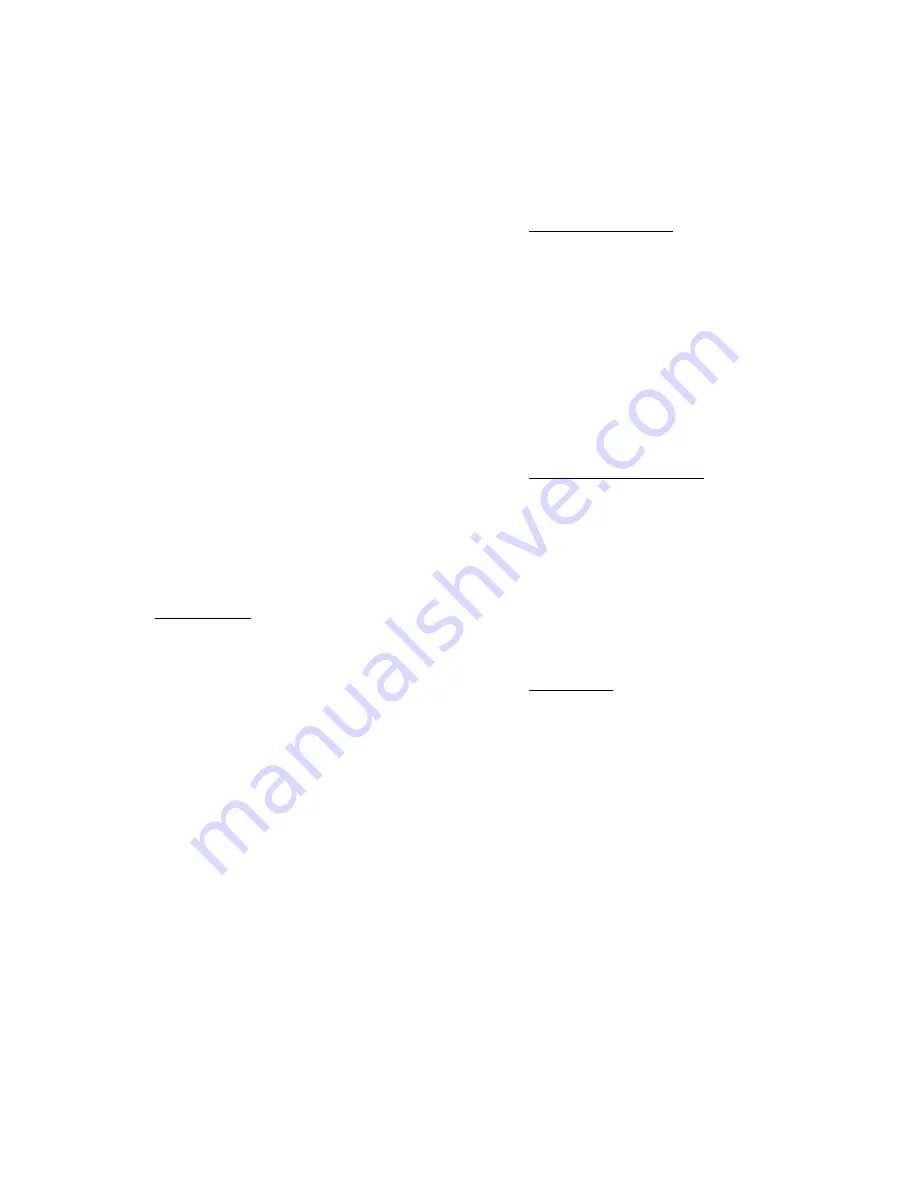
14
2. Manually load the compressor(s) to full load.
This can be done one compressor at a time if
necessary.
3. Locate the amps and full load amps (FLA)
analog locations from the analog input menu
for the compressor being calibrated.
4. When the compressor(s) are at full load and
conditions are close to design, record the
amps and FLA analog values.
5. If the values do not match within 2-3 amps,
do the following calculation: AMPS - FLA
6. Locate the amps calculation A setpoint for the
compressor from the setpoint menu.
The setpoint is labeled FLA # CON, where
is 1 through 4 for each compressor number. 7.
7. Add the value obtained in step 5 to the amps
calculation A setpoint value from step 6.
8. Change the amps calculation setpoint to the
new value.
9. Verify that amps and FLA now match closely.
10. Manually unload the compressor all the way.
11. Locate the percent full load capacity (%FLCP)
for the compressor from the analog input
menu and record the value.
12. If the value is 25% ±3%, no change is re-
quired. If the value is less than 22% or greater
than 28%, locate the %FLA # CON setpoint B.
If the setpoint is equal to 25.0, change it to
the value observed in step 11 and proceed to
step 13. If the setpoint is not equal to 25.0,
change it to 25.0 and repeat steps 11 and 12.
13. Repeat this procedure for each compressor.
4.1.2
Manual Control
To place a compressor in manual control,
which turns it on, use the following proce-
dure:
1 . Log in for authorization.
2. Address desired compressor (1, 4, 7, or 10
control point).
3. Press ENTER to modify status.
4. Use up or down arrow keys to select ON
MAN.
5. Press ENTER. The compressor will start or
continue to run in hold state.
6. Press 0 to return to computer control, 1 to
hold, 2 to load, 3 to unload. Note:
Compressors will not load past amp limits.
7. Use menu key or arrows to access other
data.
If a safety condition is exceeded while oper-
ating manually, the compressor will shutdown.
To put all compressors back into computer
control from a locked off state, press RESET.
Screw compresors can be controlled manually
with the key pad. A compressor can be turned
on, off, or placed in computer control. When a
compressor is controlled manually, it can be com-
manded to load, hold, or unload. If current limit
is active, it will not accept a load command.
CAUTION:
Anti-recycle timer is bypassed by
NOTE:
All compressors will revert back to auto-
matic control if the computer is not given a
load, unload or hold command at least once
every 15 minutes. A command can be repeated
to meet the 15 minute requirement for manual
control.
4.2. Staging of Compressors
The staging of compressors is based on leaving
water temperature and the capacity calculations
mentioned in section 4.1. When the percent
capacity target gets up to full load and tempera-
ture is above deadband, a time delay of one or
two minutes is initiated before starting the next
compressor. When the capacity target falls below
a stored setpoint and temperature is below the
deadband, a compressor is turned off.
The percent capacity values that the computer is
calculating can be displayed by addressing the
analog input menu.
4.3. Compressor Current Limiting
The amp limit B setpoint on the unit control data
sheet is the amp value at which the compressor
will be prevented from loading. The amp limit A
setpoint is the amp value at which the compres-
sor will be given an unload command until the
current drops below the A setpoint.
If the values are changed, the difference be-
tween the hold and unload points should not be
decreased below 10% of compressor RLA so that
oscillations will not occur.
4.4. Ramp Control
Ramp control can be implemented with the
microcomputer. Whenever the unit starts with
leaving water temperature greater than 5°F
above setpoint, a ramp up is generated. The
ramp start B setpoint specifies the percent
capacity target at which the ramp begins on the
first compressor. This can be set between 25 &
100 percent. The ramp rate A setpoint specifies
the maximum amount that can be added to
the target at each compressor control interval.
Thus a ramp rate of 0.1 produces the longest
ramp rate. Table 1 gives sample ramp times for
various ramp rate setpoints and start points for a
two-compressor machine.
TABLE 1
Sample Ramp Times (Minutes) For a Two-
Compressor Unit with a 2 Second Compressor
Control Interval
Ramp 25% 50% 75%
Rate
Start Pt. Start Pt. Start Pt.
Setpoint Setpoint Setpoint Setpoint
.1
38
50
42
.2
29
25
21
.3
19
17
14
.4
15
12
10
manual control. DO NOT start a compressor more
than once every 15 minutes.
Содержание HRSC - D
Страница 20: ...19 TYPICAL HRSC 150 POWER WIRING 460 3 60 COMPRESSOR MOTORS 1 2 SEE NOTE 5...
Страница 21: ...20 TYPICAL HRSC 150 CONTROL WIRING Electrical Mechanical...
Страница 22: ...21 TYPICAL HRSC 150 CONTROL WIRING Optional Micro Computer Controller...
Страница 23: ......
Страница 29: ......
Страница 30: ......