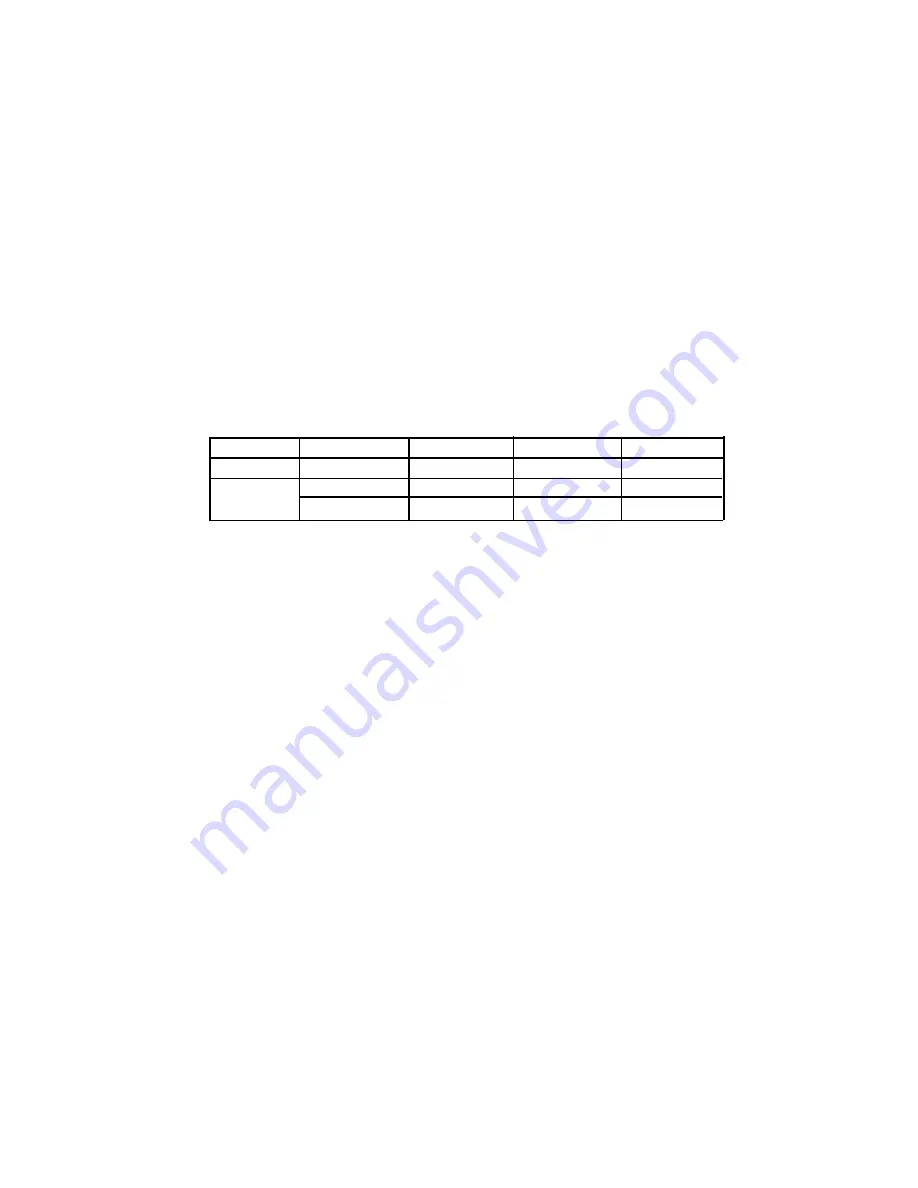
CONDENSER HEAD PRESSURE CONTROL
General
All units require some means to keep the condensing pres-
sure high enough to insure adequate expansion valve feed
to the cooler to prevent low side pressure trips, particularly
during cold starts.
THE RECOMMENDED SPD-SD REMOTE AIR COOLED CON-
DENSER
Standard Factory Installed Fan Cycling
This commonly applied scheme cycles condenser fans “on”
and “off “ in response to head pressure to maintain the head
pressure within an acceptable range for proper system op-
eration. This method will permit starting and sustained run-
ning to 30°F ambient.
T
he minimum ambient shown above reflects the performance
of the condenser surface exposed to the operational fan(s)
as well as that portion of the surface rejecting heat by natu-
ral convection with related fans “off”. To further assist low
ambient starts, all fans are held “off” until the head pressure
reaches 260 psig. This alone cannot insure sustained opera-
tion if the system load is not high enough to produce the
minimal pressures required.
Operational Variable Speed Fan Control
This scheme utilizes fan cycling but also adds speed control
to the lead fan of each refrigerant circuit. This feature not
only serves to stabilize the head pressure between normal
fan staging but also allows for virtually “no fan” operation
down to 0°F ambient.
SPD-SD
FAN CYCLING CONTROL SETTINGS
CUT-IN/CUT-OUT)PSIG)
HRSC100-150
SEQUENCE OF OPERATION (TYPICAL) MODELS
UNIT
FCP1
FCP2
FCP3
FCP4
070
260/160
275/175
285/210
295/235
FCP1 & 2
FCP3 & 4
FCP5 & 6
FCP7 & 8
260/160
275/175
285/210
295/235
The following sequence of operation is typical for all Electro-
mechanical HRSC models. Refer to the wiring diagram fur-
nished with the unit for specific information.
Important Note!
With all the control circuit switches (SW1-SW3) in the “off”
position and the staging thermostat (T1) to its highest tem-
perature, there must be a 115 volts supplied to the compres-
sor crankcase heaters (CCH1,2) for a minimum of 24 hours.
Preliminary Sequence
Close the main power disconnect switch. Check to see that
the red indicating light on the phase loss monitor (PLM1) is
lit. (Note: There will be two phase loss monitors, (PLM1) and
(PLM2) on dual power block models). This light must be on
to indicate proper phase rotation for the compressors. If the
light is not on, disconnect the main power and reverse any
two phase legs at the Main Incoming Power Terminal Block.
(Warning! DO NOT REVERSE THE LEADS ON THE PHASE
LOSS MONITOR FOR THIS WILL ALLOW THE COMPRESSORS
TO RUN BACKWARDS, CAUSING SEVERE DAMAGE, AND
WILL VOID THE COMPRESSOR WARRANTY!).
The crankcase heater relay contacts are closed and are sup-
plying power to the compressor crankcase heaters.
Control power goes through the control panel circuit breaker
(CB1) and customer supplied control (if supplied).
Start up the chilled water pump. An auxiliary contact on the
chilled water pump closes. The water flow is confirmed when
the water flow switch completes the electrical circuit. Set
the thermostat (T1) to the desired leaving water tempera-
ture (e.g. 44°F.). Set point Adjustment is accomplished di-
rectly on the control.
9
Place the three (3) control circuit switches (SW1-SW3) in the
“On” position, thus energizing the balance of the control
circuit. The system will be in the “Time-In” mode for five
minutes before the first compressor will start.
The low temperature freezestat (T2) must also be satisfied to
allow compressor operation.
Stage 1 Loading
Upon demand for cooling, the first step of the staging ther-
mostat (T1) will close energizing relays (R1) and time delay
(TD1). If all the safety controls and switches are closed, (see
“Safety Controls” section for more detail) the control circuit
for Compressor No. 1 will energize, allowing the compressor
to start. Power is supplied to condenser fan interlock termi-
nal CT19 and CT2 to enable the remote condenser fan cir-
cuit. Relay (R5) will energize, closing the normally open set
of contacts, which energizes the liquid line solenoid valve
(SOL1). Another set of normally open contacts on (R5) pro-
vide a series interlock with all the safety and operating con-
trols, which will lockout the compressor if any safety trips
during normal operation. (See Note 6 on Wiring Diagram).
The last set of normally closed contacts on (R5) open and de-
energizes (CCH1).
Time Delay (TD1) has two (2) sets of contacts: The first set of
(TD1) normally closed contacts provides a 30 second jumper
around the low pressure control (LP1) to prevent short cy-
cling during start-up. The second set of (TD1) normally closed
contacts powers the unloader solenoid (UL3-1) which holds
the compressor in the full unload position for 30 seconds.
After (TD1) times out (30 seconds), the contacts for the
unloader solenoid (UL3-1) open and the normally open con-
tacts close, which energizes the relay (R3). Upon energizing
relay (R3) the normally open contacts of relay (R3) are closed,
allowing the thermostat (T1) to energize the load (UL1-1)
and the unload solenoid (UL2-1) upon demand.
140
Содержание HRSC - D
Страница 20: ...19 TYPICAL HRSC 150 POWER WIRING 460 3 60 COMPRESSOR MOTORS 1 2 SEE NOTE 5...
Страница 21: ...20 TYPICAL HRSC 150 CONTROL WIRING Electrical Mechanical...
Страница 22: ...21 TYPICAL HRSC 150 CONTROL WIRING Optional Micro Computer Controller...
Страница 23: ......
Страница 29: ......
Страница 30: ......