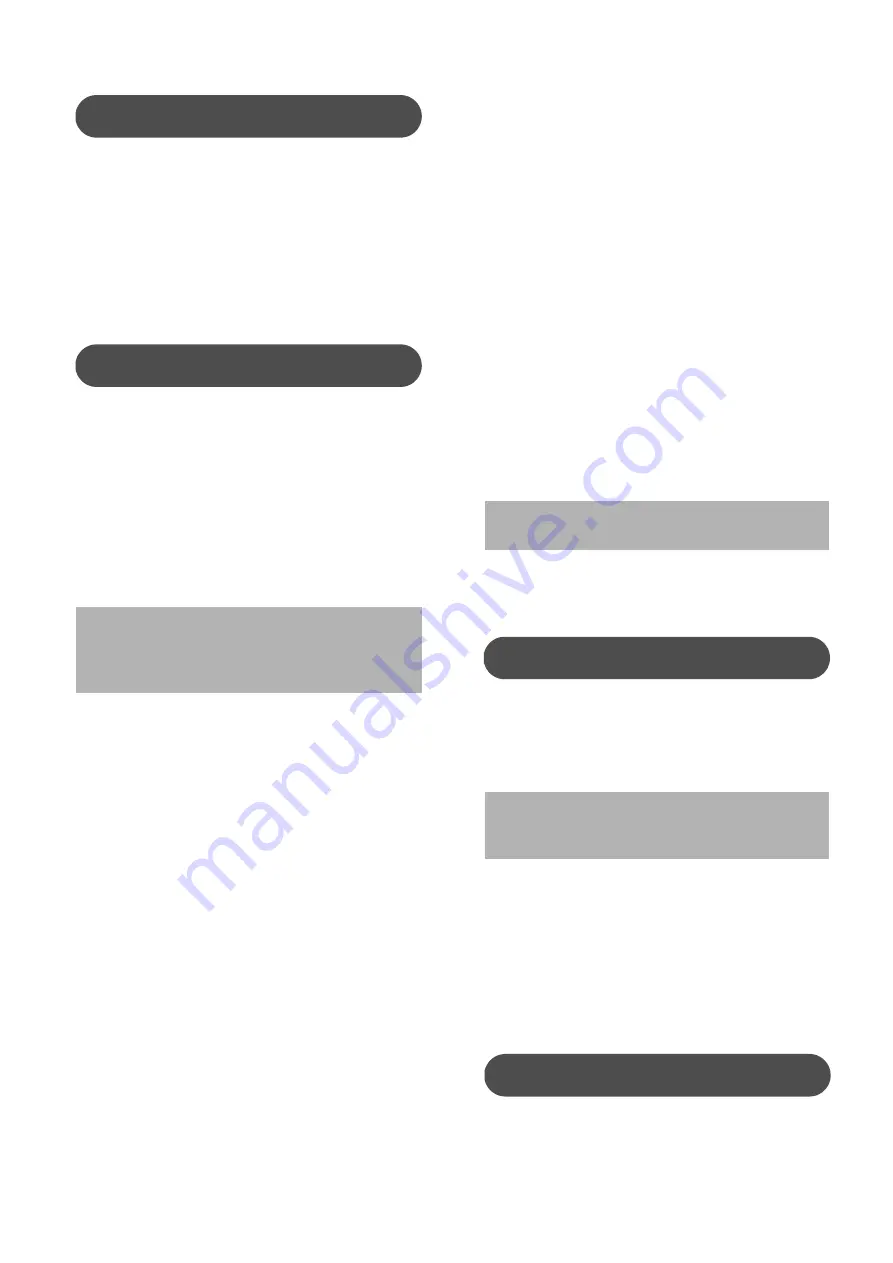
Instruction No EF 5000 E
01/2004
5
Care must be exercised when unpacking the valve to
prevent damage to the accessories and component
parts. Should any problems arise, contact the
Masoneilan Representative or District Office.
Note: For ease of shipment and to prevent damage,
valves equipped with the spring diaphragm actuator
are shipped with the handwheel unassembled. Refer
to section 10.3 for handwheel assembly procedures.
The Camflex® II valve has been assembled at the
factory in accordance with specify instructions
concerning flow direction and actuator mode. The
valve must be installed so that the controlled
substance will flow through the valve in the direction
indicated by the flow arrow (25), which is located on
the upper part of the valve body neck. The valve
actuator should be installed so the actuator is above
the centerline of the shaft. To install the valve in the
line, proceed as follows:
A.
Check the model number on the serial plate (56)
against the numbering System described in
figure 1 to determine the valve mode.
B.
Clean piping and valve of ail foreign material
such as welding chips, scale, oil, grease or dirt.
Gasket surfaces should be thoroughly cleaned to
insure leak proof connections.
C.
To allow for in-line inspection, maintenance or
removal of the valve without service interruption,
provide a manually operated stop valve on each
side of the Camflex® II valve with a manually
operated throttling valve mounted in the by-pass
line.
Note: If a flanged Camflex® II is being installed
and the distance between flanges is established
by ANSI or DIN, spool pieces (spacers) are
inserted between the line flange and the valve
body flange. Gaskets and valve bolting are then
installed and torqued using standard flange and
line bolting criteria.
D.
For flangeless valves, refer to figure 23 and
determine the correct size and quantity of bolts
to be used for the valve and flange rating.
E.
If the valve is to be installed in a horizontal
position, install the lower flange bolting to
provide a cradle, which will help support, the
valve while installing the remaining bolts.
F.
Place the valve in the line.
G.
Select and install correct gaskets.
Note: Spiral wound gaskets, suitable for service
conditions are recommended.
H.
Insert remaining flange bolting insuring that the
bolts align with the special bosses on the body,
which assure the valve is centered in the line and
also prevent rotation.
Note: For certain flange standards, through
bolting is not possible because of the valve body
neck or bonnet. To accommodate flange bolting,
guide arms with threaded holes or slots are
provided on the valve body to receive flange
bolts (refer to figure 22).
I.
Tighten flange bolts evenly and firmly.
Note: If the valve is equipped with manual
handwheel, it may now be placed in service.
Air is supplied to the actuator through the 1/4" NPT
tapped connection in the diaphragm case. Refer to
figure 14 to determine the correct supply pressure
and tubing size, then connect air supply piping.
Note: When the valve is equipped with regulators or
other accessories supplied by Masoneilan, only
connections to those accessories are required since
the piping to the actuator is connected at the factory.
Some valves equipped with electrical accessories
will require appropriate wiring. Refer to
manufacturer's instructions for correct wiring
information.
With the valve properly installed in the line and all air
or electrical service connected, it is recommended
Caution: Any change in flow direction or
actuator mode must be accomplished as
outlined. In this instruction otherwise
equipment malfunction could result.
4. Unpacking
5. Installation
Cantion: If the valve is to be insulated, do not
insulate the valve body neck.
Caution: Do not exceed maximum air
pressure indicated. Personal injury and
equipment malfunction could result.
6. Air Supply Piping
7. Placing in Service