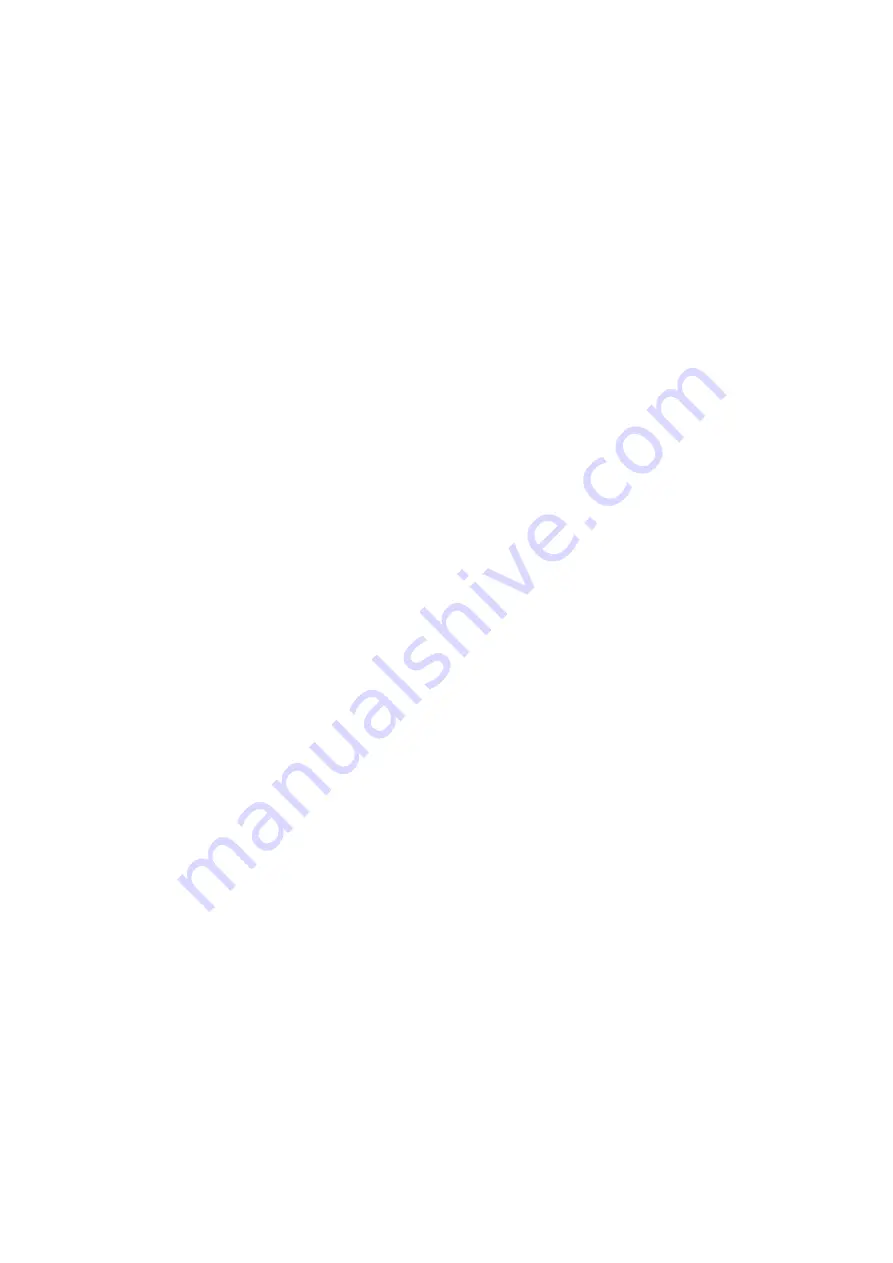
11
Figure 2-53 System settings - select axis rotation operation mode ······························ 59
Figure 2-54 System settings - displays axis rotation operation mode ··························· 59
Figure 2-55 Joint Rotation Count function mode 0 uses User Frame to teach points ······· 59
Figure 2-56 Joint Rotation Count function mode 0 does not use User Frame to teach points
Figure 2-68 External Axis Servo Switch - External Axis 1 Servo On ···························· 65
Содержание DTV Series
Страница 1: ...Handheld Teach Pendant DTV Series User Manual www deltaww com...
Страница 10: ...9 This page is intentionally left blank...
Страница 31: ...30 Figure 2 7 Edit RL enter the project name Figure 2 8 Edit RL new project created...
Страница 34: ...33 2 Tab Operation and Function Instructions Figure 2 12 Edit RL manual editing...