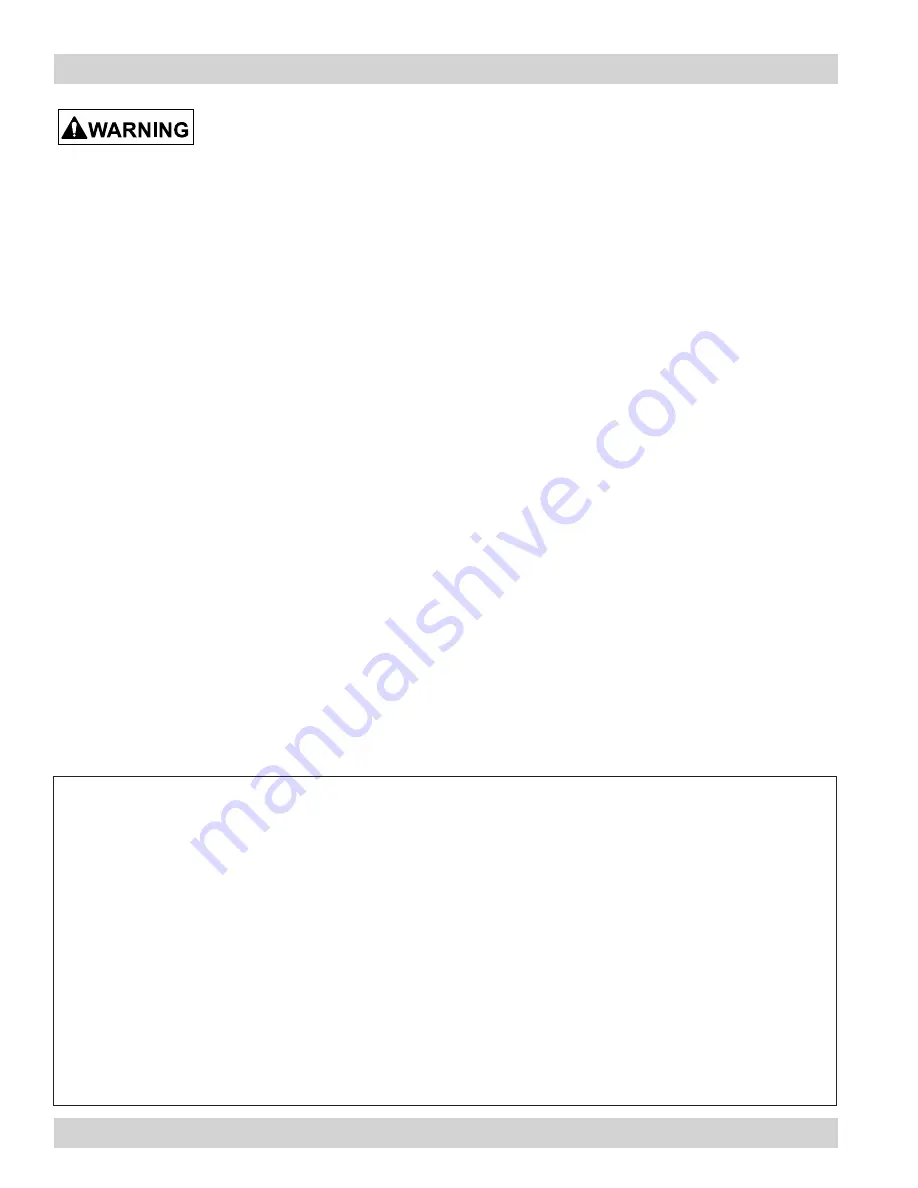
APPLICATION OF DUST CONTROL EQUIPMENT
Combustible materials such as buffing lint, paper, wood, metal dusts, weld fume, or flammable coolants or
solvents represent potential fire and/or explosion hazards. Use special care when selecting, installing, and
operating all dust, fume, or mist collection equipment when such combustible materials may be present in
order to protect workers and property from serious injury or damage due to a fire and/or explosion.
Consult and comply with all National and Local Codes related to fire and/or explosion properties of
combustible materials when determining the location and operation of all dust, fume, or mist collection
equipment.
When combustible materials are present you must consult with an expert in fire extinguishing and/or
explosion protection systems, who is also familiar with the local codes, for support and guidance on the
selection and installation of an appropriate fire and/or explosion protection system.
DO NOT allow sparks, cigarettes or other burning objects to enter the hood or duct of any dust, fume, or mist
collection equipment as these may initiate a fire or explosion of any combustible materials accumulated in
the collector.
Portions of dust, mist, and fume-collection equipment, including the clean- and dirty-air plenums may be
considered “OSHA Confined Spaces.” Refer to the appropriate OSHA regulations to determine if a specific
installation should be considered a confined space and if a permit program is required.
Recirculating filtered air in your facility can be a hazard. Consult with OSHA to ensure compliance with all
codes regarding recirculating filtered air.
Improper operation of a dust, fume, or mist control system may contribute to conditions in the work area or
facility that could result in severe personal injury and product or property damage. Check that all dust, fume,
or mist collection equipment is properly selected, installed, and operated for its intended use.
This manual contains specific precautionary statements relative to worker safety. Read this manual thoroughly and
comply as directed. Instruct all personnel on the safe use and maintenance procedures related to this equipment.
Discuss any questions on the application, use, or maintenance of this equipment with a Donaldson Torit representative.
For optimum collector performance, use only Donaldson Torit replacement parts.
Donaldson Company, Inc.
Model Number _____________________________ Serial Number ______________________________
Ship Date _________________________________ Installation Date _____________________________
Customer Name _______________________________________________________________________
Address _____________________________________________________________________________
____________________________________________________________________________________
Filter Type ____________________________________________________________________________
Accessories __________________________________________________________________________
Other ________________________________________________________________________________
Data Sheet
Содержание PowerCore CPV-1
Страница 29: ...Torit PowerCore CPV 1 to CPV 12 26 Service Notes Date Service Performed Notes...
Страница 30: ...27 Donaldson Company Inc Service Notes Date Service Performed Notes...
Страница 31: ......