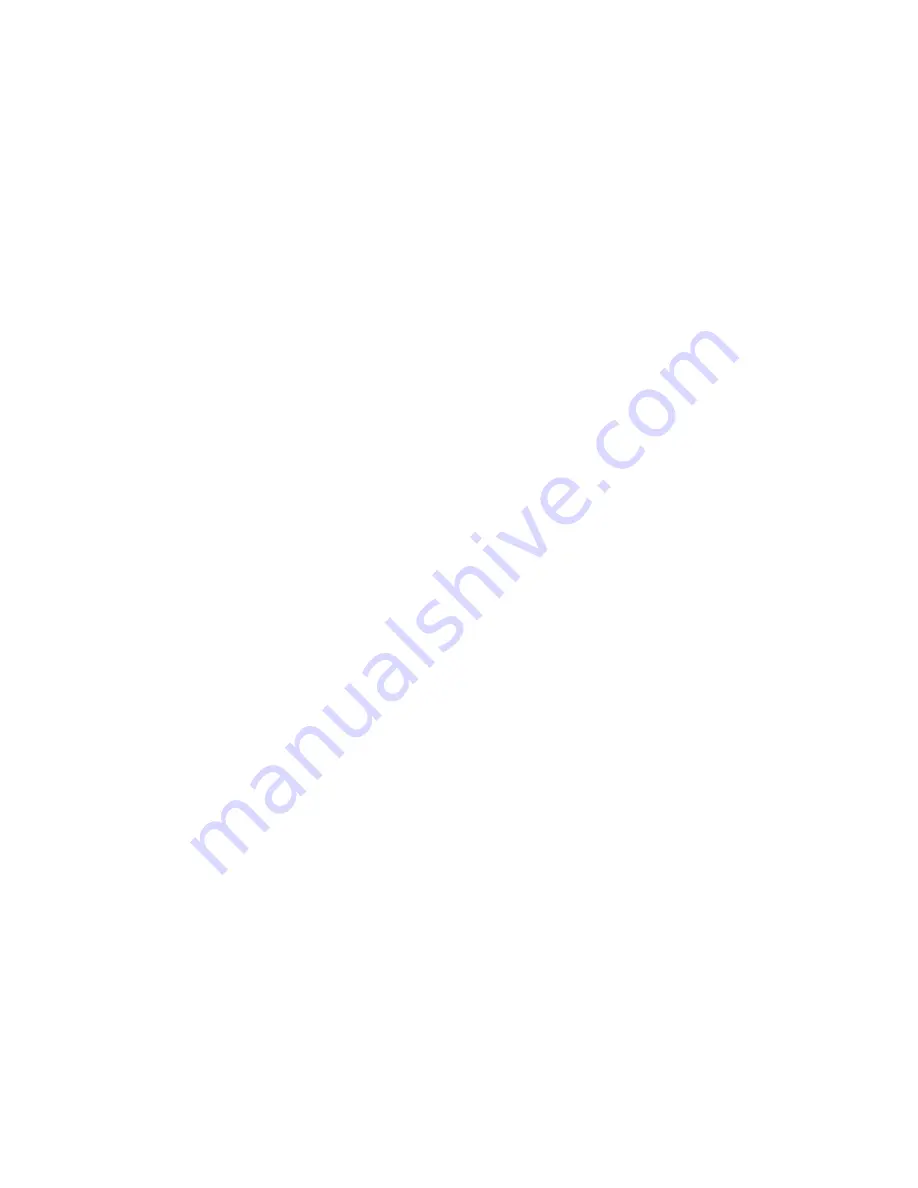
5
cartridge filters and cause excessive differential pressure across the filters resulting in greatly
reduced air flow along with premature filter replacement.
Note:
The air line must be free of oil and water. Oil and/or water will destroy
cartridge filters.
A customer supplied regulator with a 160 PSI gage must be installed to monitor air pressure.
Prior to the final connection of the air line to the collector manifold, the air line should be
purged. This will remove debris that could damage the valves and block the nozzles in the blow
pipes.
Electrical / Controls
Note:
All of the electrical installation must be performed by a qualified electrician
and in accordance with the local codes.
The blower motor operates with 208-230/460 volt, 60 cycle, and 3 phase electrical power
unless specified otherwise with the equipment order. Electrical power is connected to the
Motor Starter Control Box Located on the front of the collector. Inside the Motor Starter is a
decal that confirms the voltage the motor was set up for at the factory. Should this need to be
changed to the other voltage listed above, the motor will have to be rewired in accordance to
the data label on the motor. Access the motor from the blower door of the collector.
The blower motor will need to be energized through a motor starter with over load protection.
The electrical components must be sized and selected in accordance to the national electric
code.
Nominal Full Load Amperes are as follows:
Voltage
Horse Power
208V
230V
460V
575V
3
10.0
8.0
4.0
3.5
5
15.00
13.0
6.5
5.0
7.5
20.0
18.0
9.0
7.0
10
30.0
24.0
12.0
10.0
15
40.0
37.0
18.5
15.0
20
55.0
48.0
24.0
20.0
The blower is designed to rotate clock wise when viewed from the motor side. If the blower is
running in reverse, the air volume will be approximately 1/2 the designed air volume. Also,
excessive noise will be generated. Once the motor is wired, energize the blower motor for a
brief instant (“JOG”). Check the rotation and if it is in reverse, switch any two input wires of
the 3 phases, (T1, T2, and T3).
When the reverse jet pulse cleaning system is initiated, a digital pulse control timer controls
the air solenoid valves, releasing a brief burst of compressed air backwards through the filters
to expel the collected dust off the filter cartridges and down towards the settling area.
The sequential timer can be activated by monitoring differential pressure across the filters and
energizing the timer at a predetermined set point. The timer will continue the reverse jet
pulse cleaning until differential pressure is reduced to a predetermined pressure.
Note: