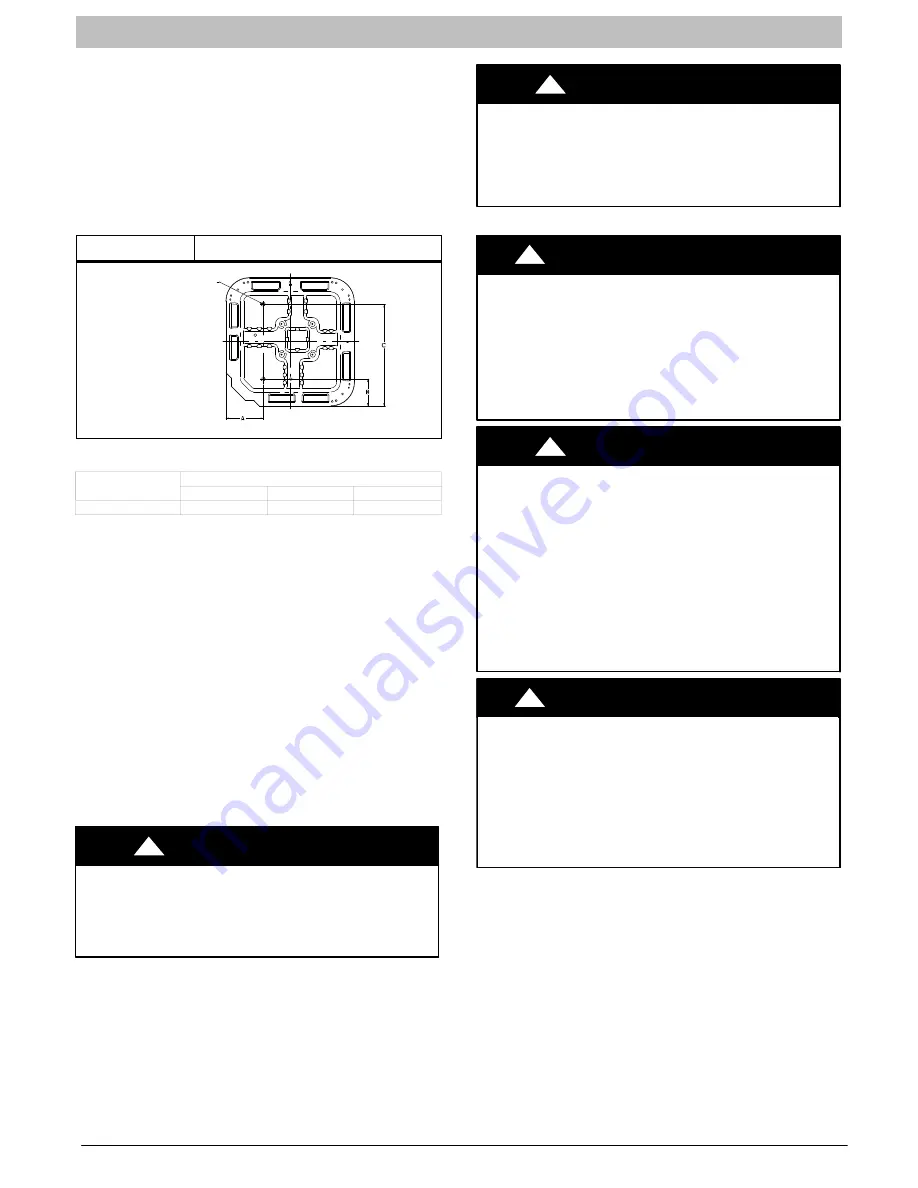
INSTALLATION INSTRUCTIONS
R
−
410A Split System Heat Pumps
428 01 1703 01
3
Specifications subject to change without notice.
Clearance Requirements
When installing, allow sufficient space for airflow clearance,
wiring, refrigerant piping, and service. Allow 24 in. (610 mm)
clearance to service end of unit and 48 in. (1219.2 mm)
above unit. For proper airflow, a 6 in. (152.4 mm) clearance
on one side of unit and 12 in. (304.8 mm) on all remaining
sides must be maintained. Maintain a distance of 24 in.
(609.6 mm) between units. Position so water, snow, or ice
from roof or eaves cannot fall directly on unit.
Figure 2
Tie Down Knockouts
3/8-in. (9.53 mm) Dia.
Tiedown Knockouts in
Basepan(2) Places
View From Top
UNIT BASE PAN
Dimension
TIEDOWN KNOCKOUT LOCATIONS in. (mm)
A
B
C
35 X 35
9–1/8 (231.8)
6–9/16 (166.7)
28–7/16 (722.3)
On rooftop applications, locate unit at least 6 in. (152.4 mm)
above roof surface.
Operating Ambient
The minimum outdoor operating ambient in cooling mode is
55
°
F (12.78
C), and the maximum outdoor operating ambient
in cooling mode is 125
°
F (51.67
C). At line voltage of 208V
(or below) and an outdoor ambient of 120
°
F (48.9
°
C) (and
above), the compressor operates in low stage The maximum
outdoor operating ambient in heating mode is 66
°
F
(18.89
C). 16 SEER product is approved for low ambient
cooling operation down to an ambient as low as 0
°
F
(
−
17.78
C) with low ambient accessory kits. 19 SEER
product is not approved for low ambient cooling applications.
Elevate Unit
CAUTION
!
UNIT DAMAGE HAZARD
Failure to follow this caution may result in equipment
damage or improper operation.
Unit must be kept free of an accumulation of water and/or
ice in the basepan.
Elevate unit per local climate and code requirements to
provide clearance above estimated snowfall level and ensure
adequate drainage of unit. If using accessory support feet,
use installation instructions from kit for installation.
CAUTION
!
UNIT DAMAGE HAZARD
Failure to follow this caution may result in equipment
damage or improper operation.
To prevent damage to the unit, ensure that it is located
with the supports such that the unit is stable in all
circumstances including adverse conditions.
Make Piping Connections
!
WARNING
PERSONAL INJURY AND ENVIRONMENTAL
HAZARD
Failure to follow this warning could result in personal
injury or death.
Relieve pressure and recover all refrigerant before system
repair or final unit disposal.
Use all service ports and open all flow
−
control devices,
including solenoid valves.
CAUTION
!
UNIT DAMAGE HAZARD
Failure to follow this caution may result in equipment
damage or improper operation.
Do not leave system open to atmosphere any longer than
minimum required for installation. POE oil in compressor is
extremely susceptible to moisture absorption. Always keep
ends of tubing sealed during installation.
If ANY refrigerant tubing is buried, provide a 6 in. (152.4
mm) vertical rise at service valve. Refrigerant tubing
lengths up to 36 in. (914.4 mm) may be buried without
further special consideration. Do not bury lines more than
36 in. (914.4 mm).
!
WARNING
PERSONAL DAMAGE HAZARD
Failure to follow this warning may result in equipment
damage or improper operation.
To prevent damage to unit or service valves, observe the
following:
Use a brazing shield.
Wrap service valves with wet cloth or use a heat sink
material.
Outdoor units may be connected to indoor section using
accessory tubing package or field
−
supplied refrigerant grade
tubing of correct size and condition. For tubing requirements
beyond 80 ft/24.38 m, substantial capacity and performance
losses can occur. Following the recommendations in the
Long Line Applications Guideline will reduce these losses.
Refer to Table 1 for accessory requirements. Refer to Table 2
for field tubing diameters.
If refrigerant tubes or indoor coil are exposed to atmosphere,
they must be evacuated to 500 microns to eliminate
contamination and moisture in the system.