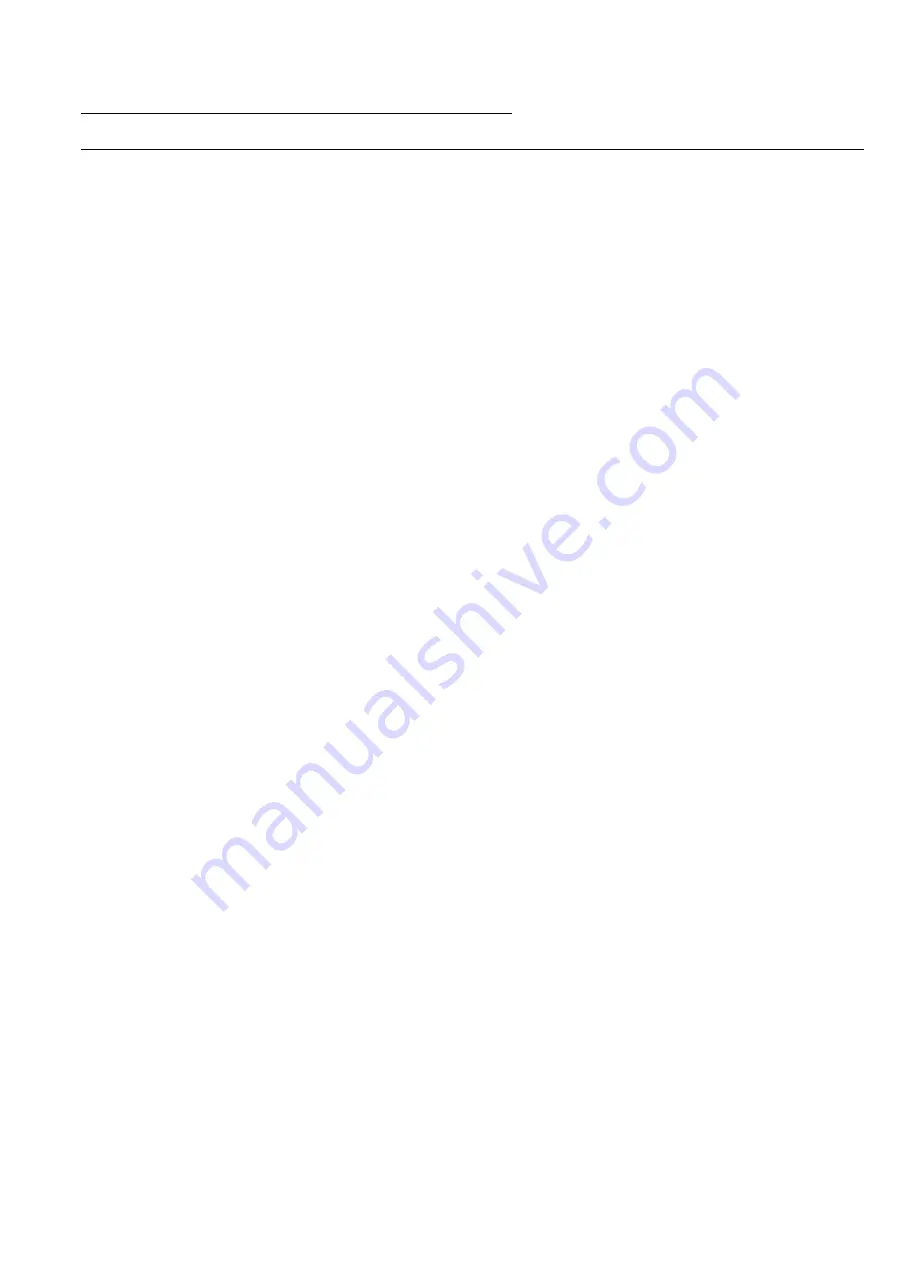
WIL-10040-E-02
11
WILDEN PUMP & ENGINEERING, LLC
SECTION 7D – ACCU-FLO™
TROUBLESHOOTING
Pump will not run.
1.
Check for pressurized air at the inlet.
2.
Check air inlet and filter for debris.
3.
Connect a test lamp to the two wires which run to pump
and ensure that the lamp cycles on and off.
4.
Make sure that the air valve manual override (small red
knob on front of valve) is switched to the “0” position.
5.
Check pilot pressure vent at the top of the operator/coil
assembly to ensure that it is not clogged.
6.
Check for a worn out air valve. If air continually blows out
the exhaust in very large quantities, the air valve seals may be
worn beyond their ability to function. In this case, the valve
must be replaced.
NOTE: Before the valve is scrapped, it is possible that it may
be saved by completely disassembling the valve, cleaning all
components and relubricating the valve.
Pump runs but little or no fluid comes out.
1.
Check that the discharge isolation valve is not closed.
2.
Check that the electronic signal is slow enough that the
pump is able to complete each physical stroke before it is
signaled to change direction. The time required to complete the
stroke is determined by a variety of factors which include fluid
viscosity and head pressure.
3.
Check for pump cavitation; slow pump speed down to
match the thickness of the material being pumped.
4.
Check for sticking ball check valves. If the material being
pumped is not compatible with the pump elastomers, swelling
may occur. Replace ball check valves and O-ring with the
proper elastomers.
5.
Check to make sure that all suction connections are air
tight, and that the clamp bands are properly tightened.
Pump air passages blocked with ice.
Check for excessive moisture in compressed air line. As the air
expands out the exhaust during the operation of the pump,
water vapor entrapped in the compressed air can freeze and
block the air passageways in the pump. If this occurs, it may
be necessary to install a coalescing filter, an air dryer, or a hot
air generator for the compressed air.
Air bubbles in pump discharge.
1.
Check for ruptured diaphragm.
2.
Check tightness of clamp bands, and the integrity of the
O-rings, especially at intake manifold.
Product comes out of the air exhaust.
1.
Check for diaphragm rupture.
2.
Check tightness of piston plates to shaft.
Pump rattles.
1.
Create false discharge head or suction lift.
Solenoid buzzes or solenoid burnout.
1.
Incorrect voltage, faulty or dirty solenoid.
Solenoid valve fails to shift electrically but shifts with
manual override.
1.
Incorrect voltage, defective coil or wiring.
Solenoid valve fails to shift electrically or with manual over-
ride.
1.
Inadequate air supply, contamination, inadequate or
improper lubrication, mechanical binding in the valve.
Valve shifts but fails to return.
1.
Broken spring, mechanical binding.
Excessive leaking from air valve vent.
1.
Worn seals in air valve.
Содержание WILDEN A1 Series
Страница 1: ...7 REPLACES 7 WIL 10040 E...
Страница 19: ...MAINTENANCE RECORD DATE SERVICE RENDERED SERVICED BY...
Страница 26: ...NOTES...
Страница 27: ......