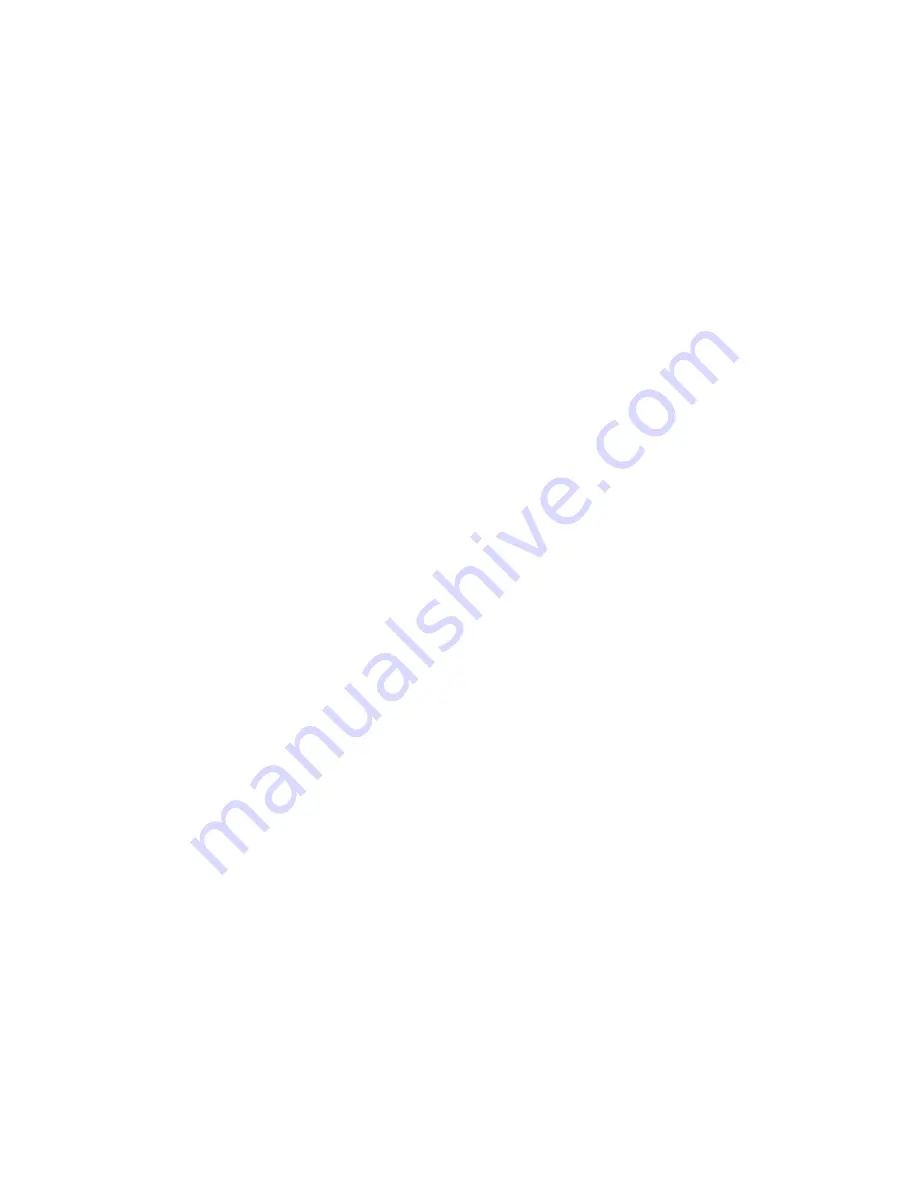
-16-
•
Insert the float hinge pin and test the movement of the float up and down and that
it moves the needle up and down in the fitting. (When held upside-down, the
bottom of the float should be parallel to the casting of the valve, in both
directions). This very important to keep the float from binding on the stem guide
as it moves up and down. If the float is not parallel to the casting , the float pin
tabs on the float will need adjusting. Hold the float firmly and bend the tabs using
needle nose pliers being gentle to not break the float from the tabs (a small crack
is acceptable). Bend both tabs down, or both up to keep float level parallel being
careful not to put pressure on the needle and seat when making the adjustments.
Check the float for sitting perfectly straight as you may need to bend one tab up
and the other tab down in order to achieve the bottom of the float straight in both
directions.
•
Replace the Top casting into the bottom casting so the metering stem slides in to
the metering guide with oil inlet on the same side as the oil overflow.
•
Replace the 2 top screws snugly, and move the control knob up and down while
tightening the 2 screws. Once tight the control knob should move up and down
freely in any position.
•
Meter the valve to the specifications above and check the overflow fuel line ( if
the float is operating correctly and adjusted parallel to the casting the oil level in
the valve will be correct.
The metering high fire screw inserted into the high temperature fuse can also be replaced
from the valve rebuild kit, or kept as a spare.
Kit Includes #02-200
1.
Float
2.
Float pin
3.
High Temp Fuse / metering screw adjustment with set screw (8-32)
4.
Extra metering screw and set screw for older valves (6-32)
5.
Replacement fuel screen
6.
Viton ‘O’ ring
7.
Needle & seat & copper/brass washer assembly
8.
Adaptor spacer for new style needle and seat
9.
Instructions