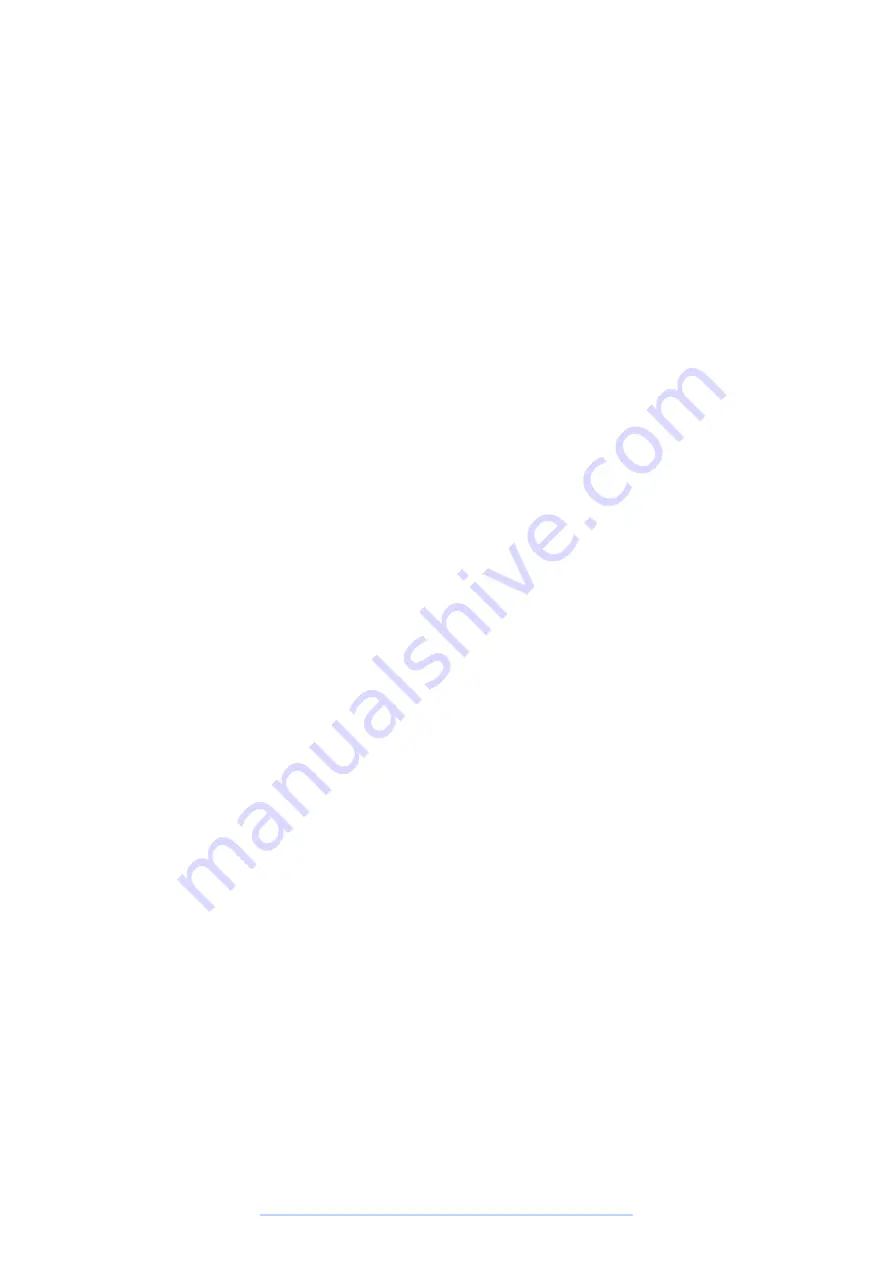
16
4. Stitch skipping.
5. Incorrect stitch locking. Threads are
locked on top side of sewn mate-
rial.
6. Incorrect stitch locking. Threads are
locked on bottom side of sewn ma-
terial and increasing of tension is
of upper thread no help.
7. Stitches insufficiently tightened and
with irregular positioning. Thread
unravelled.
8. Sewn material wavy in seam.
9. Machine does not feed or is feeding
slowly or in reverse sense.
10. Difficult and iregular machine feed.
11. Hook blocked.
3.5 Needle too thick with regard to
thickness of thread and sewn ma-
terial.
4.1 Needle incorrectly inserted.
4.2 Too big distance between needle
and hook point.
4.3 Incorrectly set needle hook timing
or needle height.
4.4 Excessively elastic material or ex-
cessively elastic thread.
4.5 Damaged hook point.
5.1 Lower thread tension.
5.2 Incorrect threading and tension
setting of upper thread.
6.1 Upper thread out of tensioning
dishes.
6.2 Opening bobbin case lifter incor-
rectly set (it opens too little).
6.3 Wheel feeder too low - difficult pas-
sage of thread between sewn ma-
terial and throat plate.
6.4 Upper thread insufficiently tensio-
ned when passing through hook.
7.1 Low tension of upper and lower
threads.
7.2 Upper thread insufficiently tensio-
ned when passing through hook.
7.3 Thin needle with regard to thread
thickness.
8.1 Thread tension to high for sewn
material.
9.1 Overrun safety clutch against hook
overload.
10.1 Wheel feeder too low (especially
when sewing soft and thick ma-
terials).
10.2 Feeder teeth unsuitable (too fine)
for sewn material.
10.3 Wheel feeder driving chain too
tensioned - blocked feeding.
11.1 Incorrect lower thread threading
when replacing hook bobbin -
lower thread caught by hook point.
Use thinner needle.
Insert needle according to NP, par. 6.5.
Set according to SK, par. 3.1.3 and 3.1.5.
Set according to SK, par. 3.1.4 and 3.2.3.
Increase timing as needed and set the
needle bar height according to SK, par.
3.2.3.
Replace hook.
Set according to NP, par. 6.4.
Thread according to NP, par. 6.1 set
according to NP, par. 6.4.
Thread correctly according to NP par. 6.1.
Set according to SK, par. 3.1.6.
Set wheel feeder height according to SK,
par. 3.5.3.2.1.
Shift thread limiter to the right and to
the top according to SK, par. 3.4.5 or by
more than the value quoted there.
Set tension according to NP, par. 6.4.
Shift thread limiter to the top and to the
right according to SK, par. 3.4.5 or more
than the value quoted there.
Use a thicker needle.
Reduce tension of both threads.
Engage correctly clutch according to NP,
par. 6.10.
Raise feeder more from throat plate ac-
cording to SK, par. 3.5.3.2.1.
Use feeder with 0.6 mm teeth pitch.
Replace according to SK, par. 3.5.3.2.2.
Set chain tension according to SK, par.
3.5.3.2.1.
Thread lower thread according to NP, par.
6.3.
www.promelectroavtomat.ru
Содержание 4181i
Страница 38: ...13 www promelectroavtomat ru...