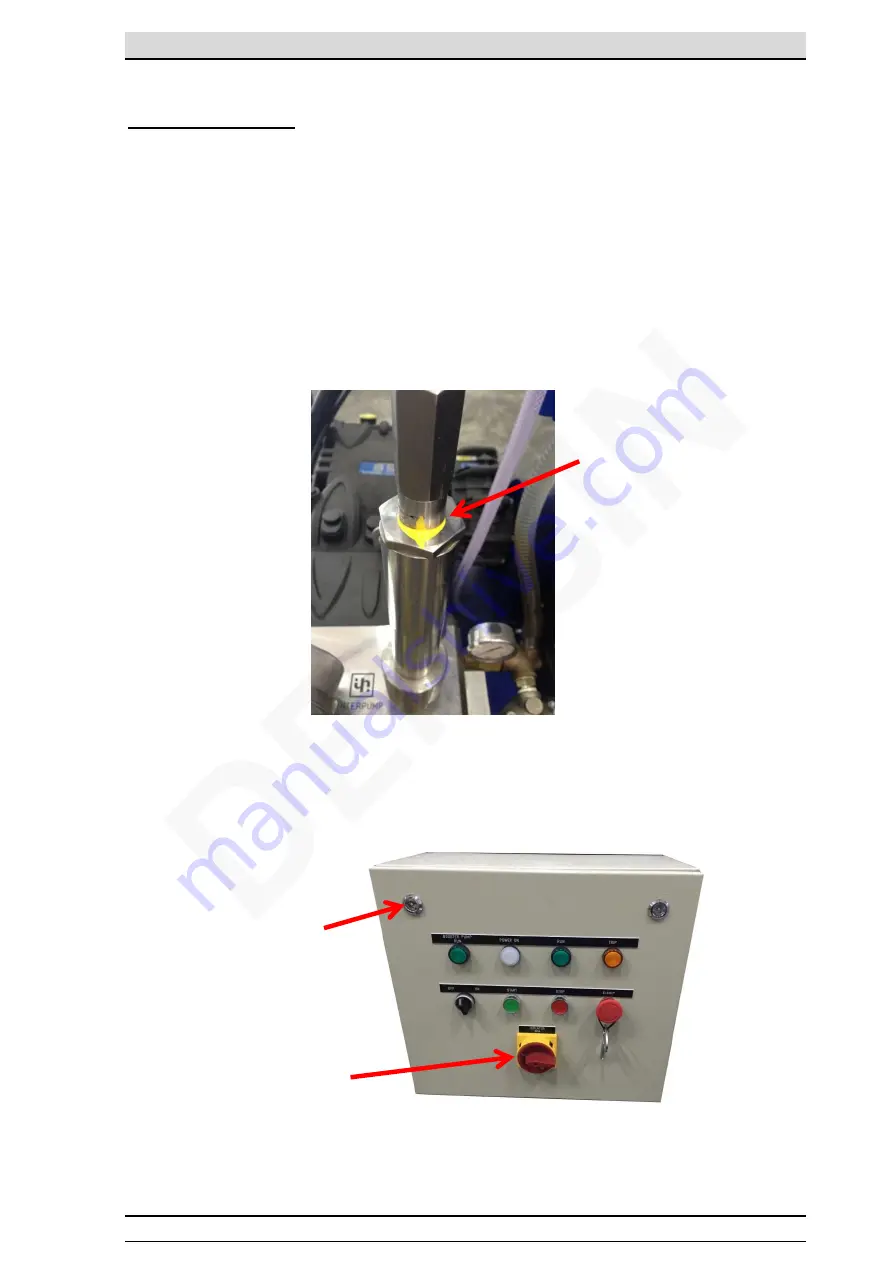
1. Getting acquainted with your Water Blaster
MERMAID E1100-I
STD00
Page 10 of 54
Unauthorized Usage
Unloader/Safety Valve
Machine’s Safety Valve are factory pre- set. Purpose of the Safety Valve is to prevent the
machine from over pressure.
Therefore, it is not recommended to adjust the setting on these valves. If setting is required, a
trained personal must performed the task. Incorrect adjustment(20~30Bar above set pressure)
to the valve may results machine damage which will cause warranty void.
To prevent unauthorized adjustment to the valves, these valves are applied with tempered
proof sealant. Once the sealant cracked, it showed that unauthorized activities occur on the
valves.
Safety Valve:
Electrical Components
To prevent unauthorized usage or sabotage, the electrical box & main switch is
equipped with locks.
Tempered Proof
Sealant
2 Locks System
Main Switch
Lock Hole
Содержание MERMAID E1100-I
Страница 33: ...4 Spare parts list MERMAID E1100 I STD00 Page 32 of 54 4 Spare parts list Frame Water Tank Assembly ...
Страница 38: ...4 Spare parts list MERMAID E1100 I STD00 Page 37 of 54 Pump assembly ...
Страница 46: ...4 Spare parts list MERMAID E1100 I STD00 Page 45 of 54 ...
Страница 47: ...4 Spare parts list MERMAID E1100 I STD00 Page 46 of 54 ...
Страница 48: ...4 Spare parts list MERMAID E1100 I STD00 Page 47 of 54 MONRO JET operation and servicing instructions ...
Страница 53: ...5 Wiring Diagram MERMAID E1100 I STD00 Page 52 of 54 5 Wiring Diagram ...