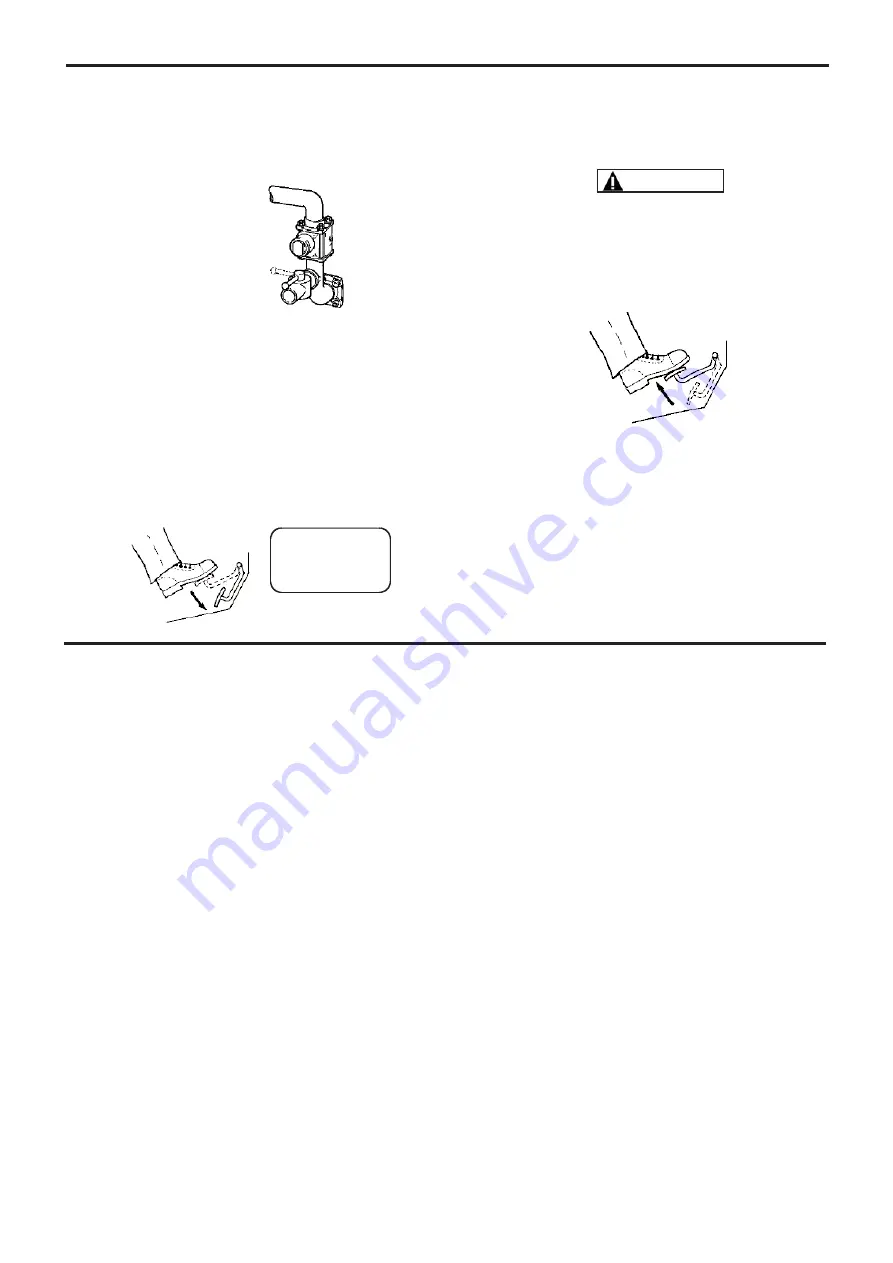
11/21
NT 1401-F00 12.05 Cold front outlet Intercooler TYPHON e
STEP 3
Close all valves and proceed to pressurize the tank and
discharge the cargo.
3.5 SHUTTING DOWN PROCEDURE - Vehicle
Mounted
STEP 1
Depress the clutch and disengage the PTO.
STEP 2
Reduce engine speed to idle.
ALWAYS DISENGAGE THE DRIVE BEFORE SLOWING ENGINE
DOWN.
STEP 3
Release the clutch.
NOTICE :
DO NOT attempt to restart the compressor in the follow-
ing instances :
a. If there is still pressure or vacuum in the system. In
this instance, open the vent valve first, than restart the
compressor. Once the pump is up to speed, close the
vent valve slowly.
b. If the compressor input speed is too slow.
CAUTION
PTO
OFF
NOTICE :
THE COMPRESSOR MUST OPERATE AT FIXED SPEED WITHIN
THECOMPRESSOR MODEL SPEEDLIMITS. SPEED MUST
REMAINCONSTANT THROUGHOUT THE OFF LOADING OPE-
RATION.
« FERME »
CLOSE
33.. P
PA
AC
CK
KA
AG
GE
E O
OP
PE
ER
RA
AT
TIIO
ON
N ((ccoonnttiinnuueedd))
44.. M
MA
AIIN
NT
TE
EN
NA
AN
NC
CE
E
4.1 Maintenance schedules
After each water cleaning of the truck or compressor
Always run the compressor for 15 minutes to remove
any water that inadvertently gets into the piping.
DO NOT fog or introduce anti-corrosive liquids into the
compressor to prevent corrosion. Use of liquids in the
compressor will cause failure.
After the first 50 hours of operation
Change compressor oil.
After 300 hours and at least every year
Change compressor oil.
Weekly
1.
The compressor should be run once a week for at
least 15 minutes to prevent moisture from collecting
inside. This will reduce the risk of corrosion damage to
the compressor and other equipment in the piping.
2.
Inspect and clean air filter. Clean the compressor
external surfaces and cooling fins. Inspect DAILY if
operating in dirty or severe environment. Check the
condition of the inlet filter hose for splits and tears.
Replace or repair as necessary.
3.
Inspect compressor, system piping and components.
Clean or repair as necessary.
4.
Check power transmission line (pulley, shaft, torque
limitor...).
Per manufacturer’s recommendations
Lubricate the universal seal.
Monthly
1.
Check the relief valve(s) for wear and proper settings.
Replace or adjust as necessary.
2.
Check that the check valve works properly, replace as
necessary.
4.2 Compressor oil draining procedure
Compressor maintenance is limited to a periodic oil
change.
For oils recommended, see § 3.1.
Unscrew and remove the oil filter with its seal. Drip-drain
all the oil contained in the casing.
Carefully clean the oil filter with solvent. Blow out all
impurities with a compressed air blast.
After checking that no particles remain in the filter, reins-
tall it making sure that the seal is in good condition.
Fill the compressor. See § 3.2.