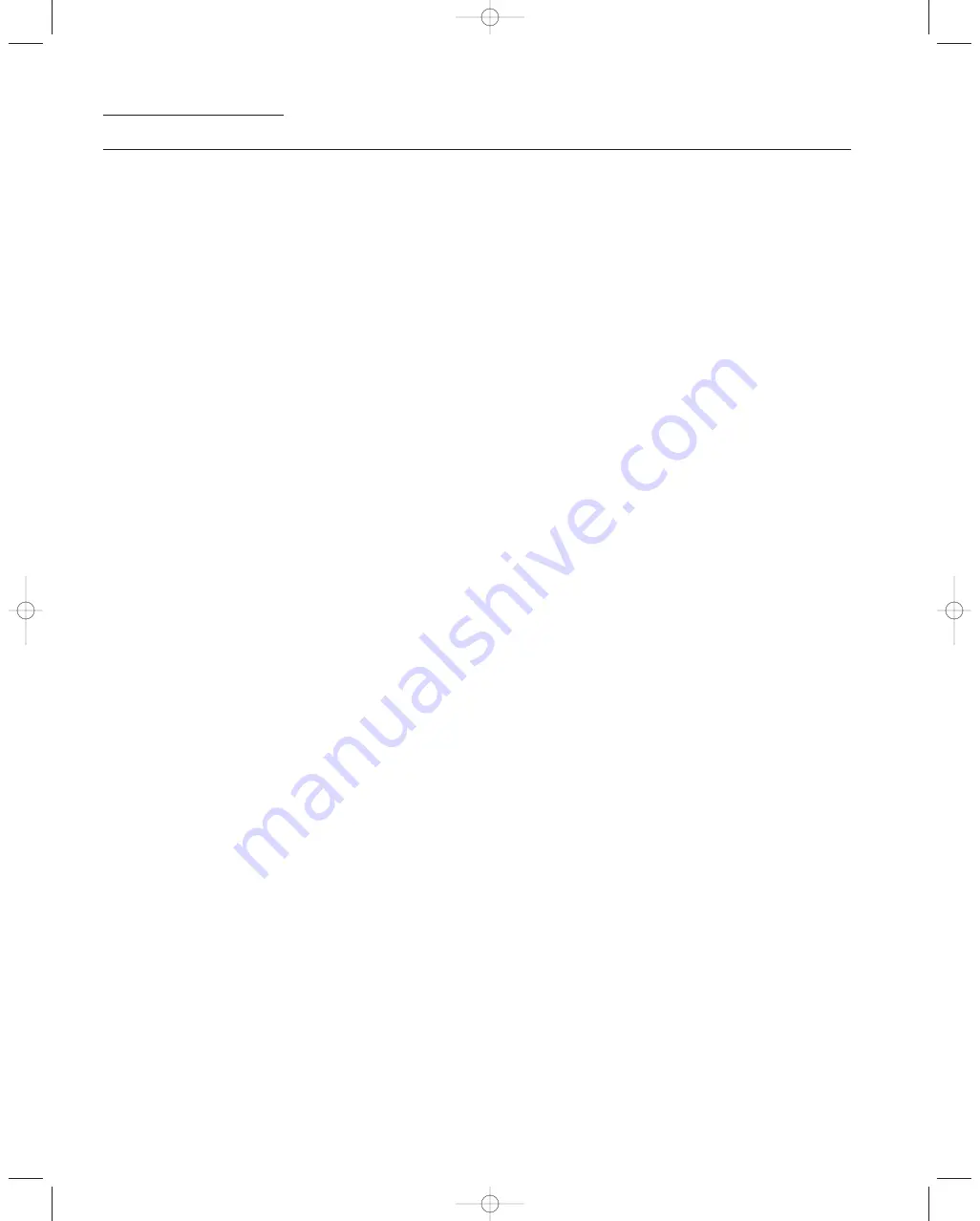
6
WILDEN PUMP & ENGINEERING, LLC
SECTION 7A
INSTALLATION
The Model T2 Metal pump has a 25 mm (1") inlet and 19.1 mm
(
3
⁄
4
") outlet and is designed for flows to 95 lpm (25.0 gpm). The
T2 Metal pump is manufactured with wetted parts of Hastelloy
®
or Stainless Steel. The center section of the T2 Metal pump is
of aluminum or polypropylene construction. The air distribution
system consists of a brass air valve body, aluminum air valve
piston, Glyd™ rings and a bronze center section bushing. A
variety of diaphragms, valve balls, valve seats, and o-rings are
available to satisfy temperature, chemical compatibility, abra-
sion and flex concerns.
The suction pipe size should be at least 25 mm (1") diameter or
larger if highly viscous material is being pumped. The suction
hose must be non-collapsible, reinforced type as the T2 is capa-
ble of pulling a high vacuum. Discharge piping should be at least
19 mm (
3
⁄
4
"); larger diameter can be used to reduce friction losses.
It is critical that all fittings and connections are airtight or a
reduction or loss of pump suction capability will result.
INSTALLATION: Months of careful planning, study, and selec-
tion efforts can result in unsatisfactory pump performance if
installation details are left to chance.
Premature failure and long term dissatisfaction can be avoided if
reasonable care is exercised throughout the installation process.
LOCATION: Noise, safety, and other logistical factors usually
dictate that “utility” equipment be situated away from the
production floor. Multiple installations with conflicting require-
ments can result in congestion of utility areas, leaving few
choices for siting of additional pumps.
Within the framework of these and other existing conditions,
every pump should be located in such a way that key factors are
balanced against each other to maximum advantage.
ACCESS: First of all, the location should be accessible. If it’s
easy to reach the pump, maintenance personnel will have an
easier time carrying out routine inspections and adjustments.
Should major repairs become necessary, ease of access can
play a key role in speeding the repair process and reducing
total downtime.
AIR SUPPLY: Every pump location should have an air line large
enough to supply the volume of air necessary to achieve the
desired pumping rate (see pump performance chart). Use air
pressure up to a maximum of 8.6 bar (125 psig) depending
upon pumping requirements. The use of an air filter before the
pump will ensure that the majority of any pipeline contaminants
will be eliminated. For best results, the pumps should use an air
filter, regulator, and lubricator system.
ELEVATION: Selecting a site that is well within the pump’s
suction lift capability will assure that loss-of-prime troubles will
be eliminated. In addition, pump efficiency can be adversely
affected if proper attention is not given to elevation (see pump
performance chart).
PIPING: Final determination of the pump site should not be
made until the piping problems of each possible location have
been evaluated. The impact of current and future installations
should be considered ahead of time to make sure that inadver-
tent restrictions are not created for any remaining sites.
The best choice possible will be a site involving the shortest
and the straightest hook-up of suction and discharge piping.
Unnecessary elbows, bends, and fittings should be avoided.
Pipe sizes should be selected so as to keep friction losses
within practical limits. All piping should be supported indepen-
dently of the pump. In addition, it should line up without plac-
ing stress on the pump fittings.
Expansion joints can be installed to aid in absorbing the forces
created by the natural reciprocating action of the pump. If the
pump is to be bolted down to a solid foundation, a mounting
pad placed between the pump and foundation will assist in
minimizing pump vibration. Flexible connections between the
pump and rigid piping will also assist in minimizing pump vibra-
tion. If quick-closing valves are installed at any point in the
discharge system, or if pulsation within a system becomes a
problem, a surge suppressor should be installed to protect the
pump, piping and gauges from surges and water hammer.
When pumps are installed in applications involving flooded suction
or suction head pressures, a gate valve should be installed in the
suction line to permit closing of the line for pump service.
The T2 can be used in submersible applications only when both
wetted and non-wetted portions are compatible with the mate-
rial being pumped. If the pump is to be used in a submersible
application, a hose should be attached to the pump’s air
exhaust and the exhaust air piped above the liquid level.
If the pump is to be used in a self-priming application, be sure
that all connections are airtight and that the suction lift is within
the pump’s ability. Note: Materials of construction and elas-
tomer material have an effect on suction lift parameters. Please
refer to pump performance data.
Pumps in service with a positive suction head are most efficient
when inlet pressure is limited to .5–.7 bar (7–10 psig).
Premature diaphragm failure may occur if positive suction is
.8 bar (11 psig) and higher.
THE MODEL T2 WILL PASS 3 mm (
1
⁄
8
") SOLIDS. WHENEVER
THE POSSIBILITY EXISTS THAT LARGER SOLID OBJECTS
MAY BE SUCKED INTO THE PUMP, A STRAINER SHOULD BE
USED ON THE SUCTION LINE.
CAUTION: DO NOT EXCEED 8.6 BAR (125 PSIG) AIR
SUPPLY PRESSURE. (3.4 BAR [50 PSIG] FOR UL MODELS.)
BLOW OUT AIR LINE FOR 10 TO 20 SECONDS BEFORE
ATTACHING TO PUMP TO MAKE SURE ALL PIPE LINE
DEBRIS IS CLEAR. ALWAYS USE AN IN-LINE AIR FILTER.
WIL_14070_E_01.qxd 1/4/06 6:29 AM Page 6
Содержание WILDEN BioPharm T2 Series
Страница 1: ...WIL_14070_E EOM T2M BIOPHARM 2 05 WIL_14070_E_01 qxd 1 4 06 6 29 AM Page C1...
Страница 15: ...13 WILDEN PUMP ENGINEERING LLC NOTES WIL_14070_E_01 qxd 1 4 06 6 29 AM Page 13...
Страница 19: ...WIL_14070_E_01 qxd 1 4 06 6 29 AM Page BC1...
Страница 20: ...WIL_14070_E_01 qxd 1 4 06 6 29 AM Page BC2...