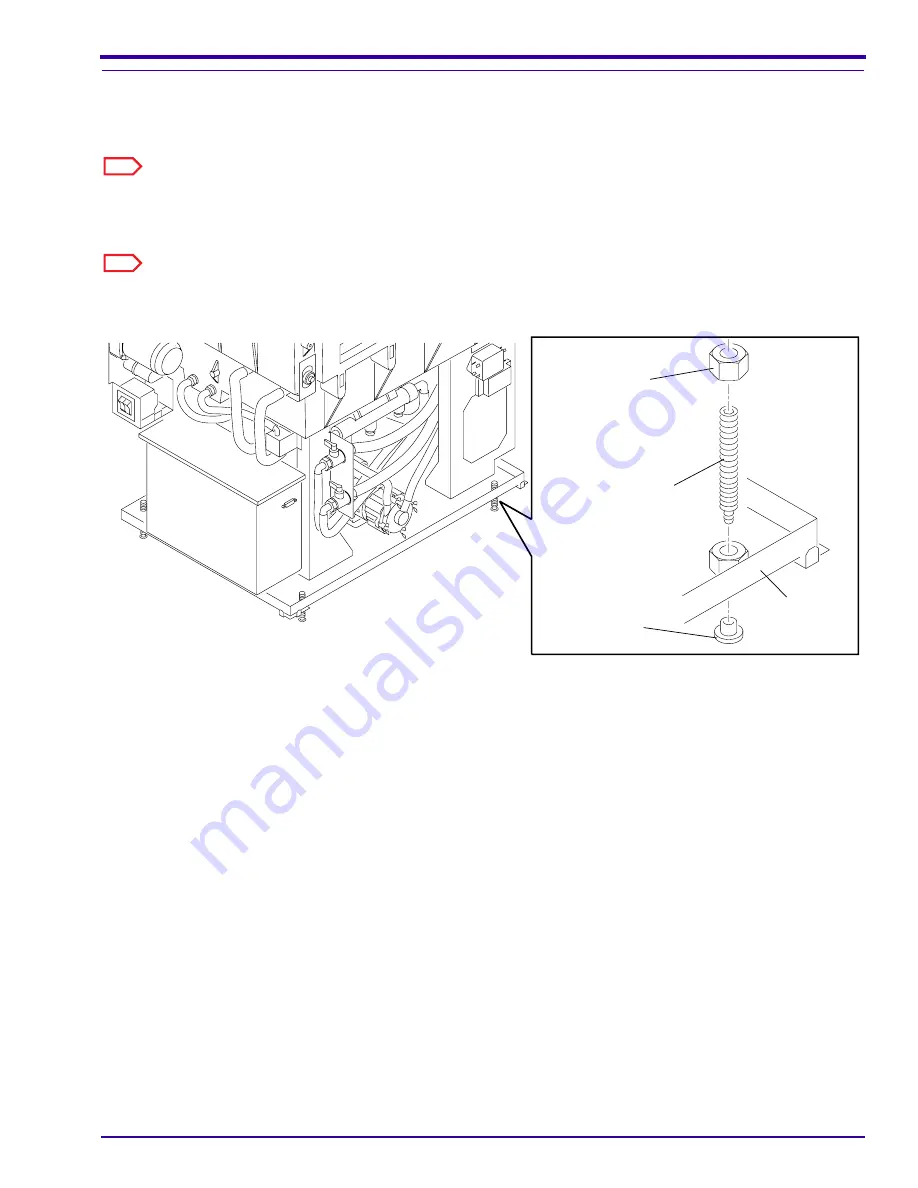
Preparing the PROCESSOR for Installation
1C7836 – February 1996
15
Moving the PROCESSOR into Position and Leveling the PROCESSOR
[1] Install the LEVELING SCREW into the PROCESSOR BASE.
[2] Install the LEVELING FOOT by rotating it counterclockwise onto the LEVELING SCREW.
Note
The LEVELING FOOT must be past the threads so that it pivots on the end of the LEVELING SCREW. Check that
the LEVELING FOOT remains in this position until it touches the floor.
[3] Install the JAM NUT.
Note
Do not tighten the JAM NUT.
[4] Install the other 3 LEVELING SCREWS.
H127_0083BA
H127_0083BCA
FOOT
LEVELING
BASE
PROCESSOR
LEVELING SCREW
JAM NUT