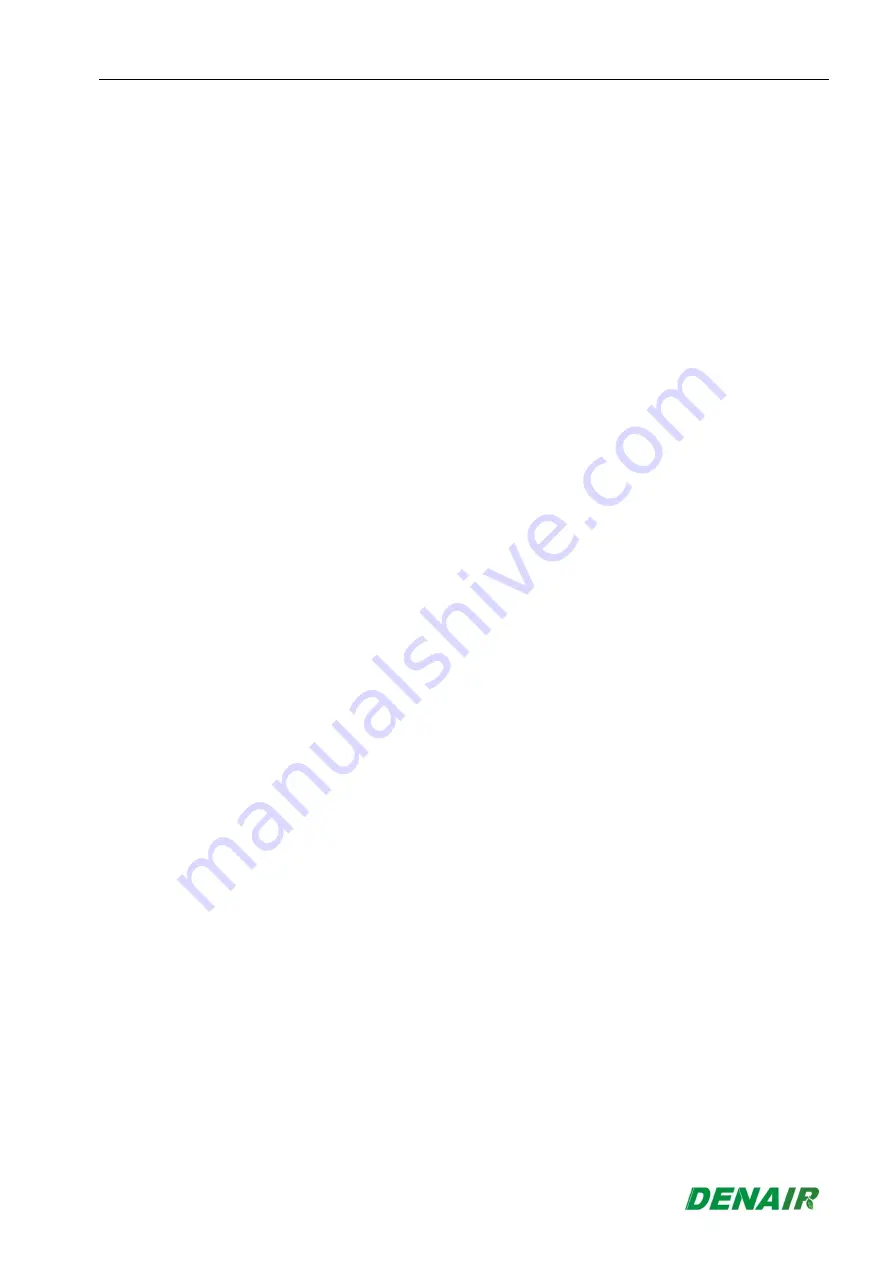
DA Series
Operation Manual
13
(1) Start-up of the electromotor (pressure drop or Y running)
The inlet valve is fully cut off, the release valve is fully opened and the release solenoid valve is
closed during this period, meanwhile the inlet side is of high vacuum and the lubricating oil required
by the compression chamber and bearings is ensured by the difference between the vacuum in the
compression chamber and the atmospheric pressure in oil-gas barrel.
(2)
Full pressure running of the electromotor (full pressure or
△
running)
The release solenoid valve is opened with power on after the control system switches to full pressure
running. When the release solenoid valve is closed, the pressure in the oil-gas barrel will gradually
rise. When the inlet valve is opened little by little, the pressure in the oil-gas barrel will rapidly rise so
that the inlet valve is fully opened and the compressor starts the heavy-load running. When the
pressure rises to a certain value, the pressure maintenance valve is fully opened and the air is
output.
(3)
Heavy-load/no-load compressor
When the pressure persistently rises to the unload pressure settings, the release solenoid
valve starts to exhaust air. The inlet valve is closed so that the air enters from the bypass pipeline
and the pressure in the oil-gas barrel starts to discharge, meanwhile the pressure maintenance valve
is quickly closed to isolate the system pressure. The pressure in the oil-gas barrel is consistently
discharge to a certain valve, i.e. the no-load pressure to provide the pressure required by
lubricating oil circulation. At this time, the air enters from the bypass pipeline and is exhausted
by the release solenoid valve after being compressed by the compressor and this circulation shows
the no-load running. When the system pressure drops to the settings of the loading pressure,
the release solenoid valve will stop discharging, the inlet valve will be fully opened and the
compressor will be running with load for a second time.
(4)
Shutdown
After pressing the STOP button, the release solenoid valve starts to exhaust air. When the
inlet valve is closed, the pressure maintenance valve will be closed, the pressure in the
oil-gas barrel will start to discharge and be isolated with the system pressure. The motor
shall stop running after the pressure in the barrel is exhausted to the no-load pressure and
the motor will be shut down after 20s.The pressure in the oil-gas barrel is consistently
exhausted to zero.
(5)
High temperature tripping or motor overloading
When the exhaust temperature is greater than 105
o
C or the motor results in current
protective device actions due to overload, the power supply will be cut off which will