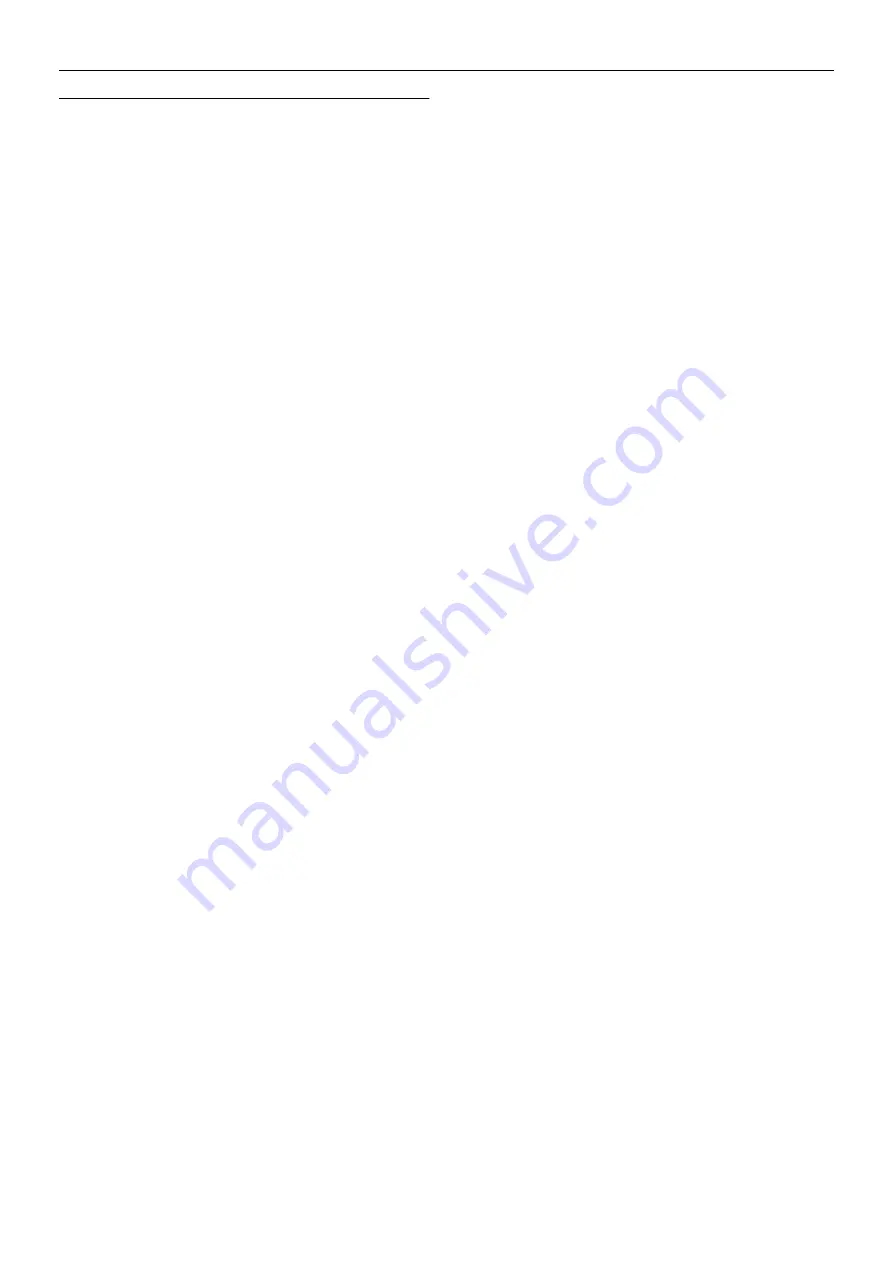
OPERATING INSTRUCTIONS
23
7/20, P65
DECOMMISSIONING
When the machine is to be permanently decommissioned or
dismantled, it is important to ensure that all hazard risks are either
eliminated or notified to the recipient of the machine. In particular:-
•
Do not destroy batteries or components containing asbestos
without containing the materials safely.
•
Do not dispose of any pressure vessel that is not clearly marked
with its relevant data plate information or rendered unusable by
drilling, cutting etc.
•
Do not allow lubricants or coolants to be released into land surfaces
or drains.
•
Do not dispose of a complete machine without documentation
relating to instructions for its use.
Содержание 7/20
Страница 9: ...DECALS 7 7 20 P65 Engine oil drain Cold Start Procedure...
Страница 18: ...16 GENERAL INFORMATION 7 20 P65 VARIABLE HEIGHT RUNNING GEAR FIXED HEIGHT RUNNING GEAR...
Страница 50: ......
Страница 51: ......
Страница 52: ......