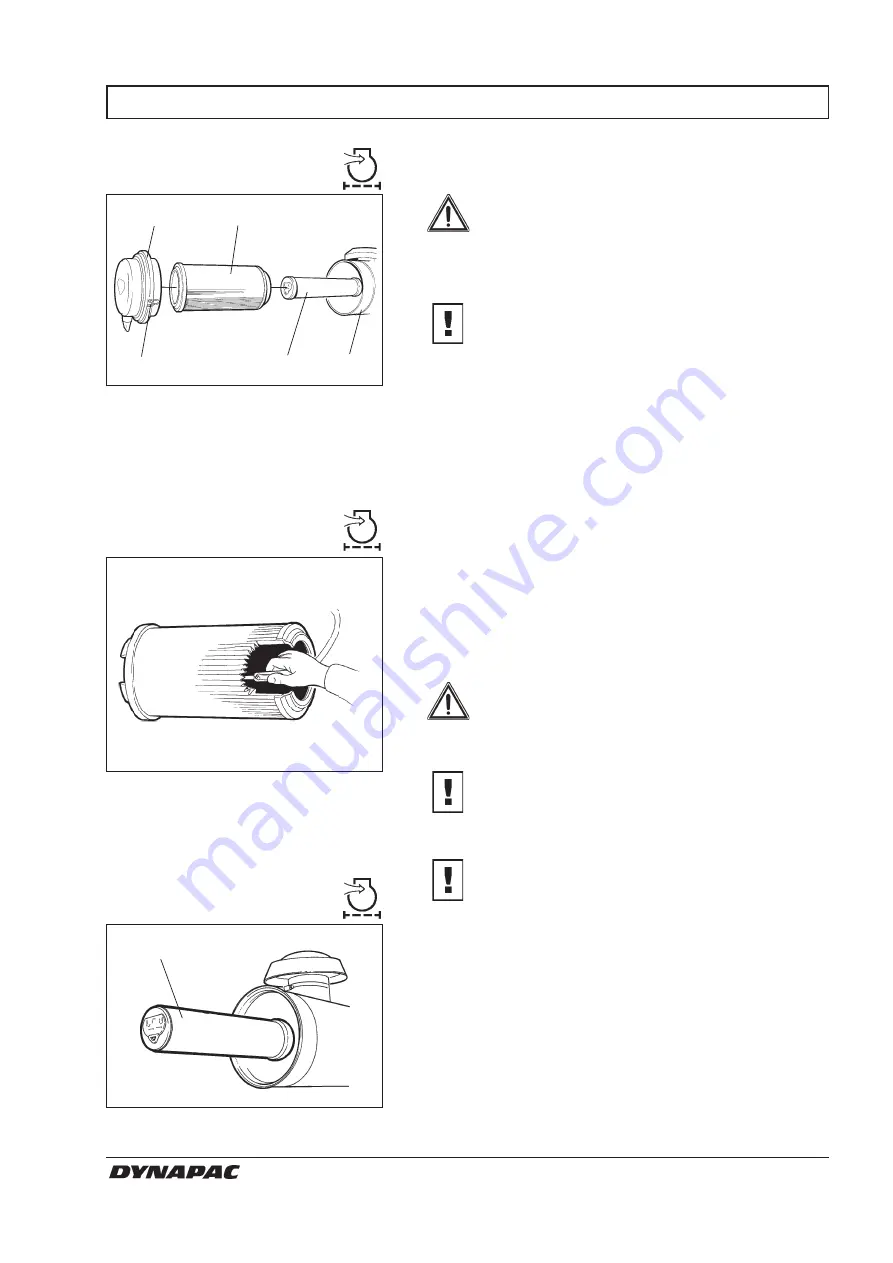
13
CS 141 M141EN4
EVERY 50 HOURS OF OPERATION (Weekly)
Air cleaner
– Check/Cleaning
Main filter – Cleaning with
compressed air
Fig. 15 Main filter
2
3
Fig. 14 Air cleaner
1. Locking braces
2. Cover
3. Main filter
4. Backup filter
5. Filter housing
Place the roller on a level base. The engine
must be switched off and the reserve/
parking brake knob pushed in for all check-
ing and adjustments on the roller unless
otherwise specified.
Replace or clean the main filter of the air
cleaner when the warning lamp on the instru-
ment panel lights at full engine revs.
Release the three locking braces (1) and pull off the
cover (2), pull out the main filter (3).
Do not remove the backup filter (4).
1
4
5
Fig. 16 Air filter
4. Backup filter
Backup filter
– Replacement
4
Use compressed air at a maximum pressure of 5 bar
(72 psi) to clean the main filter by blowing up and down
along the inside of the pleated paper filter.
Hold the air nozzle at least 2 to 3 cm (0.8-1.2 in) from
the paper pleats so as not to tear the paper.
Use protective goggles when working with
compressed air.
Wipe the inside of the cover (2) and the filter housing (5).
Ensure that the hose clips between the filter
housing and the intake hose are tightened and
that the hoses are intact. Inspect the entire
hose system all the way to the engine.
Change the main filter after cleaning it five
times.
Replace the backup filter with a new one after cleaning
or changing the main filter five times. The backup filter
cannot be cleaned and reused.
To change the backup filter (4), pull out the used filter
from its holder, insert a new filter and reassemble the
air cleaner in the reverse order.
WARNING
CAUTION
WARNING
CAUTION
CAUTION
Содержание CS 141
Страница 2: ...19 ILF015WO1...
Страница 29: ...27 CS 141 M141EN4...