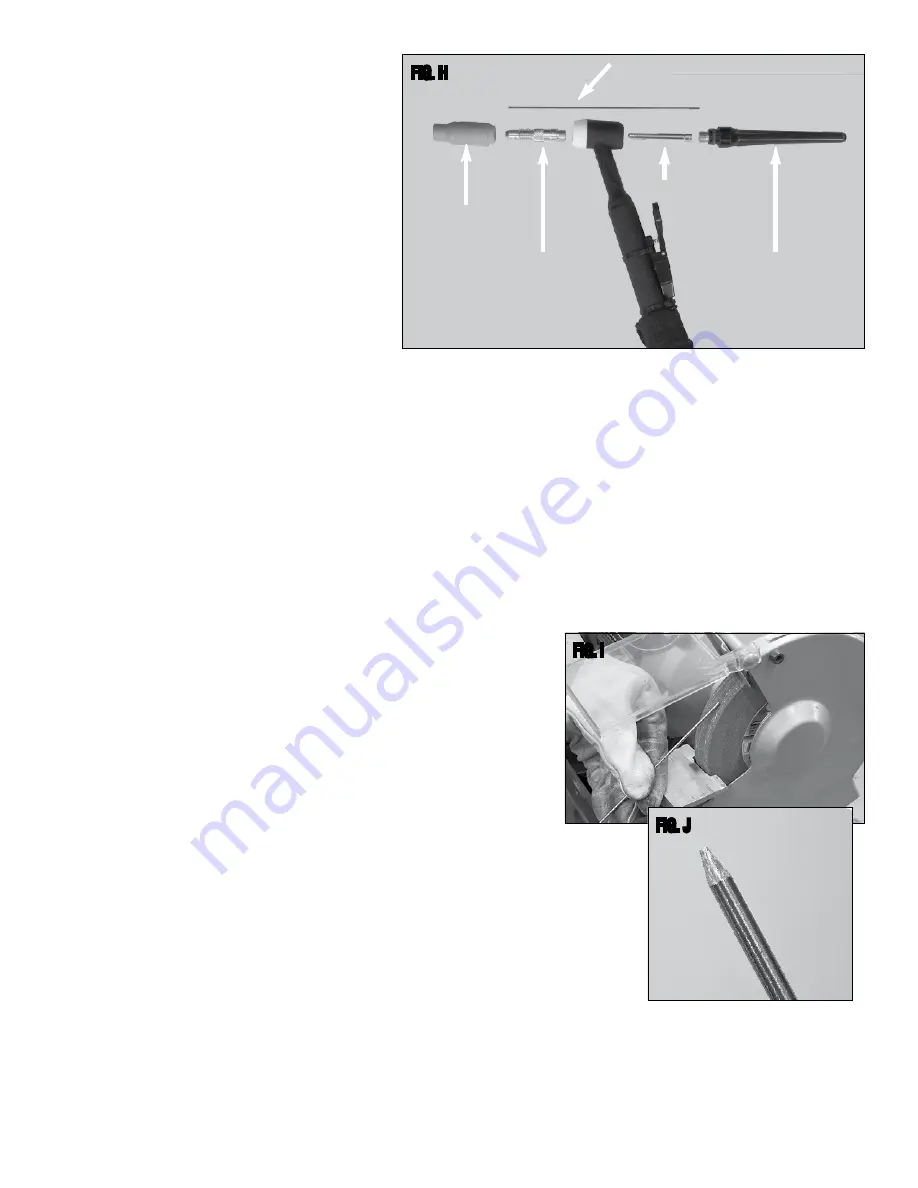
To order parts and supplies: 800.345.1178 >> eastwood.com
7
PREPARING TO wELD
TORCH DISASSEMBLY/ASSEMBLY
DISASSEMBLY:
1. Make sure the welder is turned off and unplugged.
2. Remove the back cap from the torch.
3. If there is a tungsten installed in the torch pull
it out of the front of the torch
4. Slide the collet out of the torch.
5. Unscrew and remove the gas nozzle.
6. Unscrew and remove the collet body.
ASSEMBLY:
1. Select a collet body that matches your tungsten diameter size and thread it back into the front of the torch.
2. Select a collet that matches your tungsten diameter size. Insert the tungsten into the collet and put the collet and tungsten back
into the torch.
3. The cup size should be changed according to shielding gas requirements for the material being welded. This size can be referenced
on the suggested settings chart. Select the correct gas nozzle and thread it onto the collet body.
4. Reinstall the back cap to lock the tungsten in place. Always make sure the tungsten protrudes 1/8” to 1/4” beyond the gas nozzle.
SHARPENING THE TuNGSTEN
To avoid contamination of the Tungsten and ultimately the weld, it is imperative to have a dedicated grinding wheel used for Tungsten
grinding only. A fine grit standard 6” synthetic stone grinding wheel on a bench top grinder is sufficient
or specifically designed Tungsten Grinders are available.
1. Shut off the welder.
2. Make sure the Tungsten and Torch are sufficiently cooled for handling then
loosen and remove the Back Cap then the Collet (Fig H) and remove the
Tungsten from the FRONT of the Torch only. (Removing from the rear will
damage the Collet).
3. If the tungsten is used and the end is contaminated, use pliers or a suitable
tool to grip the tungsten above the contaminated section and snap off the end
of the Tungsten.
4. Holding the Tungsten tangent to the surface of the grinding wheel, rotate the
tungsten while exerting light pressure until a suitable point is formed (Fig I).
5. The ideal tip will have the length of the conical portion of the sharpened area at
2-1/2 times the Tungsten rod diameter (Fig J).
6. Replace the Tungsten in the Collet with the tip extending 1/8”-1/4”
beyond the Gas Nozzle, then re-tighten the Back Cap.
FIG. I
FIG. J
Gas Nozzle
✑✒✓
✔
Collet Body
✑✒✓
✔
Collet
✑✒✓
✔
Back Cap
✑✒✓
✔
✑✒✓
✔
Tungsten
FIG. H