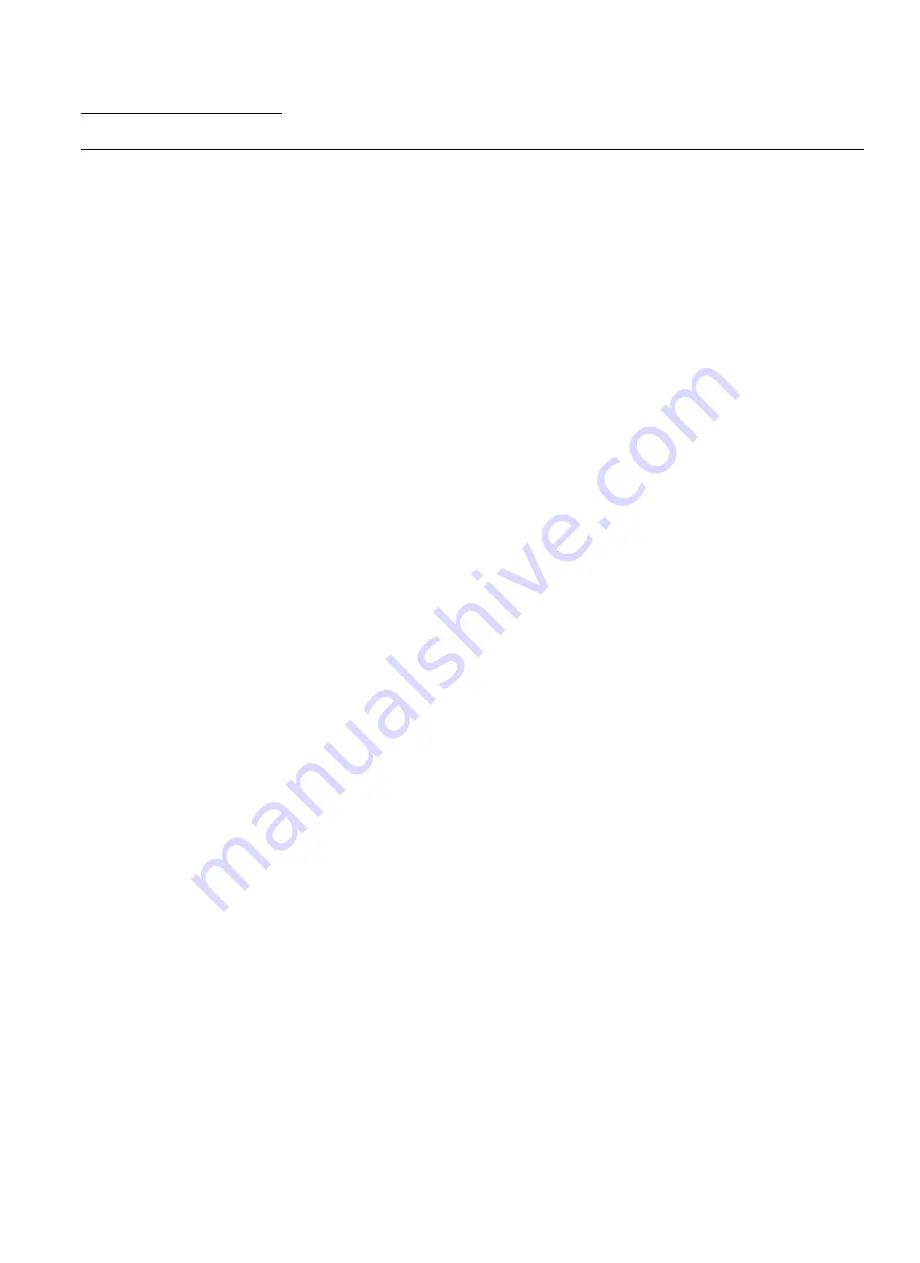
WIL-10040-E-02
9
WILDEN PUMP & ENGINEERING, LLC
SECTION 7A
INSTALLATION
All Wilden pumps are manufactured with a variety of materials
for the air distribution system, liquid path and elastomers. This
variety is offered to satisfy the temperature, chemical compat-
ibility, abrasion and flex life requirements for most applications.
Consult manual for available materials and temperature limita-
tions for this pump model.
For Accu-Flo models only, all wiring used to operate the pump
should be placed and connected according to all applicable
electrical codes. It is important that the wiring be of adequate
gauge to carry the current required to operate the pump. In
addition, it is necessary that the electrical power supply be
large enough to supply the current required to operate the
pump. Wiring should be above ground level if possible (in case
of fluid spill or leakage), and all wiring and connections which
could become wet or damp should be made watertight.
The suction pipe used for installation should be sized equal to,
or greater than, the pump liquid inlet connection. This will mini-
mize pump cavitation and potential blockages of the pump
inlet. The discharge piping should also be sized equal to, or
greater than, the pump liquid discharge connection. If the
pump is to be used in a self-priming application, be sure that
all connections are airtight and that the suction lift is within the
pump’s ability. (Consult manual for suction lift information.)
Note: Materials of construction and elastomer materials have
an effect on suction lift parameters.
INSTALLATION: Months of careful planning, study and selec-
tion efforts can result in unsatisfactory pump performance if
installation details are left to chance.
Premature failure and long term dissatisfaction can be avoided if
reasonable care is exercised throughout the installation process.
LOCATION: Noise, safety, and other logistical factors usually
dictate that "utility" equipment be situated away from the
production floor. Multiple installations with conflicting require-
ments can result in congested utility areas, leaving few choices
for siting additional pumps.
Within the framework of these and other existing conditions,
every pump should be located in such a way that four key factors
are balanced against each other to maximum advantage.
1. ACCESS: First of all, the location should be accessible. If it is
easy to reach the pump, maintenance personnel will have an easier
time carrying out routine inspections and adjustments. Should
major repairs become necessary, ease of access can play a key
role in speeding the repair process and reducing total downtime.
2. AIR SUPPLY: Every pump location should have an air line large
enough to supply the volume of air necessary to achieve the
desired pumping rate. (Consult manual for performance informa-
tion.) The use of an air filter before the pump will ensure that the
majority of pipeline contaminants will be eliminated. For best
results, the pump should use an air filter, regulator system.
Sound levels are reduced below OSHA specifications using the
standard Wilden muffler.
3. ELEVATION: Selecting a site that is well within the pump’s
dynamic lift capability will assure that a loss-of-prime condition
will be avoided. In addition, pump efficiency can be adversely
effected if proper attention is not given to site location.
4. PIPING: Final determination of the pump site should not be
made until the piping problems of each possible location have
been evaluated. The impact of current and future installations
should be considered ahead of time to make sure that inadver-
tent restrictions are not created for any remaining sites.
The best choice possible will be a site involving the shortest and
straightest hook-up of suction and discharge piping. Unneces-
sary elbows, bends, and fittings should be avoided. Pipe sizes
should be selected so as to keep friction losses within practical
limits. All piping should be supported independently of the
pump to avoid damage. In addition, the piping should be aligned
so as to avoid placing stress on the pump fittings.
Flexible hose can be installed to aid absorbing the forces
created by the natural reciprocating action of the pump. If the
pump is to be bolted down to a solid location, a mounting pad
placed between the pump and the foundation will assist in
minimizing pump vibration. Flexible connections between the
pump and rigid piping will also assist in minimizing pump vibra-
tion. If quick-closing valves are installed at any point in the
discharge system, or if pulsation within a system becomes a
problem, a Wilden Equalizer surge dampener should be
installed to protect the pump, piping and gauges from surges
and water hammer. Installation of a tee at the discharge of the
pump will allow the addition of an Equalizer to the system at a
later date without requiring piping modifications. Installation of
inlet and discharge isolation valves are also recommended to
make service and repair easier.
Pumps in service with a positive suction head are most efficient
when pressure is limited to .4-.7 Bar (7-10 psig). Premature
diaphragm failure may occur if positive suction exceeds these
recommended pressures.
A STRAINER SHOULD BE USED ON THE SUCTION LINE OF
THE SYSTEM IF THERE IS A POSSIBILITY THAT SOLIDS
ENTERING THE PUMP MAY EXCEED THE PUMP’S SOLIDS
HANDLING CAPABILITIES.
PLEASE READ AND FOLLOW ALL CAUTIONS NOTED IN
THIS MANUAL.
Pump should be thoroughly flushed before installing into
process line.
Blow out air line for 10 to 20 seconds before attaching
pump to clear all pipe line debris.
Содержание WILDEN A1 Series
Страница 1: ...7 REPLACES 7 WIL 10040 E...
Страница 19: ...MAINTENANCE RECORD DATE SERVICE RENDERED SERVICED BY...
Страница 26: ...NOTES...
Страница 27: ......