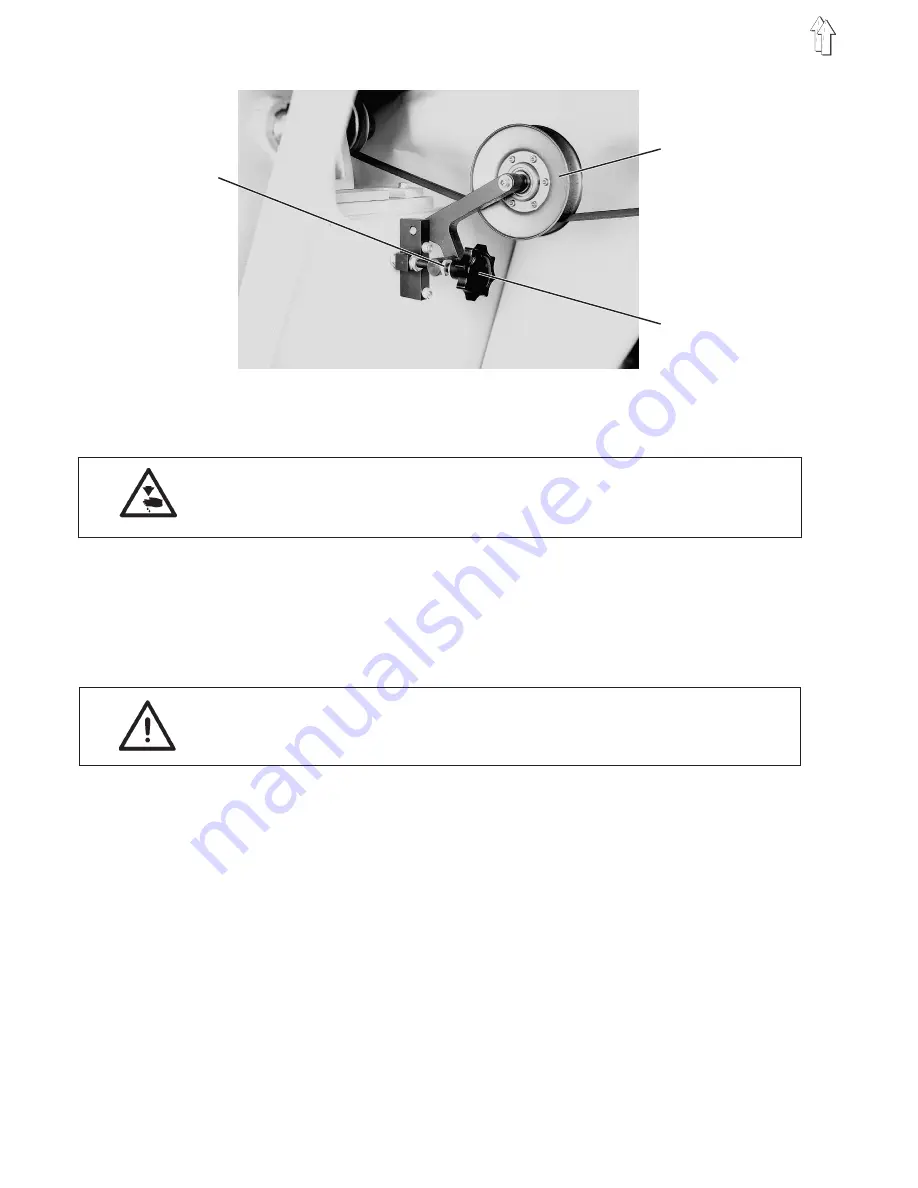
4.2
Changing the Stitch Length
The tension pulley 2 on the V-belt determines the stitch length.
The belt adjustment gearing on the motor is changed by the tension. A
stitch length of 1.8 mm is set at the factory.
Caution Risk of Injury !
Turn the main switch off.
Change the stitch length only with the sewing unit turned off.
–
Loosen lock nut 1.
–
Turn the star knob 3.
Shorter stitches
= Tension pulley lower
Longer stitches
= Tension pulley higher
–
Tighten the lock nut 1.
ATTENTION !
After a stitch length change the following points must be observed.
–
The performance of the sewing unit has changed.
–
The position of the sew-on point has changed.
Set the seam beginning again !
–
If the positions of the sew-on points of the right and left clamping
tables do not agree, then the stitch length has been set differently.
Set the stitch length again !
2
3
1
32