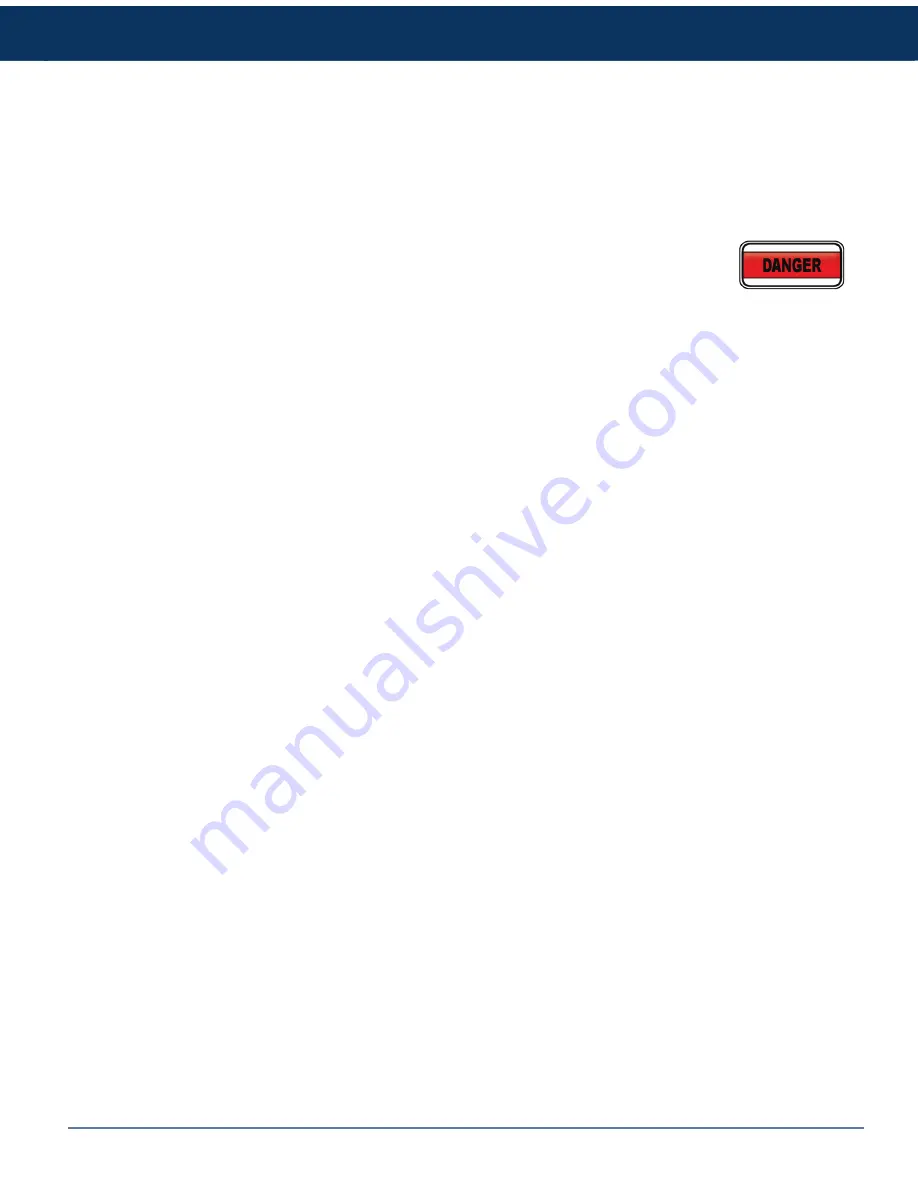
PUMP
3
Instruction & Operation Manual
800.789.1718
Care of Stainless Steel
The stainless steel components in Dixon Sanitary equipment are machined, welded and assembled by skilled craftsmen using
manufacturing methods that preserve the corrosion-resistant quality of the stainless steel.
Retention of corrosion-resistant qualities under processing conditions requires regular attention to the precautions listed below.
1.
Regularly check all electrical devices connected to the equipment for stray currents caused by improper
grounding, damaged insulation or other defects. Corrosion: Pitting often occurs when stray currents
come in contact with moist stainless steel.
2.
Never leave rubber mats, fittings, wrenches, etc. in contact with stainless steel. Corrosion: Pitting or galvanic action. Objects
retard complete drying, preventing air from reforming the protective oxide film. Galvanic corrosion occurs when two dissimilar
metals touch when wet.
3.
Immediately rinse equipment after use with warm water until the rinse water is clear. Clean the equipment (manual or CIP)
as soon as possible after rinsing. Corrosion: discoloration, deposits, pitting. Product deposits often cause pitting beneath the
particles.
4.
Use only recommended cleaning compounds. Purchase chemicals from reputable and responsible chemical manufacturers
familiar with stainless steel processing equipment, they continuously check the effects of their products on stainless steel.
5.
Use cleaning chemicals exactly as specified by the manufacturer. Do not use excessive concentrations, temperatures or
exposure times. Corrosion: Pitting, discoloration, stress cracks. Permanent damage often occurs from excessive chemical
concentrations, temperatures or exposure times.
6.
For manual cleaning, use only soft non-metallic brushes, sponges or pads. Brush with the grain on polished surfaces, avoid
scratching the surface. Corrosion: Pitting, scratches. Metal brushes or sponges will scratch the surface and promote corrosion
over a period of time. Metal particles allowed to remain on a stainless steel surface will cause pitting.
7.
Use chemical bactericides exactly as prescribed by the chemical manufacturer in concurrence with local health authority. Use
the lowest permissible concentration, temperature and exposure time possible. Flush immediately after bacterial treatment.
In no case should the solution be in contact with stainless steel more then 20 minutes. Corrosion: Protective film destroyed.
Chlorine and other halogen bactericides can destroy the protective film. A few degrees increase in temperature greatly
increases chemical activity and accelerates corrosion.
8.
Regularly inspect the joints in pipelines. Be sure all connections are tight fitting without binding. Corrosion: Crevice corrosion.
Small crevices caused by improperly seated gaskets will promote crevice corrosion. Stainless steel under stress will develop
stress cracking especially in the presence of bactericides containing chlorine.
9.
Regularly inspect equipment for surface corrosion (i.e. pitting deposits, stress cracks, etc.). If deposit or color corrosion is
detected, remove it immediately using mild scouring powder and detergents. Rinse thoroughly and allow to air dry. Review
production and cleaning procedures to determine the cause.
Note:
If corrosion is not removed, the protective film cannot be
restored and corrosion will continue at an accelerated rate.