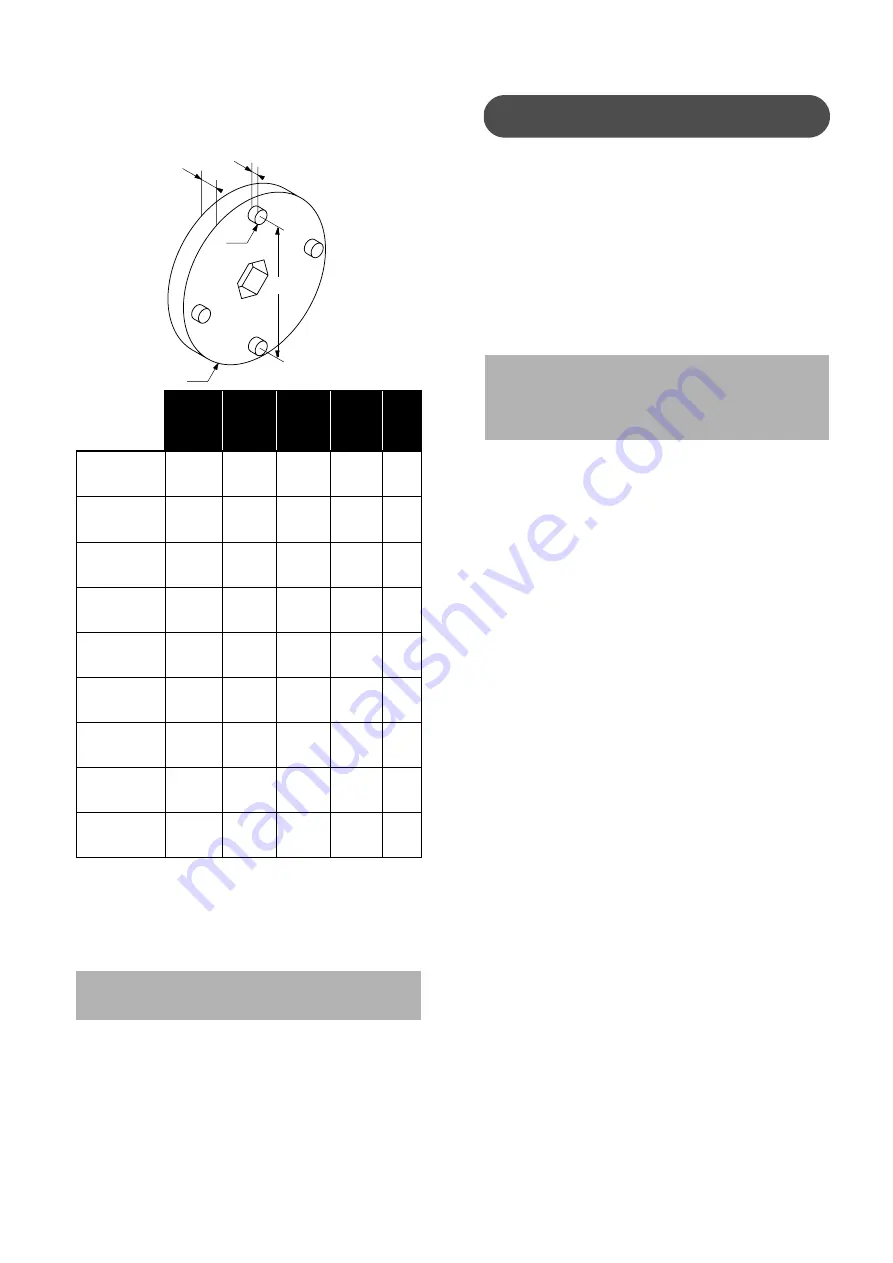
Instruction No EF 5000 E
01/2004
9
Figure 6 shows the recommended thickness and
method of construction along with specific
dimensions to facilitate construction.
A.
Secure the valve body in a vise or appropriate
holding device with the plug side facing up (refer
to figure 16).
B.
Place DVD plate wrench so it engages retainer
lugs.
C.
Engage the retainer wrench with an impact
wrench or suitable wrench and loosen, then
remove DVD (105) by turning counter-clockwise.
9.1
SPRING DIAPHRAGM
REPLACEMENT
(Refer to figures 16 and 17)
The recommended maintenance to be performed on
the Camflex® II Spring Diaphragm Actuator is limited
to the replacement of the diaphragm (40). Removal
of the actuator from the valve is not required. To
replace the diaphragm, proceed as follows:
Handwheel (53) and limit stop (77) must be backed
off to allow free travel of the lever (34).
A.
Bypass the valve, shut off stop valves and isolate
valve in compliance with CAUTION note listed
above.
B.
Shut off and disconnect air supply tubing to the
actuator.
C.
Remove the four capscrews (41) from
diaphragm case (42) and remove diaphragm
case.
D.
Remove diaphragm (40).
Note: Diaphragm is glued to the top of the
piston (43).
E.
Removed tape or glue from the top of the piston
and clean thoroughly
F.
Clean diaphragm case (42) and spring barrel
(38) at the area that engages the diaphragm
bead in preparation for reassembly.
Note: To hold the diaphragm in place on the
piston, an adhesive disc (adhesive both sides) or
rubber cement is used. If rubber cement is used,
it should be applied to both the piston and the
diaphragm or in accordance with the
manufacturer's directions for the adhesive used.
For recommended adhesives see figure 15.
G.
Apply adhesive tape or cement to the top of the
piston.
H.
The inscription "Piston Side" is located on the
diaphragm (40). if used, apply cement to this
side of the diaphragm.
I.
Center and adhere diaphragm (40) to the top of
the piston (43) (see figure 7, step A).
A
mm
(in)
d
mm
(in)
D
mm
(in)
H
mm
(in)
T
mm
(in)
DN 25
(1”)
27
(1.063)
3.6
(0.142)
2
(0.079)
2
(0.079)
10
(0.4)
DN 40
(1”
½
)
38
(1.496)
4
(0.157)
3
(0.118)
3
(0.118)
12
(0.4)
DN 50
(2”)
49
(1.929)
4
(0.157)
3
(0.118)
3
(0.118)
18
(0.7)
DN 80
(3”)
74
(2.913)
4.5
(0.177)
4
(0.157)
4
(0.157)
20
(0.8)
DN 100
(4”)
98
(3.858)
5
(0.197)
7
(0.275)
7
(0.275)
20
(0.8)
DN 150
(6”)
150
(5.905)
6
(0.236)
9
(0.354)
9
(0.354)
25
(1.0)
DN 200
(8”)
201
(7.913)
6
(0.236)
10
(0.394)
10
(0.394)
25
(1.0)
DN 250
(10”)
250
(9.843)
6
(0.236)
10
(0.394)
10
(0.394)
30
(1.2)
DN 300
(12”)
298
(11.732)
7
(0.276)
12
(0.472)
12
(0.472)
30
(1.2)
Figure 6
Caution: Care must be taken to avoid damage
to the gasket face on the valve body.
A
H
T
d
D
Caution: The valve must be isolated and free
from any service pressure. All electrical or air
pressure to component parts must be off.
Pressure to the actuator must be relieved.
9. Maintenance