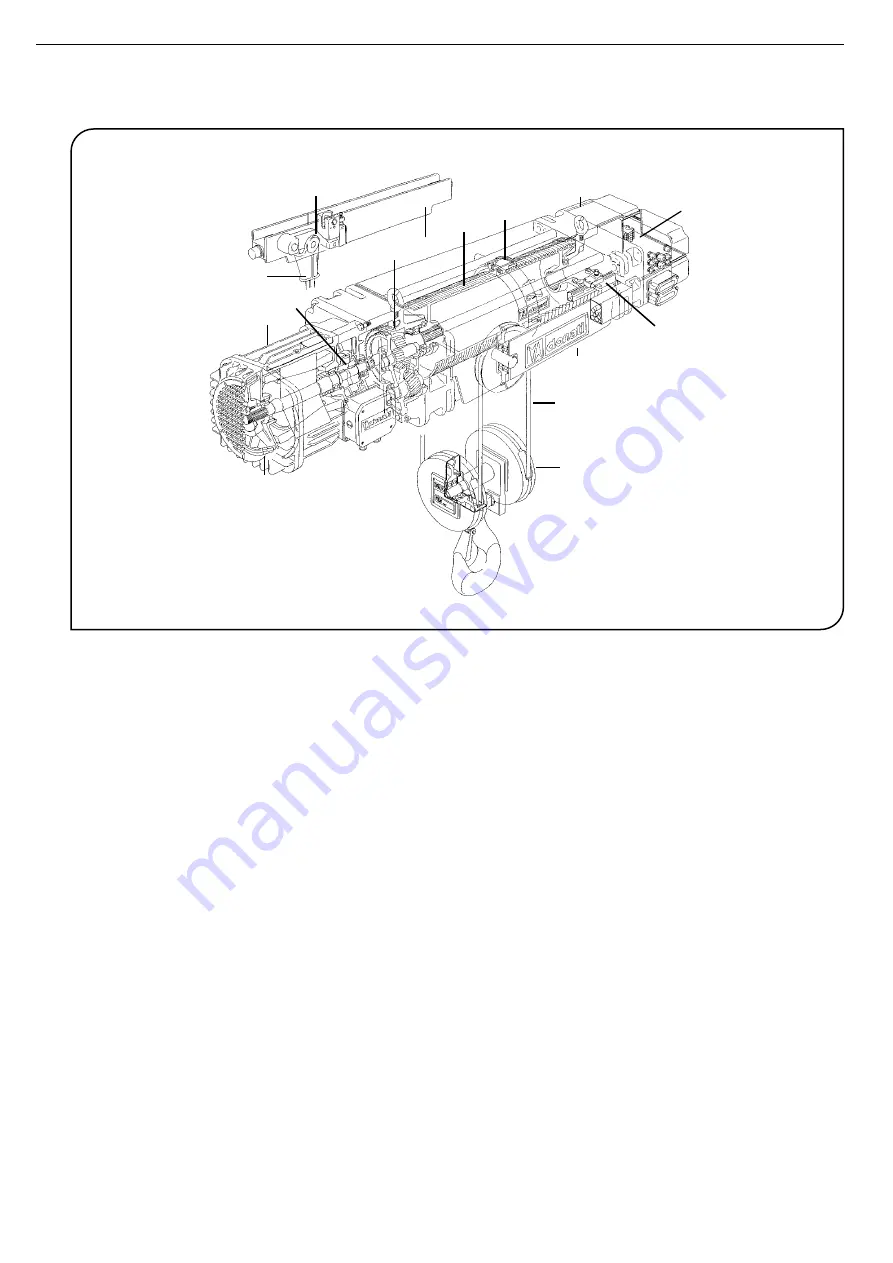
MAN16MG0
5
instructions
for
use
series
drh
1/2/3/4 -
dst
/
n
/
s
-
dst
/
r
-
drt
8
1 - Electrical lifting motor
• Three-phase asynchronous motor, self-braking conical rotor. Minimum protection IP55 - Insulation class F.
It is fitted with a series of thermal probes to protect against overloads.
Three-phase asynchronous motor DRH4 24kW cylindrical.
2 - Lifting brake
• The conical brake is fitted with an asbestos-free friction gasket. The brake block, made up of a fan which ensures
the cooling of the brake itself and of the motor, moves on its axis with the motor shaft, and the braking function
is activated automatically in case of power failure.
[RES. 1.2.6 - 4.1.2.6 c) - Attachment I Machine Directive]
Electro-magnetic brake DRH4 24kW.
3 - Joint
• It connects the self-braking motor and the reducer, allowing perfect axial running of the motor shaft.
4 - Gearbox
• Coaxial, with 3 reduction stages, produced with cylindrical high-resistance steel gears, which are helical-toothed
and heat treated. Designed to resist fatigue and wear and tear for life relating to the FEM service group [RES.
4.1.2.3 - Attachment I Machine Directive].
It is entirely installed on ball bearings lubricated for life in an oil bath.
5 - drum shell
• The drum, made of steel tube and mechanically channelled, is supported by the reducer flange and the
flange on the equipment side, with hubs with swivel broached holes on permanently lubricated bearings.
The drum is designed following the standards ISO 4308-1/86 and UNI 9466 and also the FEM rules
9.661/86. The support flanges of the drum are fitted with cylindrical steel pins to fix the suspension and
settingdown components of the hoist. Mechanically-made housings support the terminal head crossbar
and the transmission pulley. The connection between the two flanges is made with bolted staybolts.
2.1.3 DRH wire rope hoist parts (fig. 5)
fig. 5
1
2
3
4
5
14
15
7
8
9
10
11
12
13
6
9
instructions
for
use
series
drh
1/2/3/4 -
dst
/
n
/
s
-
dst
/
r
-
drt
MAN16MG0
5
6 - rope guide
•
Formed by a threaded ring made of spheroidal graphite cast iron, the rope guide allows an optimal winding of
the wire rope on the drum [RES. 4.1.2.4 - Attachment I Machine Directive]. An elastic system allows the
automatic registration of clearance and wear and tear.
The rope guide has sliding-block reaction arms made of brass which, acting on the stay bolts of the rope drum
cover, act as actuators of the ascent and descent limit switches.
7 - Lifting limit switches
• A component with safety functions which limit, in case of emergency, the hook’s ascent and descent run [RES.
4.1.2.6 a) - Attachment I Machine Directive]. It is formed of two precision micro switches which function
according to the principle of “slow positive opening” and work on the auxiliary circuit of the control device of
the lifting motor.
8 - Pulley crossbar
• Used in the executions at 4 falls, it is supported by two pivots which allow it to position along the
vertical axis of the wire rope. It is fitted with a transmission pulley made of carbon steel with a mechanically
channelled rope race and swivelling on ball bearings with permanent lubrication.
9 - Terminal head crossbar
• Used in the executions at 2 and 4 falls, it is supported by two pivots which allow it to move on the vertical
axis of the wire rope. The overload device is located between the cross head plates.
8a/9a - Pulleys and terminal head support
• Used in the executions of 6 and 8 falls, consist of a welded structure and is designed with a junction plate to
be located on the double girder carriage. It is equipped with pulleys made of carbon steel mechanically groo-
ved and swivelling on bearings with permanent lubrification. The overload device is located on the support in
the anchorage crosshead.
10 - The overload device
• All DRH electric wire rope hoists are fitted with overload devices, with a micro switch for an intervention
threshold [RES. 4.2.1.4 – Attachment I Machine Directive]. The overload device constantly measures and checks
the weight of the load and the dynamic and inertial effects due to handling. If the set calibration readings are
exceeded, the micro switch on the device intervenes by opening the control circuit of the lifting control device.
11 - rope terminal head and wedge
• The fixed head is made of spheroidal graphite cast iron and the minimum coefficient of use conforms with the
FEM 9.661/86 regulation. A wedge fixes the wire rope to prevent unthreading.
12 - rope
• Made of flexible high-resistance steel with a minimum coefficient of use chosen to conform with standard ISO
4308-1/86. On the 2-fall hoists with long drums and extra long 1st size (X1) and the 2- and 4-fall hoists with
extra long drums 2nd size (X2) antirotating wire ropes are used.
13 - hook block and hook
• Fitted with transmission pulleys made of carbon steel with a mechanically channelled rope race and rotating on
permanently lubricated ball bearings. The load hook is made of high-resistance press-forged steel and is fitted
on an oscillating transverse. It rotates on step bearings and is fitted with a safety device to prevent unhooking.
[RES. 4.1.2.6 - Attachment I Machine Directive].
14 - Frame for electrical connections
• Available on request, fitted with a cable clamp, it allows the cabling of all the connections of the electrical
equipment of the hoist and related trolley. The containment space of the electrical connections and/or related
low voltage control equipment is fitted with a thermoplastic cover with IP55 degree of protection.
15 - Low voltage controls at 48 V - AC
• When the hoist is supplied with electrical controls, the ascent and descent and right and left functions of the
related trolley are activated with electrical equipment including:
• The transformer for the low voltage power supply of the control circuits
• The general line contactor and the contactors/inverters for the control of the motors
• The protection fuses of the motors and of the transformer
• The terminal block for the connections of the auxiliary and power circuits.
The components are fitted on a hinged panel and fixed in the space located on the opposite side of the motor.
The controls are activated by the pendant push-button panel powered in low voltage AC at 48V.
The push-button panel, of ergonomic shape, made of self-extinguishing shockproof thermoplastic, is water
resistant to IP65 protection. The emergency stop function [RES. 1.2.4.3 - Attachment I Machine Directive], is
produced with a mushroom-head push-button which using an intentional release action puts the control circuit
in the forward position [RES. 1.2.3 - Attachment I Machine Directive].
The push-button panel is connected to the electrical equipment by a multipolar electrical cable fitted with tear
proof metallic parts.
KMAN16MG05
Содержание DRH 1 Series
Страница 128: ...KMAN16MG05...
Страница 129: ......