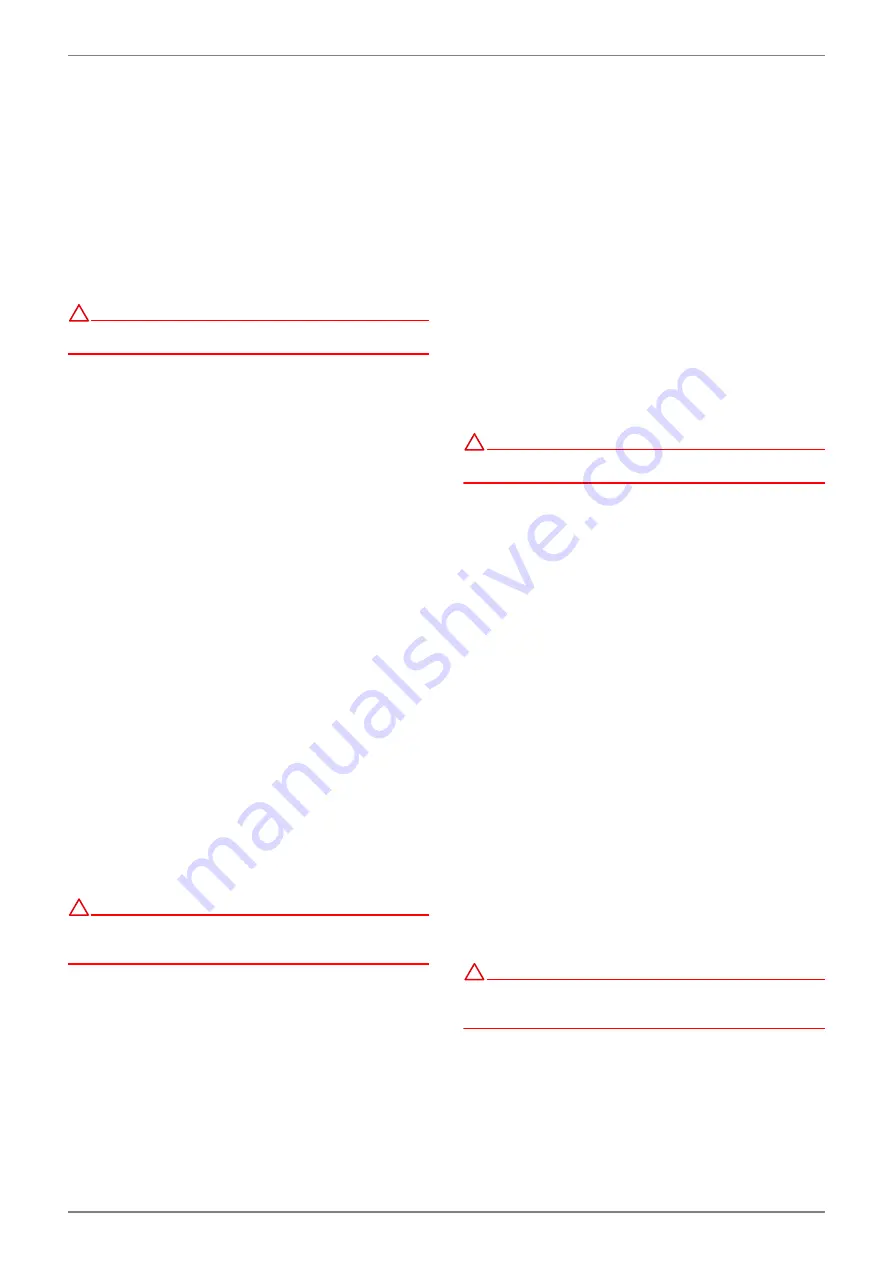
EN-10
452234.66.77 · FD 9912
www.gdts.one
English
SIH 20TE
7.5.3 Connecting an electronically
regulated circulating pump
Electronically regulated circulating pumps have high starting
currents, which may shorten the service life of the heat pump
manager. For this reason, a coupling relay is installed or must be
installed between the output of the heat pump manager and
the electronically regulated circulating pump. This is not neces-
sary if the permissible operating current of 2 A and a maximum
starting current of 12 A are not exceeded in the electronically
regulated circulating pump or if express approval has been is-
sued by the pump manufacturer.
ATTENTION!
!!
It is not permitted to connect more than one electronically
regulated circulating pump via a relay output.
8
Commissioning
8.1 General Information
To ensure proper commissioning it should be carried out by a
customer service authorised by the manufacturer. These meas-
ures can also include an additional warranty under certain con-
ditions (see Warranty).
8.2 Preparatory Steps
Prior to commissioning, the following items need to be
checked:
All connections of the heat pump must have been made as
described in Chapter 7.
The heat source system and the heating circuit must have
been filled and checked.
The strainer must have been fitted in the sole inlet of the
heat pump.
In the brine and heating circuits all valves that might impair
the proper flow must be open.
The settings of the heat pump controller must be adapted
to the heating installation in accordance with the instruc-
tions contained in the controller's operating manual.
8.3 Commissioning Procedure
The heat pump is commissioned via the heat pump manager.
ATTENTION!
!!
Start-up must be performed in accordance with the
installation and operating instructions of the heat pump
manager..
9
Care/Cleaning
9.1 Care
To prevent malfunctions due to sediments in the heat exchang-
ers, care must be taken that no im-purities can enter the heat
source system and the heating installation. In the event that op-
erating malfunctions due to contamination occur nevertheless,
the system should be cleaned as described below.
9.2 Cleaning of Heating Side
The ingress of oxygen into the heating water circuit, in particu-
lar if it contains steel components, may result in the formation
of oxidation products (rust). These can enter the heating system
via valves, circulating pumps or plastic tubing. It is therefore im-
portant - in particular with respect to the piping of underfloor
heating systems - that the installation be executed in a diffu-
sion-proof manner.
ATTENTION!
!!
To prevent the accumulation of deposits (e.g. rust) we
recommend using a suitable corrosion protection system.
In the case of severe contamination leading to a reduction in
the performance of the condenser in the heat pump, the sys-
tem must be cleaned by a heating technician.
Based on current information, we recommend using a 5 %
phosphoric acid solution for cleaning purposes. However, if
cleaning needs to be performed more frequently, a 5 % formic
acid solution should be used.
In either case, the cleaning fluid should be at room tempera-
ture. It is recommended that the heat exchanger be cleaned in
the direction opposite to the normal flow direction.
To prevent acidic cleaning agents from entering the circuit of
the heating installation we recommend that the flushing device
be fitted directly to the supply and return lines of the condenser
of the heat pump.
Thereafter the system must be thoroughly flushed using appro-
priate neutralising agents in order to prevent any damage
caused by cleaning agent residues that may still be present in
the system.
All acids must be used with great care, all relevant regulations
of the employers' liability insurance associations must be ad-
hered to.
The manufacturer's instructions regarding cleaning agent must
be complied with at all times.
9.3 Cleaning of Heat Source Side
ATTENTION!
!!
The supplied strainer must be fitted in the heat source inlet of
the heat pump in order to protect the evaporator against the
ingress of impurities.
The filter sieve of the dirt trap should be cleaned one day after-
start- up. Further checks must be set according to the level of-
dirt.If no more signs of contamination are evident, the filter can
be removed to reduce pressure drops.