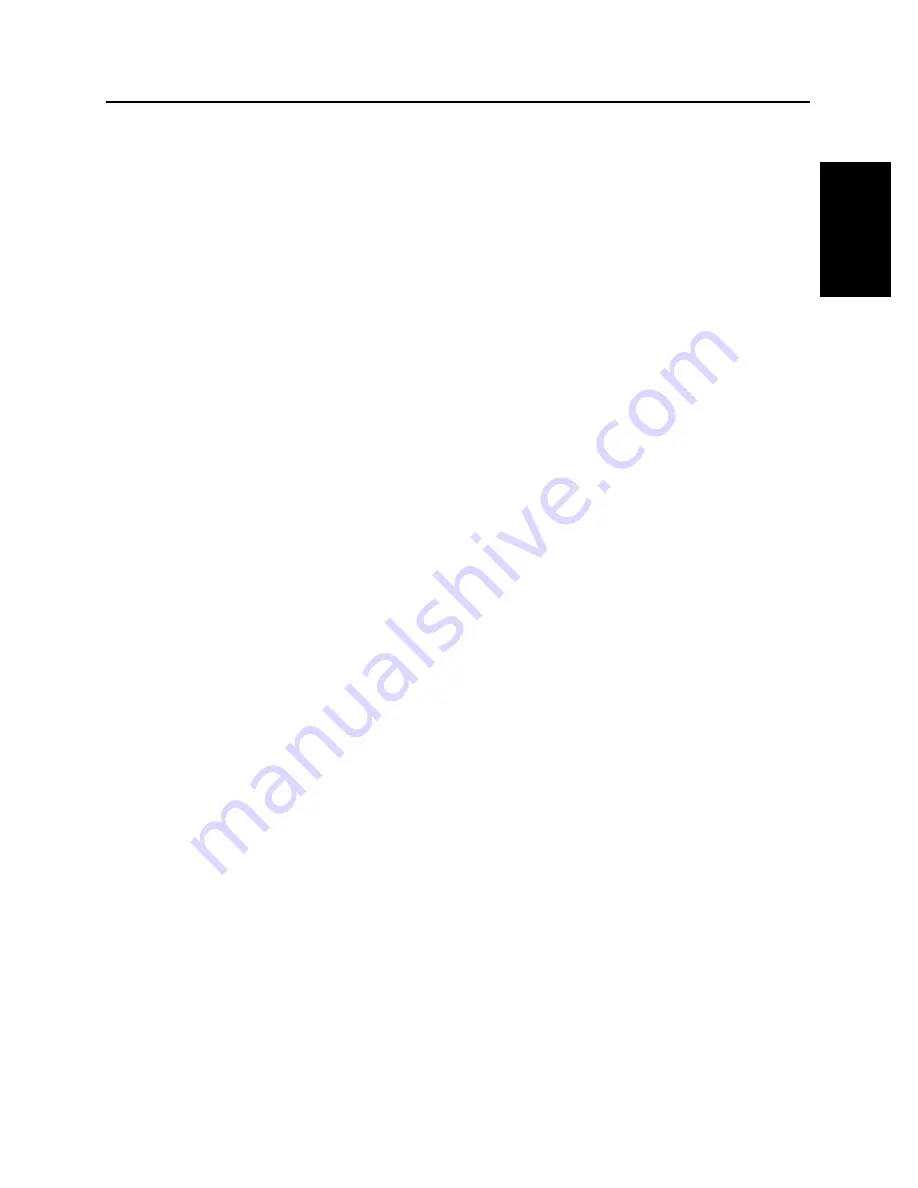
Troubleshooting
7-7
Maintenance and
Troubleshooting
Hook
Problem:
Hook will not open
Possible Solutions:
•
Check the safety enclosure doors and make sure that the air supply is on. The hook
should open by simultaneously pressing the yellow ARM button and the red FIRE
button. The ARM button must be illuminated, and the FIRE button must light when
pressed with the ARM button. If the ARM button is not illuminated, the interlocks
are indicating an unsafe condition. Check the safety enclosure doors and make sure
that the air supply is on. Once the ARM and FIRE buttons are pressed, it may take
up to 5 seconds for the weight to drop.
•
Check switch next to hook for damage. Contact Instron Dynatup if you suspect it is
damaged.
Problem:
Hook will not close
Possible Solution:
•
Check the switch next to the hook for damage. Contact Instron Dynatup if you
suspect it is damaged.
Other Problems
Problem:
Abnormal Velocity
Possible Solution:
•
Check that the guide columns are free from dirt; the weight sets are not bent or
damaged, the flag is not loose or damaged, and that the velocity detector block is not
damaged.
Problem:
Abnormal data collection
Possible Solution:
•
Check the mounting of the tup, tup insert, specimen or fixture; check that the velocity
detector or flag is properly adjusted. Problems with data or data collection are often
unrelated to the data system.
Содержание 8250
Страница 1: ... M14 13655 EN Operating Instructions Instron Dynatup 8250 Drop Weight Impact Tester ...
Страница 10: ...Preliminary Pages M14 13655 EN x ...
Страница 29: ...Connecting Utilities and Initial Set up 3 7 Installation Figure 3 3 Motor Enclosure ...
Страница 34: ...Initial Machine Operation and Checkout M14 13655 EN 3 12 ...
Страница 49: ...6 1 Operation Chapter 6 Chapter 6 Operation Outline Performing a Test 6 2 ...
Страница 54: ...Performing a Test M14 13655 EN 6 6 ...
Страница 58: ...Scheduled Maintenance M14 13655 EN 7 4 Figure 7 1 Lubrication Points LUBRICATION POINTS ...
Страница 62: ...Troubleshooting M14 13655 EN 7 8 ...
Страница 64: ...Glossary M14 13655 EN A 2 ...