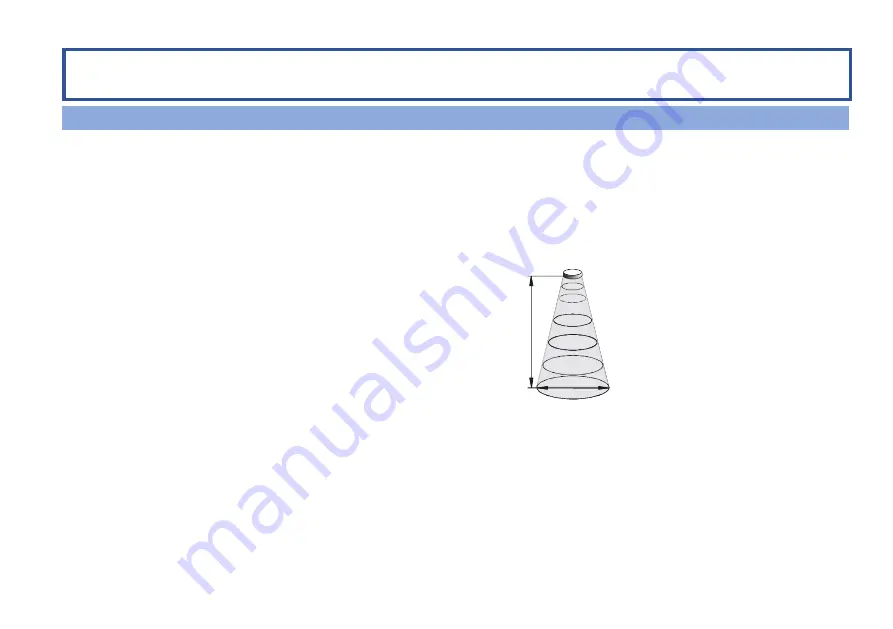
5 / 53
Thank you for choosing Delta Mobrey instrument.
We are sure that you will be satisfied throughout its use.
1.
INTRODUCTION
Application
The
DMSP400 and DMSP500
compact ultrasonic level transmitters from
DELTA MOBREY are an excellent tool for the level measurement of liquids.
Level measurement technology based on the non-contacting ultrasonic
principle is especially suited for applications where, for any reason, no
physical contact can be established to the surface of the material to be
measured.
Such reasons may include corrosive attack by the process medium against
the measuring device material (acids), possible contamination (sewage) or
particles of the process medium adhering to the measuring device
(adhesive materials).
Principle of Operation
The ultrasonic level metering technology is based on the principle of
measuring the time required for the ultrasound pulses to make a round trip
from the sensor to the level to be measured and back. The sensor emits an
ultrasonic pulse train and receives the echoes reflected. The intelligent
electronic device processes the received signal by selecting the echo
reflected by the surface and calculates from the time of flight the distance
between the sensor and the surface which constitutes the basis of all output
signals of the
DMSP400 and DMSP500
.
A Total beam angle
of 5
–
7
at -3 dB as is featured by most of DELTA
MOBREY
’s
transducers ensuring a reliable measurement in narrow tanks with
uneven side walls as well as in process tanks with various protruding objects.
Furthermore, as a result of the narrow beam angle
–
the emitted ultrasonic
signals have an outstanding focusing
–
deep penetration through gases,
vapour and foam is ensured.
rr
D
X
D
1 m
0,21 m
2 m
0,3 m
5 m
0,56 m
10 m
1 m
15m
1,45 m
X
Diameters
corresponding to
5° beam angle.
Dead Band
is a feature common to all ultrasonic level meters.
It is specified as
“Minimum measuring distance” in the Technical Data Table.
Measurement within this range can not be interpreted.
Minimum measuring distance (X
m
)
is
determined by the design of the unit
within which the measurement
is not possible (Dead Zone). This distance can be
extended by programming in order to avoid disturbing effects of possible disturbing echoes coming from fixed objects. (Close-end Blocking).
Maximum measuring distance (X
M
)
is the greatest distance (determined by the design of the unit) which can be measured by the unit under ideal conditions.
The maximum measuring distance of the actual application (H)
must not be greater than X
M
.