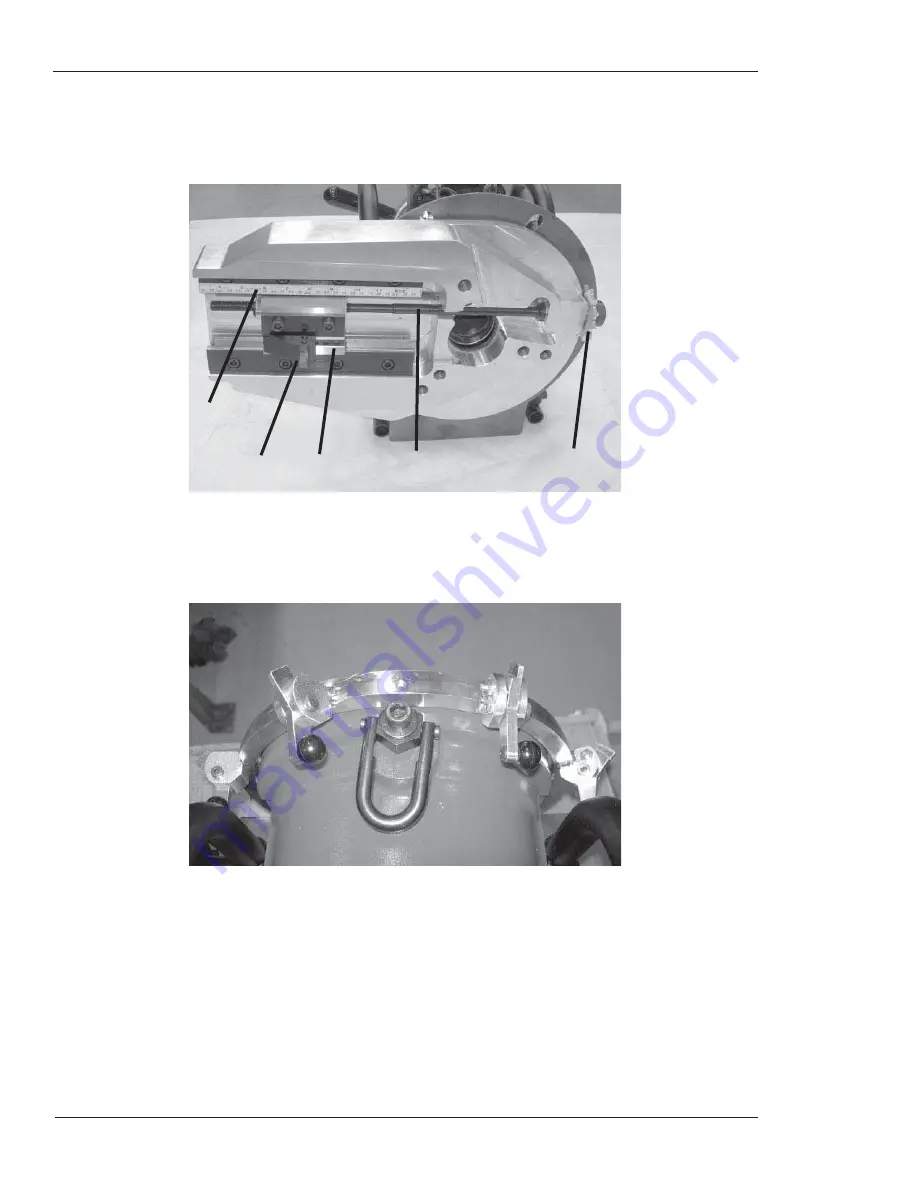
EP 424 End Prep Machine
12
Part No. 81-MAN-00, Rev. C
E.H. Wachs
The single-point confi guration includes the following addi tional components:
• single-point
slide
Starwheel
Feed screws
Male tool slide
Tool holder
Feed gauge
Figure 3-3. The single-point slide feeds the tool radi ally across the pipe face. It is driven
along a feed screw by a starwheel.
•
radial feed trip assembly
Figure 3-4. The photo shows the trip assembly mounted on the main drive housing.
Содержание EP 424
Страница 6: ...EP 424 End Prep Machine iv Part No 81 MAN 00 Rev C E H Wachs ...
Страница 10: ...EP 424 End Prep Machine 4 Part No 81 MAN 00 Rev C E H Wachs ...
Страница 30: ...EP 424 End Prep Machine 24 Part No 81 MAN 00 Rev C E H Wachs Standard Mandrel Dimensions Leg Chart 81 303 00 ...
Страница 34: ...EP 424 End Prep Machine 28 Part No 81 MAN 00 Rev C E H Wachs ...
Страница 92: ...EP 424 End Prep Machine 86 Part No 81 MAN 00 Rev C E H Wachs ...
Страница 98: ...EP 424 End Prep Machine 92 Part No 81 MAN 00 Rev C E H Wachs ...
Страница 126: ...EP 424 End Prep Machine 120 Part No 81 MAN 00 Rev C E H Wachs ...
Страница 129: ... ...
Страница 130: ...600 Knightsbridge Parkway Lincolnshire IL 60069 847 537 8800 www ehwachs com ...