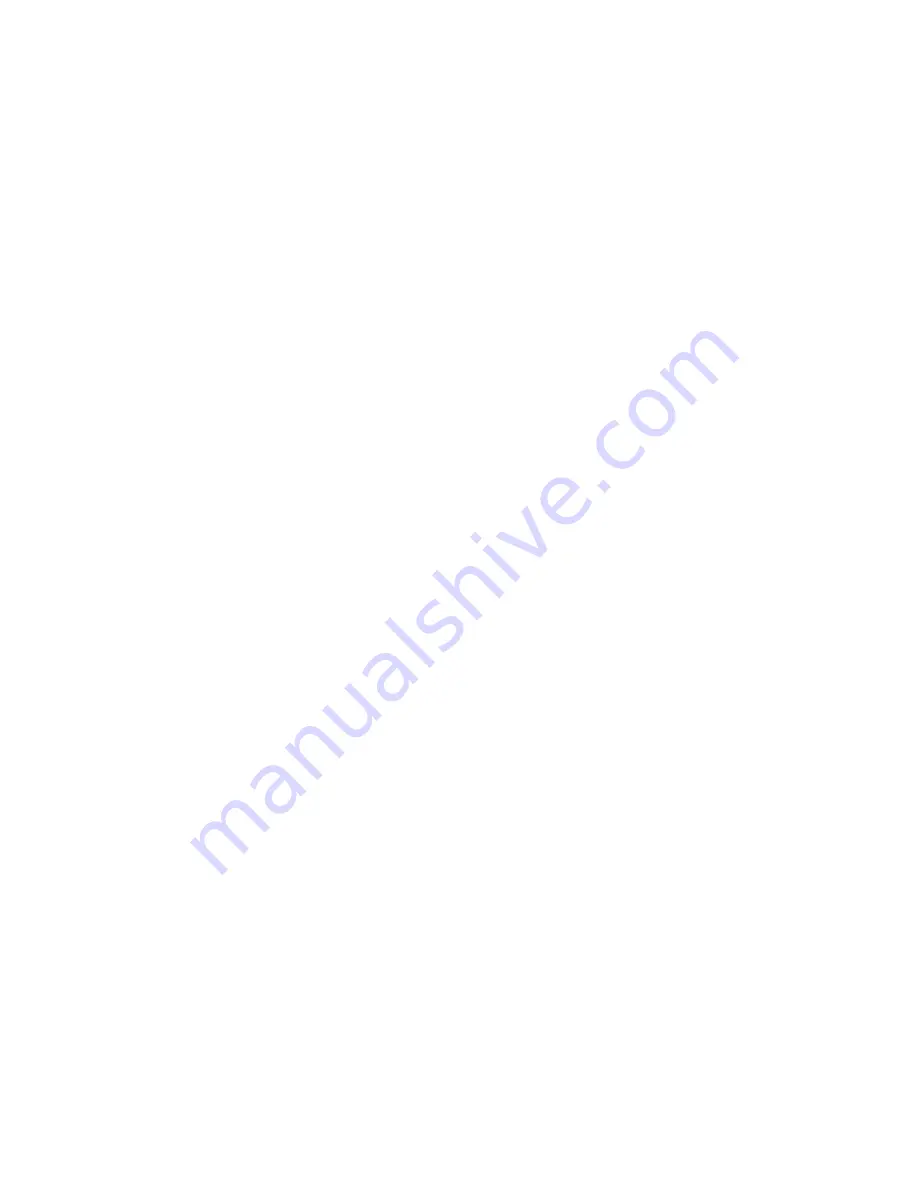
8
Eastwood Technical Assistance: 800.544.5118 >> [email protected]
SETTINGS SELEcTION
With the materials selected of which you will be welding you can begin to set up the welder for the specific material.
1. AC/DC
– The type of current will need to be selected depending on the type of material being welded. For the most part
when welding steels the switch will be set to DC and when welding aluminum the switch will be set to AC.
2. Clearance Effect
– This step can be omitted if welding in DC. If welding in AC this will need to be set. The more negative
the value will result in greater penetration and less cleaning and the more positive the value will result in less penetration
but greater cleaning. For suggested settings refer to the data chart on the welder.
3. Foot Pedal/Panel Control
– Determine whether you will be using the switch on the torch or the foot pedal for arc starting
and stopping and put the selector switch in the appropriate position. Note that some connections changes will be necessary
also when switching the control type. These connection changes are covered in the Set-Up section of this manual.
4. Amperage
– If welding using the switch on the torch to control the arc, Set the Output Amperage Knob marked “A” (Fig. A)
located at upper left of the top panel to an appropriate setting based on the thickness and type of the metal being welded.
(Refer to Data Chart for actual settings)
. If welding using the foot pedal to control the arc, it uses the same operation as the
panel control but is adjusted on the side of the foot pedal rather than the front panel. (Fig. A)
5. Pre Flow
– This adjustment controls the time (in seconds) that the shielding gas starts to flow before the arc starts.
(Refer to Data Chart for actual settings)
.
6. Post Flow
– This adjustment controls the time (in seconds) that the shielding gas flows after the arc stops.
(Refer to Data Chart for actual settings)
.
7. Power Switch
– Once all of the settings have been selected and the torch assembled and ready to use, the welder can be
plugged in and turned on.
8. Shielding Gas Flow
– Set the Gas Flow Rate to the appropriate value with the Knob located at the left side of the regulator.
SHIELDING GAS FLOw ADjuSTMENT
After connecting your Shielding Gas Regulator, the gas flow rate needs to be adjusted so that the proper amount of Shielding Gas
is flowing over your weld. If there is too little gas flow there will be porosity in your welds as well as excessive spatter, if there is
too much gas flow you will be wasting gas and may affect the weld quality. The included regulator has 2 gauges on it; the gauge
on the left is your flow rate while the gauge on your right is your tank pressure.
1. Open your Shielding Gas tank valve all the way.
2. Adjust the knob on the regulator to ~20 CFH.
3. Turn on the welder and trigger the torch switch or foot pedal which will start the gas flow.
4. As you trigger the torch switch or foot pedal, you will notice that as the gas flow starts the needle on the gauge drops to a
steady reading. The reading while flowing is the value you want to read.
5. The gas flow should be set to 12-21 CFH while flowing depending on the material and thickness being welded. The CFH
(Cubic Feet per Hour) scale is the inside scale in red on your flow gauge. 20 CFH is the most typical flow rate but it may
need to be adjusted in some cases depending if there is a slight breeze or some other instance where additional
shielding gas is required to prevent porosity in the weld.
6. When finished welding remember to close the gas valve on the bottle.