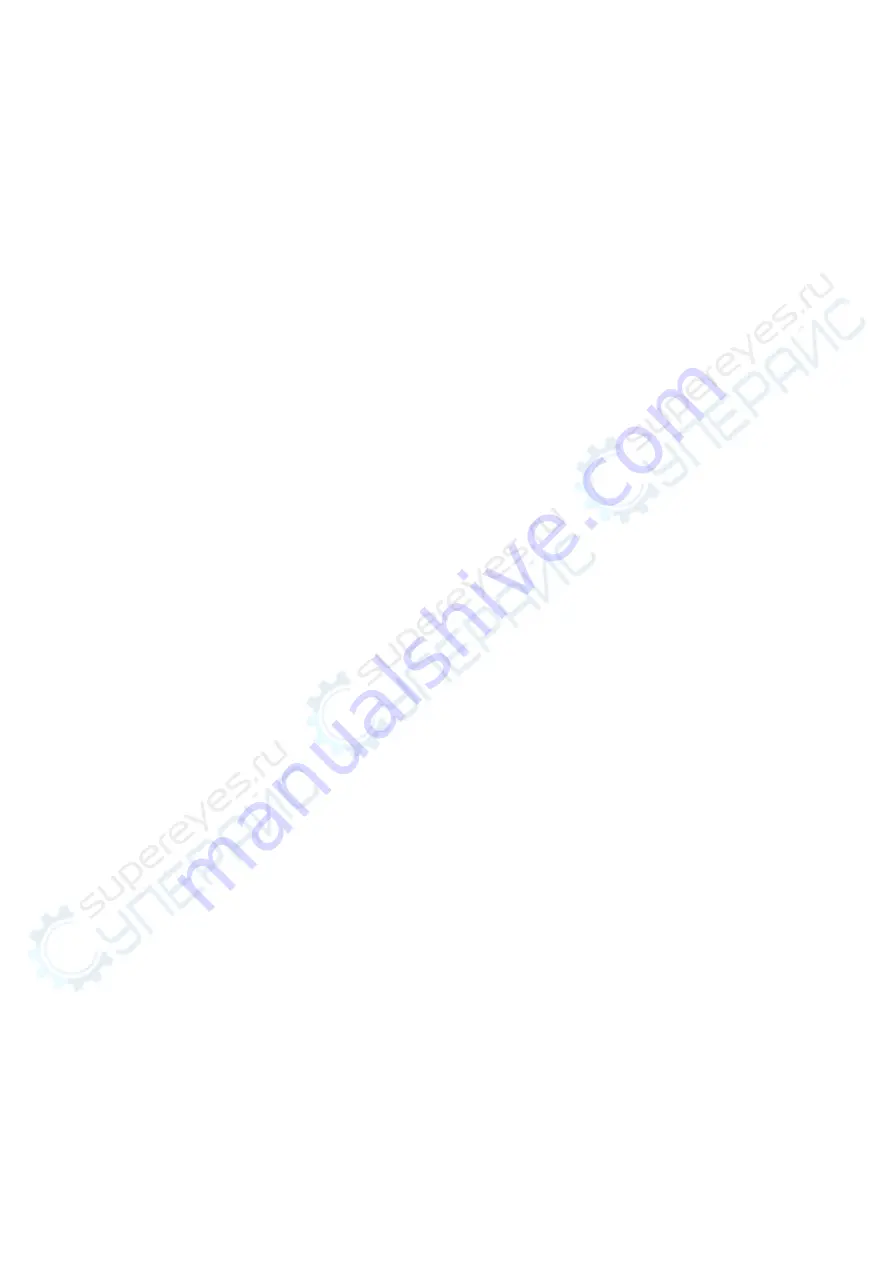
6
6.
Three temperature areas can independently heat and they are multiple temperature control,
which can ensure best integration of different temperature areas. Heating temperature, time,
slope, cooling and vacuum can all be set in the human-machine interface.
7.
There are 6-8 temperature controls up and down. Massive storage of temperature curves
which are accessible at any time according to different BGA. Curve analysis, setting and
adjustment are also accessible via touch screen. Three heating areas adopt independent PID
calculation to control heating process to enable more accurate temperature.
8. It uses high power cross-flow fan to enable fast cooling of PCB board and prevent PCB from
deformation. There are also internal vacuum pump and external vacuum chuck, which can
help to fetch the BGA chip
;
9. Collocating with sound control
"early warning" function. It can warn workers to make some
relative preparation 5-10 seconds before the completion of uninstalling or welding. Cooling
system will start after vertical wind stopped heating. When the temperature drops to normal
temperature, the cooling process will stop automatically, so that the machine will not be aging
after temperature heated up.
10. It approved CE certification, and this appliance was equipped with emergency stop switch and
automatic power-off protection device when emergency happens.
五
、
Operations:
1、
Preheating
Preheat the PCB board and BGA chip, and the temperature of constant temperature oven is usually
set at 80
℃
-100
℃
, for 4-8 hours to remove internal moisture of the PCB and BGA, to prevent
bga explose when heating.
2、Desoldering
Place the PCB board into the bracket on the repair station,and select the appropriate hot air reflow
nozzle, and set the appropriate soldering curve, press the open button until it finishes, and then
move the hot air manually,to suck the BGA chip away with the vacuum suction pen.
3
、
Clean-up
The BGA pad clean-up , one with desoldering line to drag flat, the second with iron; Best to
remove the tin a short time after the BGA removed , then BGA has not completely cooled , and the
temperature difference make less damage to the pad;use the flux can improve the activity of
soldering tin,better to clean the soldering tin. Particular attention not to damage the PCB pad,and
in order to ensure the reliability of BGA solder, when the cleaning pad to make use of some of the
solder paste residues with more volatile solvents , such as plate washer water, industrial alcohol.
4
、
BGA re-balling
Wipe the paste flux equably with the brush pen on the BGA pad, choose the right steel mesh, and
then plant tin beads by the re-balling kit on the right pad.
5、
BGA tin beads welding
Heat the bottom heating zone of BGA re-balling station and then weld the tin beads on the pad.
6、Applying
flux
Wipe the paste flux with the brush pen on the PCB pad. If you wipe so much, it will cause
connected welding, on the contrary, it will cause null welding. In order to wipe off dust and
impurity of tin balls, and enhance welding effect, the welding paste must be wiped equally.
Содержание DH-5830
Страница 9: ...9 3 3 Input password then click to enter ...