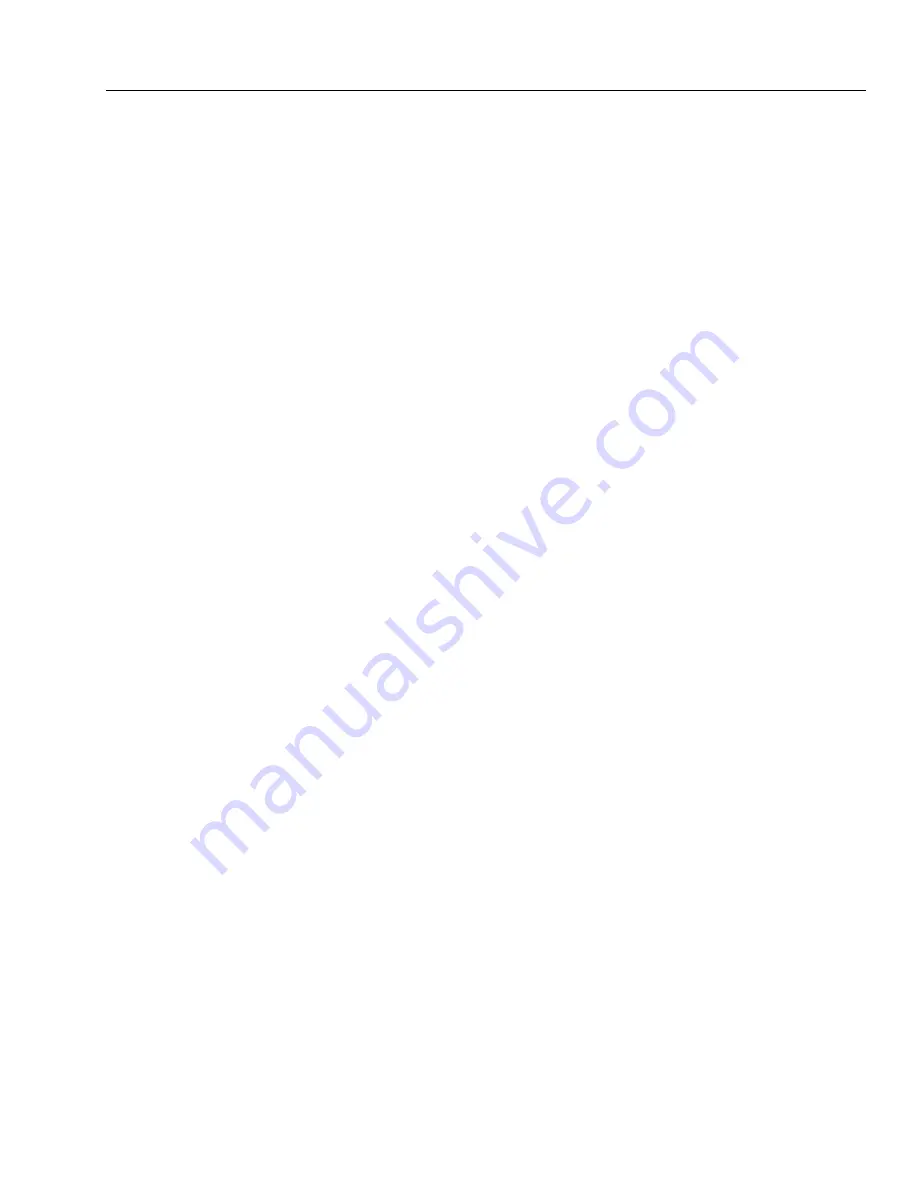
13
Appendix B: Hot Stamping Tips & Tricks
A. About Foil Printing
Rotary foil printing is accomplished by laminating a roll leaf material to the web. By running the two materials through a
station that has a heated, engraved impression die and a suitable base roll, and then stripping the roll leaf material from the
web; leaving the transferred image on the substrate and rewinding the waste foil.
In the DMS Foil Printing System, the die is a CNC and/or photo engraved hand-finished brass roll. The die is mounted on a
custom-engineered shaft/heater assembly.
The base roll assembly uses a hard (90-100 durometer) base roll mounted on an eccentric shaft within the intended die station
and a pneumatic rotary actuator outside the station, connected to the shaft. The base roll is rotated up into print position only
when the press and the HP-3002 control unit are in “RUN” mode.
The system control unit, using a microprocessor based temperature control module and solid state relay, controls the
temperature and base roll actions.
Signals are received by the control unit from an infrared thermocouple mounted on the die assist and from the “RUN” circuit
of the press run relay through a “slave line”.
B. About Roll Leaf (foil)
The foil used in hot stamping today is usually an extruded film carrier with several layers coated on one side. These layers
consist of a release agent, a pigment (or pattern of pigments), and an adhesive agent (often referred to as “sizing”). The
formulation of these layers varies depending on the application.
During the foil printing process, heat from the die travels through the foil layers, activating the release agent and sizing
simultaneously, which causes the transfer of material from carrier to substrate. The performance of these two layers together
give the foil it’s specific traits, such as how long the foil needs to be left on the web before it is stripped and where the
stripping idler is placed.
The three factors that affect foil transfer the most are: heat, dwell, and pressure.
Below a certain heat threshold, the reactions necessary for proper release will not occur consistently, and poor print quality
will result.
Dwell is the amount of time the transfer has to occur between the die and base roll. The greater the web speed, the less time
(dwell) the transfer has to take place. Increasing die temperature will compensate for reduced dwell, to a point, but there are
physical limits to how fast heat can travel from the surface of the die through the foil. Foils that will accept a short dwell are
considered “loose”, while foils that require a long dwell (or high heat) are considered “tight”.
A certain amount of pressure is needed to aid the release action of the foil, but generally not enough to deform the substrate
substantially. Image size and configuration will affect pressure requirements almost as much as foil sizing and release
properties.
Содержание FR Series
Страница 11: ...11 APPENDIX A Illustrated Parts List ...
Страница 12: ...12 APPENDIX B Hot Stamping Tips Tricks ...