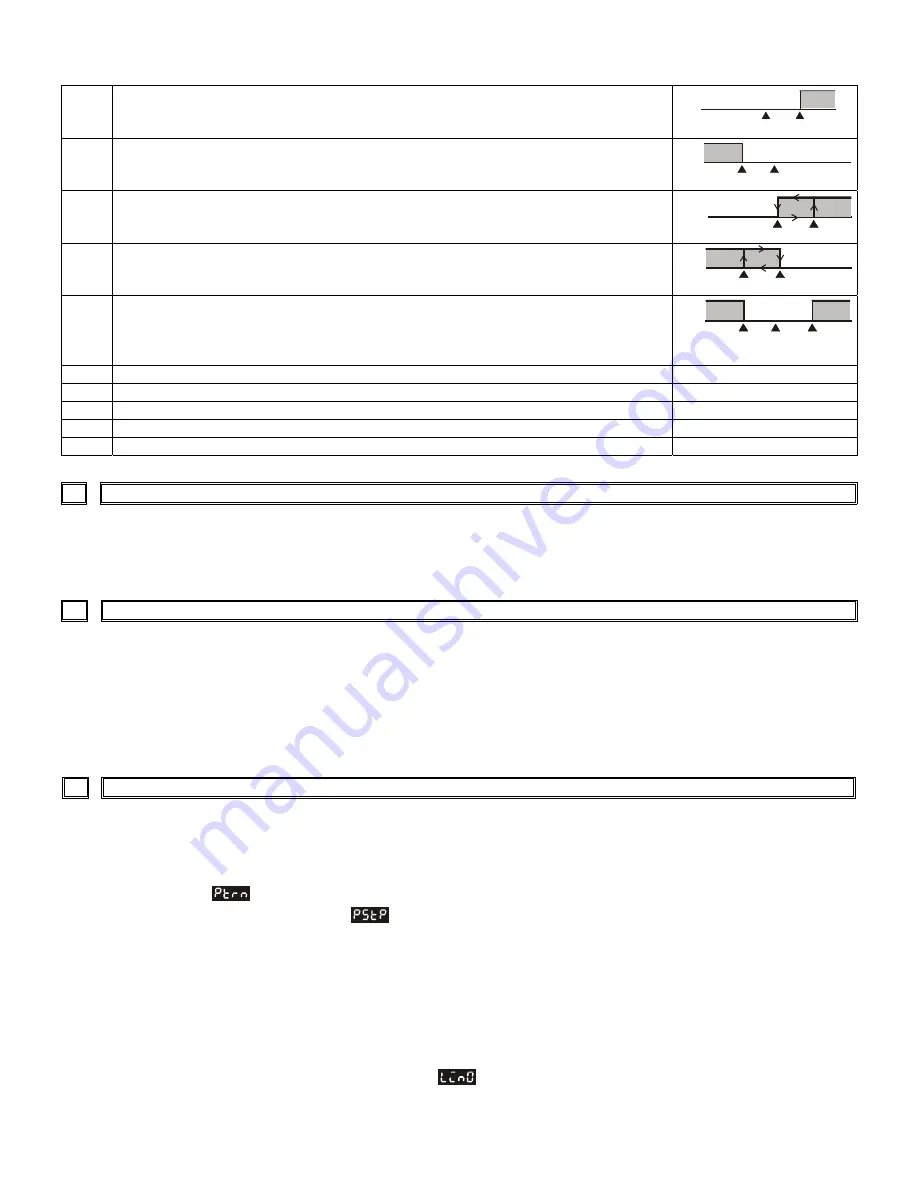
8
9
Deviation upper-limit with standby sequence:
This alarm output operates when PV value reaches set point (SV value) and the
reached value is higher than the setting value SV+(AL-H).
SV+(AL-H)
ON
OFF
SV
10 Deviation lower-limit with standby sequence:
This alarm output operates when PV value reaches the set point (SV value) and the
reached value is lower than the setting value SV-(AL-L).
SV-(AL-L)
ON
OFF
SV
11 Hysteresis upper-limit alarm output:
This alarm output operates if PV value is higher than the setting value SV+(AL-H).
This alarm output is OFF when PV value is lower than the setting value SV+(AL-L).
ON
OFF
AL-L AL-H
12 Hysteresis lower-limit alarm output:
This alarm output operates if PV value is lower than the setting value SV-(AL-H).
This alarm output is OFF when PV value is higher than the setting value SV-(AL-L).
ON
OFF
AL-H AL-L
13 CT alarm output:
This alarm operates when the current measured by transformer (CT) is lower than
AL-L or higher than AL-H (This alarm output is available only for the controller with
current transformer).
ON
OFF
AL-L
SV
AL-H
14 When program control is end status, alarm output is ON.
15 When RAMP UP status happens to PID program control, alarm output is ON.
16 When RAMP DOWN status happens to PID program control, alarm output is ON.
17 When SOAK status happens to PID program control, alarm output is ON.
18 When RUN status happens to PID program control, alarm output is ON.
Note: AL-H and AL-L include AL1H, AL2H, AL3H and AL1L, AL2L, AL3L
9
Current Transformer (CT) Function
The Current Transformer (CT) function is used with the alarm output. When using a current transformer (CT) with
the controller, change the corresponding alarm output mode to mode 13 (alarm output set value is 13), then turn
to operation mode and set the current lower-limit and current upper-limit. You can set current alarm range
between 0.5A ~ 30A, display resolution is 0.1A and measure accuracy is +/- 0.5A.
10
EVENT Inputs Function
5
There are two optional event inputs (contact inputs) supported (EVENT1and EVENT2) in DTB series.
EVENT1:
RUN/STOP operation can be executed by RUN/STOP parameters (Operation Mode) or via the
communication. User also can control RUN/STOP operation by EVENT 1 in DTB series. The control
output is ON if the circuit of EVENT 1 is open when the controller is operating. Otherwise, the
controller will stop output if the circuit of EVENT 1 is short or when the system parameter of the
controller is set to STOP mode.
EVENT2:
DTB series allows user can switch two temperature setting value by changing the status (open/short) of
EVENT 2. Each temperature setting value has independent control parameters.
11
PID Program Control (Ramp/Soak Program Control)
Description of Function and Parameters Setting:
PID program control by 8 patterns (Pattern No. 0~7) is supported in DTB series. Each pattern contains 8 steps
(step No. 0 ~ 7), one Link Pattern parameter, one Cycle parameter and one Actual Step parameter.
Start Pattern
:
is in operation mode and it is used to set the Start Pattern of PID program control (This
parameter appear in
mode only).
Steps :
Include set point X and execution time T, these two parameters setting. The set point (SV) should reach
temperature X after the period of execution time T. If the set point is the same as the result of the previous
setting, then it is called Soak program control. If not, then it is called Ramp program control. Therefore,
PID program control is also called Ramp/Soak program control. The default of step No. 0 in this controller
is Soak program control. The controller will control the temperature (PV) to reach the set point X and then
keep the temperature at set point X. The period of execution time is time T which provided by step No. 0.
Link Pattern Parameter :
For example, when set
to 2, it indicates that pattern No. 2 will execute next after